Friday, February 28, 2014
How to Repair an Exhaust Muffler

Exhaust systems are regulated by the government. Many states emissions tests require that the exhaust system, including the muffler, is fully functional and efficient. The muffler is one of the easiest portions of the exhaust system to monitor--either it is working or it is not. You can repair the muffler to address some issues, but you must replace it to fix most problems. A quick troubleshooting session can help determine what action is necessary.
Instructions
- 1
Turn the vehicle off. For added safety, if the vehicle was recently run, allow it time to cool down because a muffler tends to get hot during operation.
2Jack the car up high enough to see under the rear, following your manuals jacking procedure instructions.
3Verify that the muffler is attached to the exhaust pipe. If it is not, take it to a local welder or exhaust shop to have it reattached.
4Inspect the muffler to ensure it is whole and the mufflers body does not have visible holes or dents.
5Replace the muffler immediately if there are signs of damage. Obtain a new muffler from your local parts store. With the rear of the car still jacked in the air, locate brackets that are holding the muffler in place. Loosen the brackets and slide the muffler out towards the rear of the vehicle.
6Slide the new muffler into place, just as the previous muffler was. Utilize the mounting brackets to tighten the muffler back into place. Lower the car by releasing the jack slowly. Start the car and observe the muffler to ensure that exhaust is exiting the muffler port.
1996 Honda Odyssey Problems

Whether you purchased your 1996 Honda Odyssey the year it came out, or you purchased a used model, there have been problems reported by consumers regarding this car. Always make sure your car is covered by a warranty because repairs will more than likely be needed.
2009 Recall
In May of 2009, Honda recalled all Odysseys that were manufactured in 1996 due to the headlamps failing to conform to the requirements of the Federal Motor Vehicle Safety Standard No. 108. The lamps in the 1996 Odyssey did not contain the required amber side lectors.
Ignition Problems
Over 500,000 1996 Honda Odysseys had problems with faulty ignition switches that caused the vehicle to shut down while traveling at both low and high speeds. Most of these vehicles were manufactured in China, and exported into North America.
SRS Control Module
Several complaints have been filed stating that after a replacement battery has been installed in the 1996 Honda Odyssey, the SRS light would come on. Upon inspection by mechanics, a conclusion came about that the SRS control module needed to be replaced and the cost would be around $700.
Thursday, February 27, 2014
How do I Change a Fog Light Bulb on a 2005 Chevy Monte Carlo

Although not as important as the headlights, a vehicles fog lights still make driving safer and easier when there is a lot of fog in the area. When there is a malfunction with the fog lights, they must be replaced as quickly as possible. Thankfully, replacing a fog light on the 2005 Chevrolet Monte Carlo is a simple process that does not take much time.
Instructions
- 1
Turn off the Monte Carlo and put on the gloves. Whenever working in or under a vehicle, gloves should be worn for safety reasons.
2Place the jack under the vehicle and raise it to a comfortable level. Whereas the headlight assembly is accessed through the hood of the car, the fog lights can only be reached from underneath.
3Unplug the electrical wire connection that is connected to the fog lights. The connection is located under the vehicle, plugged into the fog lights. This will allow you access to the fog light assembly.
4Remove the bulb socket by twisting and pulling it from out of the fog light assembly. Remove the old bulb by pulling it out of the assembly.
5Insert the replacement bulb into the assembly and lock it into place. Reattach the socket by twisting it back onto the fog light assembly. Reconnect the electrical wire connection to the fog light assembly and lower the Monte Carlo back onto the ground.
The Average Cost to Have Cylinder Heads Milled

Car engines perform fast actions, such as the pistons moving within the cylinders, over many years of use. If the engine begins to fail, cylinder heads can be milled to bring the engine back into proper performance standards.
Function
Typically, milling engine cylinder heads is part of a larger repair called an engine rebuild. The lower portion of the engine block is detached, inspected and cleaned. The cylinder heads are then resurfaced to properly seat the pistons and rings within the cylinders body.
Expert Insight
Cars Direct estimates that a common four-cylinder engine rebuild can cost from $400 to $500, and as the amount of cylinders increases, so does the pricing. A six-cylinder vehicle costs about $500 to $600, and an eight-cylinder increases to between $600 and $700. Estimates are as of early 2011.
Considerations
The extent of damage to the cylinder heads can increase the cost of rebuilding. The more resurfacing that is needed requires extra labor hours to create the correct effect for a properly functioning vehicle.
Wednesday, February 26, 2014
How to Repair Window Rubbers
The rubber part of a cars window is erred to as a window rubber. It protects the window as it slides in and out of the car door. Many times, a window rubber can become dry and cracked from weather conditions or from improper maintenance. Window rubbers can also shrink over time. With just a few supplies, they are easy to repair.
Instructions
- 1
Wash the window rubber thoroughly with soap and water. Any type of soap will do; dishwashing soap works well. Wash with a sponge to avoid causing additional damage with the pressure from a hose.
2Dry with a lint-free towel. If the rubber is cracked, a traditional towel can get cut on it, or leave lint behind.
3Apply urethane sealer to the rubber with a paintbrush or applicator pad. Thoroughly coat cracked and chipped areas.
4Cure the urethane overnight. Curing is allowing it to dry before exposing it to the elements, including sunlight and extreme heat.
How to Change the Water Pump on a Cummins 5 9L Turbo Diesel

The Cummins B Series of engines are diesel engines for trucks and industrial applications. The six-cylinder, 5.9-liter version has appeared in Dodge Ram trucks since 1989. These engines are turbocharged and require an effective cooling system to prevent the engine from overheating. The water pump in a Cummins 5.9-liter diesel engine is on the front of the engine, below the cooling fan. The replacement of the water pump in this engine requires the removal of additional components.
Instructions
- 1
Remove the cable from the negative terminal of both batteries with a socket wrench. Place a drain pan under the radiator drain and remove the drain plug. Wait for the coolant to drain from the radiator and replace the drain plug.
2Detach the electrical connectors from the air temperature sensor and the mass airflow sensor if your vehicle is so equipped. Detach the inlet tube for the turbocharger and remove the housing for the air filter with a socket wrench. Remove the alternator assembly.
3Rotate the tensioner assembly clockwise with a long-handled wrench to relieve the tension on the accessory drive belt, then disconnect the belt. Remove the mounting bolts for the water pump with a socket wrench and disconnect the water pump from the engine. Remove and discard the O-ring from the water pump.
4Install a new O-ring onto its mounting groove on the water pump. Install the water pump so that the weep hole on the water pump faces down. Torque the mounting bolts for the water pump to 18 foot-pounds with a torque wrench.
5Install the accessory drive belt with a long-handled wrench. Connect the alternator assembly and torque its mounting bolts to 30 foot-pounds with a torque wrench. Install the air filter housing and attach the inlet tube for the turbocharger. Attach the electrical connectors to the air temperature sensor and mass airflow sensor.
6Refill the radiator with coolant and connect the cables to the negative battery terminals with a socket wrench. Start the engine and allow it to warm up. Check and correct any coolant leaks.
Instructions for Reflooring a Horse Trailer

Horse trailer flooring takes a lot of abuse. It supports animals of several thousand pounds, while the trailer itself is bounced and pounded by the roadway, sometimes at speeds of 60 or 70 miles per hour. Replacing the flooring is done with the same techniques you would use to replace the flooring in any trailer. Use treated lumber for the boards to add life to your trailers floor. If your trailer does not have a rubber mat, adding one can add years to the life of your trailer floor and save wear and tear on the horse.
Instructions
- 1
Remove the rubber mat from your floor. These are heavy duty rubber, without fasteners to allow for thorough cleaning. Lift the mats and remove them from the trailer. Lift the trailer onto jack stands, or concrete blocks. Using a standard auto jack to lift one end, slip the jack stands under, lift the other end and slip stands under to provide better access to the bolts underneath.
2Cut the bolts, just above the nut, with a reciprocating saw. Tap the bolts up through the floor and pull them out on top with a claw hammer. Remove the floor boards from the trailer, one at a time, laying them out in the same order you removed them, to serve as a template for the new boards.
3Cut one piece of 2 inch-thick treated lumber for each board. Use boards the same width and cut to the same length as the original using a circular saw. Typical floor boards range from 2-by-6 to 2-by-10, but are usually standard sizes. Drill the bolt holes through each board, using the original board as a template. Use a bit the same thickness as your new bolts.
4Fit each board into place, working it under any edge flanges to get a smooth fit. Set the board in with its front end tipped up, slide the back end under the edge of the rear door sill and tap it down with a hammer until it drops into place. Tap a bolt down through each hole in the floor boards, through the frame of the trailer. Fit every board and bolt before adding nuts and washers underneath.
5Fit a washer and nut over the end of each bolt, turning it tight by hand. Fit all washers and bolts, then tighten all nuts with an impact driver. Remove the trailer from the jack stands and replace the rubber mats over the new floor boards.
Tuesday, February 25, 2014
How to Change a Light in a Chevy Tahoe

The Chevrolet Tahoe is an SUV introduced in 1995. The lights on your Tahoe must all be in working order for your safety as well as for fellow drivers; if not, you may be pulled over by your highway patrol and issued a fix-it ticket. Replacing any of the lights is a simple process, requiring nothing more than a screwdriver and a replacement bulb. Although the bulb types differ for each light, they are all available at most automotive parts suppliers.
Instructions
Headlights
- 1
Turn off the Tahoes engine and open the hood. Remove the two pins from the top of the headlamp assembly by twisting them inwards and pulling them out.
2Pull the headlamp assembly out of the vehicle and unplug the electrical wire. The larger socket is the low-beam headlight and uses 9006-type bulbs. The smaller socket is the high-beam headlight and uses 9005-type bulbs. Rotate the desired bulb counterclockwise and remove it from the assembly.
3Push the new bulb into the assembly and rotate it clockwise to lock it into place. Reconnect the electrical wire to the rear of the assembly and place it back into the vehicle.
4Reinstall and tighten the two pins above the headlamp assembly. Close the hood.
Front Turn Signal, Side Marker and Daytime Running Lamps
- 5
Remove the headlamp assembly by following the steps outlined in Section 1. This will allow access to the turn signal assembly. Press down on the retainer clip to release the assembly.
6Pull the assembly out of the vehicle. The smallest socket is the side marker lamp and uses 3457A-type bulbs. The largest socket is the turn signal lamp and uses 3457A-type bulbs. The remaining socket is the daytime running lamp and uses 4114K-type bulbs. Press the locking release lever on the desired socket to release it then rotate it counterclockwise to remove it from the assembly.
7Pull the old bulb out of the socket and place the new bulb into the socket. Place the socket back into the assembly and rotate it clockwise to tighten it.
8Reinstall the turn signal assembly into the vehicle. Reconnect the electrical wire. Place the headlamp assembly back into the vehicle, making sure to reconnect the electrical wire and reinstall the two pins. Close the hood.
Side Identification Marker Lamps
- 9
Locate the lap gasket near the rear wheel. Pull back the edge of the gasket in order to expose the service slot.
10Push into the slot with a screwdriver to release the side marker assembly. Pull the housing out and unplug the lamp assembly harness. Remove the old bulb and place the replacement bulb into the vehicle. The side marker lamps use 194-type bulbs.
11Reattach the lamp assembly harness and snap it into the housing. Reinstall the lamp assembly into the vehicle.
Roof Marker Lamps
- 12
Use a screwdriver to remove the six screws on the front of the roof marker assembly. This assembly is located on the top of the Tahoe. Once the screws are removed, lift off the lens from the assembly.
13Turn the old bulb counterclockwise to remove it from the socket. The roof marker lamp uses 194-type bulbs.
14Push a new bulb into the socket and rotate it clockwise to lock it into place.
15Reinstall the lens and tighten all six screws.
Tail Lamps
- 16
Remove the two screws from the tail lamp assembly. Pull the assembly out of the vehicle.
17Press down on the release tab and rotate the desired bulb socket counterclockwise to remove it from the assembly. The top socket contains the turn signal bulb, the middle socket contains the back-up bulb and the bottom socket contains the brake light bulb. All three lights use 3157-type bulbs.
18Pull the old bulb straight out of the socket and replace it with a new bulb. Place the socket back into the assembly and rotate it clockwise until it clicks into place. Reinstall the tail lamp assembly and reattach the two screws.
Monday, February 24, 2014
How to Replace Side View Mirrors

The side view mirror on most late-model domestic and import vehicles connects to an electric motor located inside a larger plastic mirror enclosure that bolts to the side of the door. The enclosure is made of highly durable ABS plastic to help reduce the likelihood of breaking the mirror if struck by a passing car. On occasion, the mirror, not the enclosure, takes a direct impact and the mirror cracks. If this happens, you can replace the mirror without replacing the enclosure.
Instructions
- 1
Push one side of the mirror into the enclosure. If changing the driver mirror, push the right side of the mirror into the enclosure. If you are changing the passenger mirror, push the left side of the mirror into the enclosure. This pushes the other side of the mirror out of the enclosure so you can reach behind it.
2Grasp the mirror by wrapping your fingers behind the mirror and pressing on the face with your thumb. Pull the mirror out of the assembly. The mirror glass has a metal clasp on the back that holds the mirror onto the mirror motor inside the enclosure. Pulling on the mirror releases the clasp and allows the mirror to pop off the motor.
3Place the new mirror into the enclosure with the same side pushed into the enclosure. Pop the clasp back onto the mirror motor by pushing on it until you hear it snap into place.
How to Remove the Heating Panel on Dashboard of a 2002 KIA Spectra Car
The 2002 Kia Spectras heating control panel is located directly beneath the cars radio. This control panel also has the switch for the Spectras fan controls and air conditioner. If the heating control panel is malfunctioning, you may want to consider replacing it. The first step toward doing so is removing the faulty control panel from the car. The control panel is attached to the Spectras front dash cover.
Instructions
- 1
Disconnect the Spectras negative battery cable with pliers or a wrench. Inspect the dash to find the two Phillips screws on the underside of the odometer hood.
2Remove the two Phillips screws. Grasp the dash cover and pull the top edge of it downward to unhook it. The heating control panel will come out with it. Examine the back of the dash cover to view the back of the heating control panel.
3Unplug the wiring harness from the heating control panel. Around the heating control panels perimeter, youll find four Phillips screws.
4Remove the four Phillips screws. Pull the heating control panel out of its mount to remove it.
How Do I Unfreeze the Lock on My Gas Cap
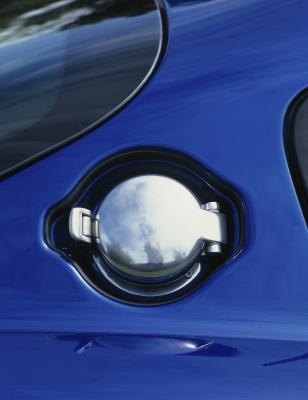
Finding your locked gas cap frozen can be more than an inconvenience, especially if youre nearly out of fuel and need to fill the tank. Although you can use hot water to unfreeze a gas cap lock, this could result in water leaking into the gas tank. If youre at the gas station, you may not have access to conventional methods such as de-icing sprays or hairdryers, but there are methods to unlock the cap without them. If you live in a cold weather climate or the lock freezes frequently, keep remedies for thawing it with you in the vehicle.
Instructions
- 1
Heat the key on the engine while the car is running and try inserting it in the lock. If the key is warm enough, it will thaw the lock. You may have to repeat this several times. Its a handy method if you dont have any other method of thawing the cap available in the car. The key can also be heated with a match or cigarette lighter.
2Wet a cloth with warm or hot water and lay it over the lock. Avoid pouring hot water on the lock, as this may compound the problem if the water reezes or gets into the gas tank.
3
Spray de-icer on the lock and the key. Use it sparingly on the lock. Spray the lock caully to avoid getting the de-icer into the gas tank.
4Direct hot air from a hand-held hairdryer at the lock if youre at home, in a garage or close to an outlet that will allow you to use one.
5Use a cardboard cylinder from a paper towel or toilet paper roll. Place one end over the lock and breathe through the other. Your warm breath may help thaw the lock. This may take some time.
Sunday, February 23, 2014
How to Fix Rock Chips in Paint
A rock-chipped area on your cars paint can turn into rust if you let it go without repairing it. Repairing it immediately after it happens ensures that it does not become a bigger problem in the future. Fixing rock chips in your auto paint is not a hard repair, and in most cases can be done without a professional.
Instructions
- 1
Look up the year, make, and model of your car in the paint section of your local auto parts store. There will be a booklet that lists the colors that were used that year for your car. Find your paint color using that list. Dealers may have the paint you need as well, but in many cases will not sell a small enough amount to make it budget friendly to buy for small chip repairs.
2Clean the chipped area with soap and water. This will remove any debris and ensure that the area is clean when you apply the paint. Dry the area with a soft cotton cloth.
3Rub auto polish over the chipped area. This will help to soften any edges that are ragged on the chipped surface. Too much rubbing could damage the existing clear coat on your car by making it appear cloudy. Take care not to rub more than 10 or 12 times in a smooth, circular motion.
4Clean the finish with denatured alcohol. Do not pour the alcohol directly on the car. Instead, pour some onto a soft cloth first. Wipe along the chipped area. This will remove any polish that still remains and any grime that is left on the car.
5Apply primer using the wrong end of a match, also known as the butt end of the match. The size of the match makes it perfect for touching up small chips. Dip it into the paint and then fill the area inside the chip, allowing it to just slightly touch the paint that is around it. Allow time to dry according to manufacturer instructions. It typically takes up to half an hour.
6Paint over the primer with your touch-up paint. It usually will come with a brush inside the bottle. Test it on a piece of paper first if you are worried that it will not match your car color. The more coats you put on the paper to test, the more closely the color will match how it dries on your car. Wait an hour and apply another coat. Let the paint sit for several days. Lightly sand the edges or raised area of paint with fine-grit paper. Gently polish the area to blend in the edges of your repair.
Subaru 3 0 Engine Problems
Starting in the late 1990s, Japanese automaker Subaru installed a 3-liter hemispherical (Hemi) six-cylinder engine called the EZ30 on some of its vehicles -- namely the Tribeca, Legacy and Outback, which is the wagon offshoot of the Legacy. The Outback has experienced problems.
Major Problems
Some Subaru Outbacks of the 2001 to 2003 model years may experience failures of the catalytic converter, air-fuel ratio sensor, knock sensor and/or the cylinder head gaskets. These problems can trigger the "Check Engine" light, and drivers may experience engine stalling, coolant leaks or overheating.
Minor Problems
Although the 2004 Subaru Outback is virtually free of the aforementioned issues, it has an occasional problem with the failure of the oxygen sensor. This causes the "Service Engine Soon" indicator to illuminate, and the vehicle could fail emissions.
Cost of Repair
As of December 2010, MSN.com estimates repair costs as follows: $1,055 to replace the catalytic converter, $200 for the air fuel ratio sensor, $162 for the knock sensor and $595 for the cylinder head gaskets. In some extreme cases related to the aforementioned problems, the mechanic working on the vehicle may need to reprogram the engine control module as well; this can cost an extra $98 for labor. The oxygen sensor is estimated at around $238.
Saturday, February 22, 2014
200R4 Technical Information

The 200R4 is the model number of a transmission introduced by General Motors (GM) in 1982. This transmission is compatible with the GM Chevrolet, Buick, Pontiac and Cadillac brands. Owners can obtain key information about the transmissions workings in their cars by reviewing their history, critical systems, gear ratio, dimensions and horsepower.
History
GM introduced the GM 2004R as an overdrive version of the three-speed GM THM300 model. It offered a vast improvement in strength and durability over the THM200. Because the 200R4 was similar in size to the GM TM400 model, the 200R4 eventually replaced the THM 400 model.
Critical Systems
The internal hydraulic pump is the most critical part of the 200R4 transmission. The pump housing is precision-machined. Because of this precision, its performance level is impervious to heat, pressure and the age of the transmission.
Gear Ratios
The first gear ratio is 2.74-to-1, the second gear radio is 1.57-to-1, the third gear ratio is 1.0-to-1, the fourth gear ratio 0.67-to-1 and reverse is 2.07-to-1.
Dimensions
From the dimensions and the fit, an owner can determine the size, make and model of vehicle with which the transmission is compatible. The overall length of the transmission is 27- 11/16 and height is 19 1/8 inches.
Horsepower
The 200 R4 can reach up to 500 horsepower and requires a 12-volt feed to control the torque converter.
How to Replace Broken Car Keys

A major inconvenience that most people dont consider when going about your daily life is the possibility that your car key could break. You might expect that on occasion youll experience a flat tire or a dead battery, but a broken car key usually doesnt cross your mind. Unfortunately, keys do break. And when they do, it is imperative that you locate your spare key or contact the correct person or company to obtain a new car key. After all, the most important part of a working vehicle is a key to operate it.
Instructions
- 1
Use your spare keys until you can obtain new keys for your car.
2Call your local car dealerships service department to order a new key. If you have a late model car that uses a transponder key embedded with a computer chip to match that of your vehicle you will need to purchase a new key from an authorized vehicle dealership. Expect to pay a large fee for a new transponder key, as they run anywhere from $150 to $250 per key, depending on the make and model of your vehicle.
3Provide the vehicle service department with the vehicle identification number of your car. The location of the VIN depends on the type of car you drive. It could be on your drivers side windshield, viewable from outside of your car or it could be located on the door panel of the drivers side. VINs are always located on purchase paperwork, insurance information and registration forms. The VIN contains the key code for your specific vehicle, which allows the key maker to know exactly how to cut your new key.
4Pick up your replacement key and test it on your vehicle.
Friday, February 21, 2014
How to Fix a Harley Davidson Oil Leak

The name Harley Davidson is synonymous with motorcycles, a desert landscape, street cool and rebelliousness. Some famous riders include actors Brigitte Bardot, Peter Fonda and Elizabeth Taylor. It is also the motorcycle for the notorious gang, Hells Angels, which is most popularly linked to crime and drugs. Harley-Davidson may evoke a glamorous image but even this is not a perfect brand. Even the most expert rider will probably have to tend to an oil leak at some point in his lifetime.
Instructions
- 1
Check from where the leak is occurring to locate the problem. Make sure to check for any holes in the fuel, oil, or hydraulic tanks. Check both the cases and the lines for leaks. The leak may not be directly from the tank but could be a mixture of oil, water and air, blackened to look like an oil leak. Checking the source of a possible leak should be a regular practice anyway to ensure you are not left without fuel in the middle of nowhere.
2Wipe away excess oil. According to Harley Davidson Maintenance, the initial thoughts of a rider when he finds oil formation on the right side of the engine is that the oil leak is caused by a damaged push rod tube seal. In this case, the tube should be replaced. A replacement tube can be found by looking at Harley Davidson parts retailers.
3Take your bike to a mechanic who specializes in Harley Davidson motorcycles. If the problem is recurring, your best bet is to take it to an expert mechanic. He or she may have to tear out the engine to look for the cause of the oil leak and this is best left to an expert. Affordable mechanics can be found on the Internet.
How to Repair a Volvo S70 Window Switch
The Volvo S70 is a great mid-size luxury car from a Sweden. It comes with many luxury amenities standard, such as power windows. However, European car electronics do have a higher than average failure rate, so to avoid exorbitant import repair costs, you can repair the switch yourself. The switch controls the position of the window by controlling an electrical motor. The switch itself could have damage or the wires leading from the switch could be frayed.
Instructions
- 1
Drive the Volvo S70 to a garage or other covered area, perably a garage though. You do not want to work on the cars electronics out in the open in case it starts to rain or precipitate. Put the Volvo S70 into "Park" and then engage the parking brake to keep the car from moving while you work on it. Turn the Volvo S70 off and pull the key out of the ignition.
2Open the door with the window switch that you want to repair. Open it all the way so you have the most room to work with. Take a thin flathead screwdriver and wedge the tip into the seam around the window switch and the armrest bezel. Pry the switch out gently and pull it out by hand, but do not disconnect the wires yet.
3Inspect the switch for any obvious damage. If the switch itself is damaged then unplug the control wires from the switch. Plug the wires plugs into the port on the new switch and place it back in the armrest. If the switch is fine but there is corrosion on the wires, then pull the wires up and out of the port at the bottom of the switch well. Plug the replacement wire into the port at the bottom of the switch well and then into the old switch.
4Wedge the switch back into the armrest and then turn the Volvo S70 on. Roll the window up and down to test the window switch. If it does not work then pry the switch out again to make sure the wire plugs are firmly pushed into the port.
Thursday, February 20, 2014
How to Replace a Signal Light on a 1996 Subaru Impreza Outback
The turn signal bulbs on your 1996 Subaru Impreza are 1156 or 194 bulbs available from most auto parts retailers and Subaru dealerships. When a front or rear turn signal bulb fails on your Impreza, replace the bulbs at home to get your car back on the road within minutes without the need to spend time in a service center waiting room.
Instructions
Front Turn Signal
- 1
Remove the two screws on the lens cover with a Phillips screwdriver. Pull the lens assembly forward until the wiring harness is accessible. Squeeze the tab on the wiring connection, and pull it apart.
2Twist the bulb and socket counterclockwise, then pull it out of the light assembly. Turn the bulb counterclockwise, and remove it from the socket. Insert the new bulb into the socket, and turn it clockwise.
3Position the light assembly in the front of the car, and secure it with the mounting screws. Tighten the screws with a Phillips screwdriver. Repeat the process on the opposite light if needed.
Rear Turn Signal
- 4
Open the rear hatch of the Impreza Outback edition. Pull the cover off the rear of the taillight assembly.
5Turn the socket assembly counterclockwise to remove it from the light. Turn the bulb counterclockwise, and pull it straight out of the socket. Insert the new bulb into the socket, and turn it clockwise.
6Push the cover back on the taillight assembly. Repeat the process on the opposite light if needed, then close the rear hatch.
How to Remove a Grille on a 2003 Ford F150

You can remove the grille from the front of your 2003 Ford F150 at home using a few simple tools that can be purchased from any hardware store. You may have to remove a grille because of accident damage or you may wish to replace it with an after-market grille. In either case, its an easy job requiring only a few minutes of your time. Besides being visually pleasing, the grilles purpose is to protect the radiator.
Instructions
- 1
Pop up the hood and find the bolts that attach the upper radiator fan cover to the upper part of the grille. Use a socket and ratchet to remove these bolts.
2Remove the cover from the upper grille using your hands.
3Find the two plastic tabs attaching the drivers side of the grille to the fender in front. Push the tabs in toward the fender and pull on the grille from the front of the vehicle to dislocate it from the fender. Do the same thing on the passenger side of the grille.
Wednesday, February 19, 2014
How to Reset the Computer on a 2001 Monte Carlo

You can reset the computer on your 01 Chevy Monte Carlo right from your home garage, saving yourself time and money. The On-Board Diagnostics computer receives trouble codes from sensors positioned throughout the vehicle. These sensors keep track of all the functions of the vehicle and communicate with the computer. When the computer receives a trouble code, it communicates this to the driver in the form of a warning light on the dashboard. You can turn off these lights and reset after you have made repairs.
Instructions
- 1
Put the key into the ignition and turn it to the "on" position, but do not start the engine.
2Plug the computerized scan tool into the diagnostic port under the dash. You can buy a computerized scan tool from your local auto parts retailer. Select "PCM" on the menu and then choose "codes." Finally, select "clear all codes."
3Unplug the computerized scan tool from the port.
4Turn on the engine and observe the instrument panel to make sure all warning lights have shut off. The computer is now reset.
How to Identify a 10 Bolt 8 5 inch Posi Rear End

When it comes to getting power to the pavement, GMs 10-bolt, 8.5-inch rear end with Positraction is a hero. Like Superman in street clothes, however, it can be hard to identify this beefy unit among its weaker cousins, the 10-bolt, 8.2-inch with open differential.
GM built countless thousands of both types of 10-bolts from 1970 to 1994. This means you can typically find one suitable for your muscle car dirt-cheap at your local junkyard. Learn how to separate this strong man from the wimps.
Instructions
- 1
Wipe any grease and other debris off the gear casing with a rag to ensure you can see all of its features clearly.
2Count to make sure there are 10 bolts arranged equally around the outer perimeter of the gear casing, similar to the numbers on a clock.
3Locate two lugs, or ears, extending out from the bottom of the gear casing approximately in the 4 oclock and 8 oclock position. This will firmly identify the unit as having come with Positraction from the factory.
4Measure the gear casing horizontally, end to end, across its widest point. The measurement will be either 10 5/8 (10.625) inches or 11 inches, depending on the year it was made.
5Look for a bulge running vertically down the center of the gear casing. Most of the 10-inch units youre looking for will have this.
6Place your 1.25-inch socket over the pinion nut. If it fits, its the 10-bolt, 8.5-inch unit.
7Inspect the entire gear case and center section thoroughly to make sure there are no cracks or other damage that might compromise the units integrity.
Tuesday, February 18, 2014
How to Clamp an Exhaust Leak

The exhaust on a car or truck directs the gasses built up from the internal combustion process out to the back of the vehicle, that way the gasses dont build up inside of the vehicle and cause a carbon monoxide poisoning. If you develop an exhaust leak, then not only will it make an annoying noise, but if it could leak exhaust gasses into the cab which could be dangerous. To fix the issue, you can use a specialized clamp called an exhaust clamp to fix the issue.
Instructions
- 1
Put the vehicle on jack stands with the jack. Start the engine and listen to locate the exact spot of the exhaust leak, then turn off the engine.
2Crawl under the car and go to the exhaust leak. Wrap the clamp around the leak, which should not only be a hole, but should also have carbon buildup around the hole, indicating where the leak is.
3Tighten the clamp down over the exhaust using the flathead screwdriver, making sure that its secure all the way around. Lower the vehicle off the jack stands with the jack.
How to Install a Jack in a Ford Focus
The Ford Focus, which was first produced in 1999, is a compact car available as a hatchback, sedan or wagon. There are many instances when raising your Focus off the ground with a jack may be necessary, such as to change a flat tire, replace brake pads or change the motor oil. Before lifting the vehicle, it is important to understand how to properly use the jack and where to place it as incorrectly using a jack could result in serious injury or death.
Instructions
- 1
Move the vehicle to a level, paved surface as raising the vehicle on an incline could cause the vehicles wheels to roll and fall off of the jack.
2Shift the vehicle into "Park" and engage the parking brake. If you have an automatic transmission, shift the vehicle into "Reverse" and engage the parking brake.
3Place wheel chocks behind or in front of the two wheels on the opposite side of the end of the vehicle that you will be raising. The wheel chocks will prevent the wheels from moving while the vehicle is in the air.
4Locate the jack points underneath the Focus on both sides of the vehicle. The Focus has four jack points, two located approximately 8 inches in front of the rear wheel wells and two located approximately 6 inches behind the rear wheel wells. The jack points can be easily identified as they are double seam-welded sections and often have notches removed from the bottom.
5Place the floor jack below the sub-frame and raise it to lift thevehicle off of the ground. The jack included with the Focus must be turned clockwise with a special tool that resembles a thick, straightened wire hanger. This tool will be located in the trunk, along with the jack and spare tire. To use the tool, insert the hooked end of the tool into the fitted hole on the side of the jack.
6Position a jack stand beneath the jack point closest to the jack then lower the vehicle onto the jack stand by turning the jack tool counterclockwise. Repeat this process for the other side of the vehicle to raise the vehicle off the ground prior to repair or maintenance.
Monday, February 17, 2014
How to Test an Oil Pressure Sensor

The oil pressure sensor, often erred to as the oil pressure sender, is a unit responsible for telling a vehicles computer the oil pressure. It controls the gauge on a vehicle, which lights up as a warning indicator. This signals that the automobiles engine is receiving too little oil pressure or the sending unit is faulty. Low oil pressure could mean that not enough oil is present and can be easily fixed with additional oil. It might also indicate that the engine is burning oil or that an oil leak exists. If the sensor, or sending unit as some call it, is to blame, it can be easily tested.
Instructions
- 1
Insert the key into the ignition, and turn the key to the accessory setting. The engine should not be running.
2Look at the oil gauge on the dashboard. Unplug the wire that is connected to the sending unit, if the gauge is at zero. If the gauge goes up to three, it indicates that the sender is bad and needs to be replaced.
3Hold the end of the unplugged wire from the sending unit, and touch it to the negative part of the battery or to any other metal piece in the vehicle. If it shows zero on the oil gauge, it is a good sender and is not faulty.
How to Change the Oil on a 2001 Jeep Cherokee

Engine oil acts as a lubricant inside the engine and breaks down over time, theore your automobile requires a regular oil and filter change in order to extend the life of the vehicle. Learning to change your Cherokees oil and filter on a regular basis can help save you money on maintenance and expensive repairs later.
Instructions
- 1
Find the oil filter located at the oil pan of the engine. Place a container directly underneath filter.
2Turn the filter counterclockwise, using an oil-filter wrench, and remove from the engine. Allow the oil to drain completely from the engine.
3Apply a small amount of oil to the rubber seal of the new filter. Attach the new filter to the engine turning it clockwise until tight. Only use your hand to tighten the new filter and not a wrench or other tool.
4Remove the oil pan drain plug, using a socket wrench and turning counterclockwise. Be prepared to grab the plug before it drops into the container below. Allow the oil to drain completely.
5Reattach the drain plug without overtightening and remove any excess oil from around the oil pan with a cloth or paper towel.
6Locate and remove the cap for engine oil at the top of the engine. Add the amount of oil and weight specific to your Cherokees engine, either 6 quarts of 10w30 or 5w30. This information is located in your automobiles manual as well as underneath the hood. Replace the cap to the engine.
7Run your engine for one minute and let it sit for a few minutes. Using the oil dipstick, double-check the engine oil level is between the two indicators. Dispose of the old oil properly at your local oil-recycling center.
Sunday, February 16, 2014
Is My Engine Ruined Because of Sugar in the Gas

Its a commonly heard anecdote that an easy way to exact expensive vengeance on an enemy is to put sugar in the gas tank of his car. Its assumed the sugar will liquefy in the gasoline, turning it into a gummy, unburnable mess that ultimately destroys the cars fuel system and engine. It turns out that this is an urban myth. Putting sugar in the gas tank may slightly affect the vehicles running, but it is unlikely to do lasting or major damage.
Sugars Reaction With Gasoline
In reality, sugar does not dissolve in gasoline the way it does in water. When poured into the fuel tank, sugar will sink to the bottom and remain solid. If it is picked up by the fuel pump, it is caught by the cars fuel filter, which is designed to keep particulates from reaching the fuel injectors or carburetor where they can do damage.
Damage From Sugared Gasoline
Usually, the worst thing a handful of sugar in a gas tank will do is clog the fuel filter -- a time-consuming repair on some vehicles, but hardly an expensive or incapacitating one. If enough sugar is poured in, the tank itself may need to be removed and cleaned by a mechanic. The worst effect of a sugared gas tank it that it can cause the car to stall and be difficult to restart until the sugar is cleaned out.
Mythbusters
The television show "Mythbusters" put this theory to the test in 2004 by pouring sugar into a cars fuel tank and letting it run. The shows testers reported that the car was not damaged, and in fact ran even better after the tank was sugared! This does not mean that sugar can be considered a performance additive, of course.
Other Fuel Tank Pollutants
Other solid contaminants, like sand, react similarly in gasoline. Sand is less likely to get into the fuel filter because it is heavier than sugar and sinks to the bottom of the tank. A gas tank with sand in it will need to be removed and cleaned, but further damage is unlikely.
How to Adjust a Chrysler Headlamp

If you are relying on your high-beams more often than usual or have motorists flashing their lights at you even though you do not have your high-beams on, you may need to adjust the headlamps on your Chrysler. Your Chryslers headlamps provide you the light you need to see safely during nighttime driving. If your headlamps are incorrectly adjusted, the pattern they project can be inadequate and can also blind oncoming drivers. Periodically verifying and adjusting the aim of your Chryslers headlamps will give the the ideal nighttime visibility.
Instructions
- 1
Find a flat surface that is adjacent to a large wall. You will need a level surface that extends at least 30-feet from the wall. Pull your vehicle close the the wall as straight as possible.
2Mark the center line of your Chrysler on the wall using the masking tape. Coolbulbs.com recommends using a yardstick placed on the hood ornament and extended to the wall to get a precise mark. Measure the center of one headlight from the ground and from the center of one headlight to the center of the vehicle. Using more tape, transfer these measurements to the wall to mark the horizontal and vertical center lines of each headlamp beam.
3Measure 25-feet away from the wall and park the Chrysler there. Be sure to keep the vehicle perpendicular to the wall, if the vehicle is crooked it will skew the adjustments.
4The adjustment screws on Chryslers are located on top of the headlight assembly. Locate these screws and determine which screws control the vertical headlamp movement and which adjust the horizontal aim. You will most likely only need to adjust the vertical alignment of your Chryslers headlamps. Several manufacturers do not recommend adjusting the horizontal headlamp aim.
5Adjust the headlamp beams until they are two inches below the horizontal lines and two inches to the right of the vertical lines by turning the adjustment screws. Adjust each plane separately for the greatest accuracy. In this position your Chrysler headlamps will project the most efficient beam pattern without blinding other drivers.
Saturday, February 15, 2014
How to Clear the Codes in a Mazda MPV

You can clear the trouble codes on your Mazda MPV right from your home garage, saving yourself a trip to the mechanic or dealership. Mazda MPVs manufactured between 1989 and 1995 come equipped with an On-Board Diagnostics I computer (OBD I) and those manufactured from 1996 to the present have an OBD II computer. In either case, the procedure is the same, you just need a different tool to do the job. You must obtain a small, computerized OBD I or OBD II scanner. Clear the trouble codes after the vehicle has been serviced or repaired. Clearing the computer codes shuts off the warning and service lights on the instrument panel.
Instructions
- 1
Find the data link connector (DLC) port underneath the steering column. Its positioned a bit to the left of the steering column in some later model MPVs.
2Plug the OBD I or II scanner into the DLC.
3Put the key into the ignition and turn it two clicks forward to the "ACC" position. Follow the instructions on the scanner. Most scanners have an "Erase" or "Delete" command. Select this command and wait for the scanner to indicate that it has completed the task.
4Unplug the scanner and turn on the engine. Check to make sure the warning and service lights are not illuminated on the instrument panel.
How Do I Install Fuel Injection on a 350 Chevy
A 350 Chevy can be any engine in a Chevrolet vehicle with a displacement of 350 cubic inches. The last version of this engine was the Vortec 5700, which appeared in full-size Chevrolet trucks from 1996 to 2002. The 350 Chevy engine used central sequential fuel injection, which fires the fuel injectors in a specific order. The installation procedure for the fuel injectors is the same for all trucks with a 350 Chevy engine made after 1998.
Instructions
- 1
Turn the ignition off and remove the cable from the negative battery terminal with a socket wrench. Open the filler cap on the fuel tank to release the fuel tank pressure.
2Wrap a shop towel around the pressure fitting on the fuel rail and connect a fuel pressure gauge to the pressure fitting. Place the free end of the bleed hose of the pressure gauge into a container suitable for gasoline. Open the valve on the pressure gauge to relieve the fuel system pressure and disconnect the fuel pressure gauge from the pressure fitting.
3Detach the electrical connectors from the fuel pipes on the engine. Disconnect the fuel send and return lines from the fuel pipes with a socket wrench and discard the O-rings for the fuel lines. Remove the upper intake manifold from the engine with a socket wrench. Release the lock tabs on the fuel meter and disconnect the fuel meter from the engine.
4Remove the retaining nuts on the lower hold-down plate for the fuel injectors with a socket wrench and disconnect the hold-down plate. Pull the nozzle of each fuel injector down as you push a small pry tool between the electrical terminals of the fuel injector. Pry the injector out of its socket on the fuel meter and discard the O-ring on the fuel injector.
5Lubricate the O-rings for the fuel injectors with engine oil and mount the new O-rings to the new fuel injector. Install the new fuel injector to its socket on the fuel meter. Attach the lower hold-down plate and tighten its retaining nuts to 27 inch-pounds with a torque wrench.
6Connect the fuel meter to the intake manifold and tighten the retaining bolts to 88 inch-pounds. Attach the lock tabs for the fuel meter bracket to secure the fuel meter in place. Connect new electrical connectors for the fuel injectors. Mount new O-rings on the fuel lines and attach the fuel lines to the fuel pipes on the engine. Tighten the retaining nuts for the fuel lines to 22 foot-pounds with a torque wrench.
7Turn the ignition on for two seconds, then turn it off for 10 seconds to pressurize the fuel system. Turn the ignition back on and correct any fuel leaks.
Friday, February 14, 2014
How Do I Check If a Fuel Injector Is Working Properly

Properly working fuel injectors allow a vehicles engine to run and perform at a high level. However, even a slight clogging of an injector is enough to cause driveability issues with your vehicle. Its beneficial to be able to determine if a fuel injector is working properly.
Symptoms
There are several symptoms an automobile can display that will help you determine if your fuel injector is working properly, such as power loss to the vehicle. A car that hesitates when you attempt to take off from a dead stop is also a classic sign of fuel injector problems.
Testing
Another way to check and see if your fuel injectors are working properly is by running a flow test on them. The standard rate at which fuel should flow from the injectors can be compared with the injectors current flow rate. A flow that is not up to par indicates that your injectors have problems that need addressing.
Mileage
Yet another way to find clues about the condition of your injectors is by figuring out the mileage that has been traveled with them. Because experts suggest that fuel injectors should be cleaned before reaching 30,000 miles, distances over this benchmark indicate a need to at least have your fuel injectors checked.
The Disadvantages of Rack Pinion Steering

Rack and pinion steering is used in many cars. Essentially, the steering wheel turns a round gear -- the pinion -- which in turn moves a straight bar with gear teeth -- the rack -- from side-to-side to turn the wheels. It is a simple arrangement, but it does have some disadvantages.
Leakage
Because of the simplicity of the system, rack and pinion steering requires fewer parts to function properly. However, this places a greater strain on the individual parts, and the wear can cause leakage, requiring replacement of the rack assembly.
Less Durability
When installed in a four-wheel-drive vehicle, rack and pinion steering can cause problems when driving off-road. While this simple system provides responsive handling on paved roads, the greater force required to turn the wheels on drastically uneven ground can cause it to wear out much more quickly.
Vibration
Its simpler construction and reduced number of parts help rack and pinion systems provide more road feel than other steering mechanisms. However, this more intimate connection with the road can also transfer more noise and vibration to the driver and passengers.
Thursday, February 13, 2014
How to Install an Integra Fuel Injector
The Honda Integra was a compact sports car manufactured from 1985 to 2007. The last generation of the Integra includes the 2002 through 2007 model years, which Honda sold as the Acura RSX in the United States. A late-model Integra has a four-cylinder, 2.0-liter engine with multi-port fuel injection. Each fuel injector sends fuel to a cylinder in a specific sequence. The installation of the fuel injectors also requires you to relieve the pressure in the fuel system.
Instructions
- 1
Remove the cable from negative battery terminal with a socket wrench. Detach the kick panel under the dashboard and remove the fuel pump relay from the fuse box. Start the engine and allow it to stall to relieve the pressure in the fuel system. Open the fuel filler cap to relieve the pressure in the fuel tank. Replace the fuel pump relay, and fasten the kick panel. Close the fuel filler cap.
2Disconnect the cover on the intake manifold with a socket wrench, if your vehicle is so equipped. Detach the electrical connectors from the fuel injectors. Release the quick-connect fittings on the fuel line, and detach the fuel line from the fuel rail. Disconnect the fuel line and vacuum hose on the fuel pressure regulator.
3Remove the mounting nuts for the fuel rail with a socket wrench, and detach the fuel rail from the intake manifold. Release the retaining clip for the fuel injector. Pull the fuel injector up as you rock it from side to side to remove it from the injector bore. Discard the O-rings on the fuel injector.
4Coat the new O-rings with a thin layer of gasoline, and mount them to the new fuel injectors. Install the fuel injectors to the fuel rail, and attach the retaining clips. Mount the fuel rail to the intake manifold, so the injectors fit into the injector bases. Fasten the mounting nuts for the fuel rail, and tighten them to 16 foot-pounds with a torque wrench.
5Attach the fuel line to the fuel rail, and connect the quick-connect fittings. Install the fuel line and vacuum hose to the fuel pressure regulator. Attach the electrical connectors to the fuel injectors. Replace the cover for the intake manifold with a socket wrench, if your vehicle is so equipped.
6Connect the cable to the negative battery terminal with a socket wrench. Start the engine and allow it to idle for two minutes. Turn the engine off and correct any fuel leaks.
The Exhaust Is Leaking at the Motor for My 2001 GMC Sierra 2500 6 0L
Leaking exhaust at the engine on the 6.0-Liter GMC engine means the exhaust manifold gasket is faulty and there no longer is a good seal between the exhaust manifold and the cylinder head. To fix this leak, it is necessary to remove the exhaust manifold and replace the gasket. The exhaust manifold is secured to the cylinder head with six bolts.
Instructions
Removal
- 1
Lift the vehicle hood. Ensure the exhaust leak is coming from the mating surface between the cylinder head and the exhaust manifold, not the EGR valve or where the manifold meets the down pipe. Mark each spark plug wire with the paint marker to identify which wire belongs on what spark plug.
2Turn each spark plug boot about a half turn and pull it straight off the spark plug. Do not remove any plug wires from their respective coils.
3Remove each exhaust manifold mounting bolt with the proper size socket and ratchet. Gently pull the manifold away from the cylinder head a bit and remove the faulty gasket from the cylinder head.
Installation
- 4
Hold the new exhaust gasket to the exhaust manifold. Press the manifold and gasket to the cylinder head. Hand-tighten each exhaust manifold bolt.
5Tighten the exhaust manifold bolts to 10 foot-pounds of torque with the proper size socket and torque wrench. First torque the inside bolts, then the two outside bolts. Once all of the bolts are torqued to 10 foot-pounds, repeat the same process to 15 foot-pounds of torque with the socket and torque wrench.
6Install each spark plug wire by pushing it onto the proper spark plug. Pay attention to the marks previously made so the firing order is not disturbed. Shut the vehicle hood. Check the exhaust manifold bolt torque after the engine is warmed and cooled twice to ensure they maintain 15 foot-pounds of torque.
Wednesday, February 12, 2014
How to Replace the Windshield on a Jeep Cj7

You can replace the windshield on your Jeep Cj7 easily at home using some basic tools. Jeeps are made to withstand a beating, but sometimes even their very sturdy windshields may get chips or cracks in them and require replacement. This job should only take about an hour of your time. Visit your local junkyard to see if you can find an intact windshield for sale. This will save you some money.
Instructions
- 1
Unbolt the windshield using a 3/8-inch socket wrench, and set it aside.
2Spray the replacement windshield with glass cleaner to make it easier to wrap the molding around it. Wrap replacement windshield molding around the windshield.
3Put a 15-foot 1/4-inch nylon rope into the seam in the molding and leave 12 inches hanging out on each end.
4Put the windshield on the frame from outside the Jeep, making sure the ends of the rope are hanging inside the Jeep. Push on the glass from outside the vehicle while a helper pulls on the rope from inside the Jeep, simultaneously working the molding over the frame from inside the vehicle. This will seat the windshield.
5Put the windshield frame back in place and tighten it with the 3/8-inch socket wrench.
How to Troubleshoot a 1969 Chevy Trucks Headlights

The 1969 Chevrolet truck has two headlights. Theore, each headlight will have two filaments built in; one for the high beam and one for low beam. Headlight failure was prevalent on some early vehicles. The dimmer switch on these vehicles mount on the floor and exposes the wiring and connections to an abundance of moisture and corrosion. Another issue was the actual headlight switch or the plug that connected to it would heat up and the connection would fail. Headlight failure is unacceptable, and all issues should be addressed and corrected to maintain safe driving.
Instructions
- 1
Put on safety glasses. Remove at least one headlight bulb, using a screwdriver to remove the hold-down ring around the headlight, and test it. Connect a jumper wire between one of the parallel prongs of the headlight and the positive terminal on a 12-volt battery. Connect a second jumper wire between the negative battery terminal or a grounded engine component and the single prong below the two parallel prongs. If the light is bad, replace it.
2Inspect the entire fuse box for any blown or discolored fuses. The fuse box on a 69 Chevy truck is located under the dash on the drivers side of the truck. The 69 Chevy truck uses a glass tube fuse.
3Inspect the ground wire, which bolts to the radiator support behind the headlight socket on most older vehicles, for a good connection. If the connection is burnt or discolored, unbolt it with a wrench and clean it with a wire brush. Most models have a small black wire that mounts to the chassis with a 5/16-inch self-tapping metal screw.
4Charge the Chevy trucks battery with a charger or by running the engine for 15 minutes. If you are charging the battery, the red terminal of the charger should be connected to the positive terminal, and the black terminal connects to the negative terminal of the battery.
5Pull the headlight switch to full-on position. If the switch is pulled out halfway, it lights the parking lights only. Click the dimmer switch several times; take notice as to whether the high-beam indicator lamp in the dash lights up. If the high-beam indicator lights up, test the dimmer switch.
6Roll back the carpet or floor mat around the dimmer switch, found on the truck floor. Locate and remove the connector plug. Use two jumper wires and join all three wires of the dimmer switch plug together. If the headlights come on, replace the dimmer switch. If lights do not come on, check the plug with a 12-volt test light for a hot wire. One wire in the plug should light the test light unless the headlight switch is bad. Be sure the test light is grounded to a metal ground.
7Remove the headlight switch. The main mechanism of the switch is behind the dashboard and the pull knob is on the outside of the dashboard. From under the dashboard, press the spring-loaded tab, located on the switch mechanism, and rotate the headlight switch to the left to activate the interior lights. The switch must be rotated to pull the knob and rod out of the switch mechanism. Unscrew the thin nut on the front side of the dashboard that holds the switch in the dash with a box-end wrench. Drop the switch below the dashboard and unplug it.
8Probe the headlight connector plug with a 12-volt DC test light until the hot wire is found. If no hot wire is found, check the plug that comes through the cowl near the fuse box on the cowl side of the cab. Check the plug and headlight switch for heat related failure, melted or discolored wires.
9Inspect the wiring harness plugs, on the firewall side of the cab, that go through the firewall, for burnt or discolored wires. These wires are located around the area where the steering shaft comes through the cowl.
10Trace the wiring harness from the headlight bulbs or headlamps back to the cowl, checking for cracked, frayed or burnt wires. If any damaged wires are found, replace or repair the wiring harness.
Tuesday, February 11, 2014
Can You Have a Drive Shaft Balanced

A driveshaft transfers the force created by the engine to the drive wheels. Driveshafts can become out of balance, which may cause a number of problems both in terms of mechanical soundness and driving comfort.
Symptoms
An unbalanced driveshaft will wobble while spinning. This wobble may create a vibration felt in the steering wheel while driving or may shake the entire vehicle. The driveshaft may wobble only at certain speeds and not be felt otherwise. An unbalanced driveshaft will also cause increased wear to related components that may require frequent replacement.
Causes
Driveshafts can become unbalanced for a variety of reasons. A vehicle wreck may bend the driveshaft. The driveshaft may also become unbalanced due to loss of balance weights, corrosion or other damage. Bent or significantly damaged driveshafts may be incapable of being balanced and will require replacement.
Repair
Balancing driveshafts requires specialized equipment. A large device similar to a lathe spins the driveshaft and measures balance. Technicians weld small weights onto the driveshaft where needed to properly balance the driveshaft. Car owners should use only an experienced repair technician to tune driveshafts, as the process is complicated.
How to Tighten a Truck Engine Belt
A trucks engine belt operates accessories such as the water pump, air-conditioner compressor, power-steering pump and alternator. The belt moves these accessories from the crankshaft pulley. With the engine running, the crankshaft turns the belt around the pulleys so that each accessory can work. Over time, the belt will begin to wear and become loose. Once the belt becomes loose, tighten the belt to the proper tension. Most belt manufacturers recommend to have no more than a half an inch of slack in the belt.
Instructions
- 1
Open the hood and locate the belt. Follow the belt around the accessories that it operates. Locate the adjusting component that keeps the belt tight inside the pulleys. Most all truck belts are tightened by an adjustment bracket that is mounted to the alternator or the power-steering pump.
2Loosen the locking bolt from the front of the adjustment bracket with a ratchet and socket. Loosen the pivot bolts that mount the accessory to the engine block with the ratchet and socket.
3Tighten the belt by turning the adjustment bolt, located on the end of the adjustment bracket, counter-clockwise with the ratchet and socket. Once the belt is tight, push inward on the belt with your hand to check the belt tension. The belt should have no more than a half an inch of slack to be properly tensioned.
4Re-tighten the lock bolt in the middle of the adjustment bracket with the ratchet and socket. Re-tighten the pivot bolts that mount the accessory to the engine block with the ratchet and socket.
5Crank the truck engine for about five to 10 seconds. Turn the engine off and recheck the belt tension with your hand. Adjust the belt as needed to get a half an inch of slack in the belt.
Monday, February 10, 2014
Is R134 Compatible With R12

While modern air-conditioning systems use R-134 and other environmentally friendly rigerants, owners of vehicles manufactured before 1994 may have systems that use R-12 rigerant. Though the two rigerants are not compatible with one another, mechanics can adapt an older system for the new rigerant.
Differences
According to the automotive website Pro Car Care, R-12 rigerant is a chlorofluorocarbon (CFC) that erodes naturally occurring ozone. The substance consists of slightly larger molecules than R-134, and this difference makes a direct replacement of R-12 with the newer R-134 impractical. The automotive website AA 1 Car also points out that no one should mix R-12 with any other rigerant, as doing so can result in serious environmental damage while also presenting a significant safety hazard.
Retrofitting
Vehicle owners cannot directly replace R-12 with R-134 rigerant. However, mechanics can perform a retrofit that replaces air-conditioning components with new lubricants and seals designed to contain R-134.
Warning
While often considered a more environmentally friendly rigerant, R-134 is a greenhouse gas and can still cause environmental problems if allowed to vent directly into the atmosphere, according to the automotive website Garage-Pak. In addition, Pro Car Care notes that either rigerant will instantly freeze skin and other surfaces if allowed to vent.
Catalytic Converter Cleaning
Kids in the United States who reach driving age today probably dont remember acid rain and smog alerts. Those problems still exist, but their frequency and intensity have been mitigated, due in part to the catalytic converter, a clever little device developed by French engineer Eugene Houdry. He identified a growing problem in the smog heyday of the 1950s, but his invention wouldnt become standard equipment in most U.S. autos until the 1970s. Catalytic converters achieve their results efficiently with minimal power loss in todays cleaner-burning engines, but they can become clogged, or "poisoned," and that requires immediate attention.
What Is a Catalyst?
Catalytic converters are made up of a substrate, usually a ceramic honeycomb that maximizes exposed surface area, and a metal catalyst like platinum, rhodium or palladium that reacts with exhaust contaminants. Unburned hydrocarbons (HC), carbon monoxide (CO) and nitrogen oxide gas (NOx) are the big three baddies that the catalytic converter eliminates. Signs that your converter may be failing include sluggish throttle response, stalling at high temperature or a persistent sulfur smell coming from the tailpipe.
Poisons
The service life for most OEM converters exceeds 100,000 miles, so if your lower-mileage cars exhaust contains higher-than-accepted levels of HC and CO, the converter is fouled due to a problem elsewhere. There are contaminants that "poison" the reactive surface of the honeycomb. Lead is a converter killer, and while it was banned in gasoline in the 1970s, it is still found in some engine additives. Phosphorous and silicone are culprits also. Phosphorous is found in motor oil and can find its way to the converter if your engine is drawing oil into the combustion chamber. Silicone comes mainly from a leak that causes coolant to burn in the engine and exit to the exhaust systems. Both of these are engine problems that ruin the converter, not converter problems that ruin the engine.
Antidotes
A simple Internet search returns a host of products that promise to clean your catalytic converter. Some of these are temporary fixes designed to fool emissions-testing equipment. That gets you exactly nowhere in terms of fixing your vehicle. The consensus among mechanics is that you dont clean a catalytic converter--you replace it. Magical additives will cost you money, delay the inevitable and divert your attention from the real problem, which could be as severe as a failing head gasket that leaks coolant into the engine. Let that one go for a while, and youll be replacing your entire head at a cost of thousands. The bottom line is to be aware of the messages your car is sending. If your converter is indeed bad, either it has reached the end of its useful life or it is failing prematurely due to another engine problem. Dont get cute. It will cause you headaches down the road.
The Good News
One thing people never do is ask the mechanic to show them their old part when something has been replaced in their cars, which mechanics are required to do by law. This protects consumers against fraud. In the case of the catalytic converter, however, it can also net you some money. You own the failed converter, so youre entitled to take it with you and sell it for scrap. Its full of precious metals, so selling it to a scrap yard can help defray some of your repair costs. Also, the EPA mandates that warranties of up to 8 years and 80,000 miles be given on certain exhaust components. If your problem is the result of a defect, and your converter has failed earlier than it should, your repair cost could be covered under warranty.
Sunday, February 9, 2014
2001 Eclipse Mitsubishi Harmonic Balancer Removal
The Mitsubishi Eclipse is a two-door sedan that Mitsubishi has manufactured since 1990, and consists of four generations as of 2011. The 2001 model is a third generation Eclipse, which includes the 2000 through 2005 models. The harmonic balancer, or crankshaft damper, is a weight on the crankshaft pulley that reduces the vibrations caused by a rapidly-spinning crankshaft. In the case of the 2001 Eclipse, the crankshaft damper is an integral part of the crankshaft pulley. The procedure for removing the crankshaft damper from a 2001 Eclipse differs slightly, depending on the engine.
Instructions
- 1
Remove the cable from the negative battery terminal with a socket wrench. This ensures that you dont start the engine accidentally while removing the crankshaft balancer.
2Detach the accessory drive belts surrounding the crankshaft pulley to gain access to the pulley.
3Raise the vehicle with a floor jack and support it on jack stands. Disconnect the right front wheel with a lug wrench. Remove the fasteners for the inner splash shield on the right front fender with a socket wrench. Detach the splash shield from the right front fender.
4Disconnect the mounting bolts that attach the crankshaft pulley to the crankshaft sprocket with a socket wrench. Perform this step only if your engine has a displacement of 1.5 liters, 1.6 liters, 2.0 liters or 2.4 liters.
5Remove the retaining bolt in the center of the crankshaft pulley with a socket wrench. Perform this step only if your engine has a displacement of 1.5 liters, 1.8 liters, 3.0 liters or 3.5 liters.
6Attach a puller to the crankshaft pulley, and remove it from the crankshaft. The crankshaft balancer is part of the pulley.
How to Reset a BMW E60
The BMW E60 is more commonly known as the BMW 5 Series. The automobiles in this series come equipped with an on-board computer that tracks driving conditions and uses this information to determine when service is needed. The computer will illuminate an indicator on the instrumentation panel to alert the driver that maintenance is required. Once the car has been serviced, the computer must be reset so it can resume tracking conditions and alert the driver the next time maintenance is required.
Instructions
- 1
Turn the ignition on without actually starting the car.
2Press the odometer reset button and hold it in for about 5-10 seconds until the "Service" icon appears.
3Release the odometer button and press it again. This will display images of the various service icons. For example, an oil can indicates that oil service is required.
4Reset the service indicators by releasing and pressing the odometer button until the service icon that you want to reset appears. As soon as it appears, hold in the odometer button until the prompt "RESET?" displays. When the prompt appears, release the button briefly and then hold it in again for another 5-10 seconds until another icon appears. Continue resetting the other service indicators in this manner.
Saturday, February 8, 2014
How to Get a New Key for a 99 Ford Expedition
The 1999 Ford Expedition comes standard with a passive anti-theft system Ford calls "PATS," that incorporates a computer chip-equipped key to cut down on vehicle theft. Ford codes the chip inside the key with a digital signal unique to the particular Expedition. A transponder inside the dashboard reads and recognizes this signal as soon as you insert the key into the ignition. If the chipped key is not present, the Expeditions ignition system is disabled. In the event you lose or damage your key, youll need to have a Ford dealership replace it and program the replacement key to your Expedition.
Instructions
- 1
Go to your Ford dealers parts department with your 1999 Expeditions VIN number, registration or title and your state issued ID.
2Present your VIN number to the parts counterperson and request a new key for your 1999 Ford Expedition. The Parts Manager will need to verify you own the Expedition by matching your title or registration with your state issued ID (if the Parts Manager is not available, ask to see the Service Manager or Parts and Service Director). This is a safety measure incorporated by Ford Motor Company in 2007 to prevent thieves from requesting keys to your Ford vehicle.
3Go to the service department with your new key and request to have the key programmed to your Expedition. You will have to have your Expedition present, so if you dont have any keys for it, youll need to tow it to the dealership.
How to Tie a Nerf Bar Netting

Nerf bars are used on race cars, pickups, sports utility vehicles, motorcycles and ATVs. The Nerf bars are usually made from a light to medium weight material such as stainless steel. Nerf bar netting is attached to the bar in a certain way so there is no shifting or moving while you are on or off the road. After attaching the netting, it is imperative that you burn the ends of the nylon netting to make sure it does not fall apart.
Instructions
- 1
Assemble your Nerf bar kit according to the kits instructions. Each manufacturers kit may vary in size, shape and installation instructions.
2Position the Nerf bar netting so the pattern on the net lines up with the net tabs that are on the Nerf bars.
3Grab the end of the netting and push it through the top slot on the net tab. Push the netting through and out the bottom slot.
4Bring the netting up to the middle slot. Push it through the bottom of this slot and back up to the top slot.
5Repeat steps two through four for all the net line ends on your Nerf bar. Adjust the tightness of your netting according to your personal perence.
6Use a scissors to cut the excess ends of your netting. Make sure to leave 1 inch of netting on the ends.
7Hold an end of the netting with needle-nose pliers. Use a lighter to burn the end of the netting. This will prevent the netting from fraying.
8Repeat the previous step for all netting ends.
Friday, February 7, 2014
Uses for Cerium Oxide

Cerium oxide is an oxide of cerium, which is a rare earth metal, encountered on the periodic table. Cerium oxide is usually an off-white powder. It is also often called ceric oxide. The most common use of cerium oxide is as a glass and crystal abrasive, but several other industries also apply the compound in different ways.
Abrasive for Polishing Jewels
The most common use of cerium oxide is as an abrasive for fine polishing. It is frequently used to polish precious and semiprecious stones to a fine finish, and also as an abrasive agent in repairing scratches in these stones.
Glass Industry
Cerium oxide is also used as a fine abrasive in the polishing and grinding of precision lenses. Opticians often use it for this purpose. However, it is also useful in polishing all kinds of precision glasswork such as mirrors and machine lenses. Another use that the compound commonly sees is as a light filtration coating on lenses and as a UV protective coating on certain kinds of glass. This is due to its abilities as an excellent lector of ultraviolet light.
Ceramics
Cerium oxide is a key ingredient in the production of high quality ceramics of all kinds. It is used to build semiconductors, dental ceramics and even in high precision applications such as ceramic components for the aerospace industry and fuel cell manufacture. Cerium oxides main utility in the ceramics industry comes from the fact that it improves stability, wear-resistance and temperature-resistance when used in the manufacturing process of oxide ceramics.
Catalyst
Catalytic converters in cars often contain cerium oxide as a much cheaper alternative to platinum. This is because cerium is very effective at converting poisonous carbon monoxide gas into relatively harmless carbon dioxide. It also helps reduce the amount of nitric oxide that is emitted with a cars exhaust.
Blazer Fuel Pump Specs

Fuel pumps transfer pressurized fuel to various engine components. Some vehicles, such as older motorcycles, do not require fuel pumps. Fuel injected engines use a fuel pump that is mounted on the inside of the fuel tank. There are options available to replace the fuel pump on a 1994 Chevrolet Blazer.
Mr. Gasket
The Mr. Gasket company manufactures the micro electric fuel pump, model 12S. The pump is compatible with 1994 Chevy Blazer vehicles. The pump can be used alone or as a booster pump. The micro electric fuel pump has a two wire design and works on vehicles with a 12-volt negative ground system. The pump delivers 35 gallons of fuel per hour under four to seven pounds per square inch of pressure. Instructions are included for self-installation. The universal design fits most domestic, non-diesel four, six and eight-cylinder vehicles.
Airtex
The Airtex electric fuel pump, part number E3902, is compatible with 1994 Chevy Blazer vehicles. A strainer is required to validate the pump warranty. Airtex electric pumps feature brush and terminal assembly, which prolong the life of the fuel pump. The ball check valve ensures fuel is delivered under a consistent pressure level. The inlet is specially molded to reduce friction. A screen filters out fuel contaminants.
Delphi
Delphi electronic fuel pumps feature internal steel plated, all metal components. The pump has internal springs that enhance stability and reduce tube chafing. Delphi electronic pumps have a large volume reservoir that delivers continuous fuel during vehicle cornering and low-fuel situations. A two-strainer system greatly reduces fuel contaminants. Delphi guarantees a correct gas gauge reading with its pumps. Installation is facilitated with a color-coded wire harness.
Thursday, February 6, 2014
How to Install Clamp Style Risers
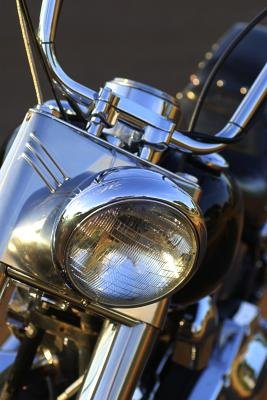
Risers are a way to raise or lower the height of the handlebars and hand controls on a motorcycle. Risers usually raise the riders connection to the bike by about 3 inches and may push the controls 2 inches closer to the saddle. This small change is usually enough to prevent back problems during a multi-state ride. But you should know before you begin that new risers may make your old control cables slightly too short. And, if that is the case, you must install the risers before you can measure your motorcycle for new cables.
Instructions
- 1
Drape towels over all sheet metal components on the front of the motorcycle, including the gas tank or air box and the front fender.
2Loosen the instrument cluster in the middle of the handlebars if your motorcycle has an instrument cluster there. Typically, the cluster attaches to the handlebars with four Torx or Allen bolts, so they should be loosened with Torx or Allen sockets and a socket wrench. Do not remove the cluster from the bars or any wires or cables.
3Instruct an assistant to sit in the saddle and hold the handlebars. Loosen the original upper handlebar clamps with a socket wrench and socket. The size of the socket and whether that measurement is metric (such as 22 mm) or standard (such as 7/8 inch) varies by brand of motorcycle.
4Instruct your assistant to hold the handlebars upright and remove the lower handlebar clamps with a socket wrench and socket.
5Install both new risers to the upper fork bracket in the same location as the original lower handlebar clamps with a socket of the correct size and a socket wrench. Instruct your assistant to hold the handlebars in the new lower riser clamps.
6Attach but do not fully tighten the upper riser clamps with the nuts, screws or other fasteners that came with your risers. Apply two drops of strong thread locker to each fastener. The handlebars will now be sandwiched between the lower and upper riser clamps.
7Instruct your assistant to dismount the motorcycle. Sit on the motorcycle and adjust the position of the handlebars before the final tightening.
8Tighten the upper riser clamps with a socket wrench and the correct socket. Retighten the instrument cluster screws or bolts.
9Turn the handlebars fully right and left to check for cable binding.
How to Replace the Injector RE531334 John Deere Tool

Fuel-injected engines are used to power medium and heavy John Deere equipment, such as tractors, loaders and combines. Periodic engine maintenance includes servicing the injectors for reliable fuel delivery. Dirty fuel filters or low-grade diesel fuel can clog fuel injector nozzles to the degree that replacement is necessary. Replacing a RE531334 injector requires mechanical aptitude and special tools you obtain through diesel engine service centers that carry the injectors. Injector tools are produced by a variety of manufacturers. Regardless of the manufacturer, obtain the tools that are compatible with the RE531334 injector.
Instructions
- 1
Park the equipment in a ventilated area and set the parking brake. Remove the engine cover.
2Remove the air cleaner assembly to provide access to the injector. Depending on the particular engine, it might be necessary to disconnect one or more exhaust recirculation hoses to remove the assembly.
3Detach the heat-signal wire from the outer end of the injector by depressing tabs on the connector. Move the connector and signal wire out of the way.
4Remove the secondary retainer ring at the base of the injector with a ring-clip tool. Save the retainer ring. Loosen the injector with a socket and ratchet until it spins in the injector port on manifold.
5Attach an injector puller onto the end of the injector. Fit the stems of the tool against the manifold at each side of the injector. Hold the tool in place with one hand as you turn the handle clockwise until the stems remain in place.
6Slide a length of 1/2-inch pipe onto the handle as a lever. Turn the handle clockwise with the pipe to remove the injector.
7Fit the tip of the new RE531334 injector nozzle into the rubber cup on an injector installation tool. Fit the large end of the injector into the port where the old injector was removed.
8Slide the circular driver on the installation tool up the rod to the base of the handle. Hold the handle with one hand as you slide the driver down the stem several times with moderate force to seat the injector in the port. Remove the tool from the tip of the injector.
9Tighten the injector with the socket and ratchet. If the injector spins and doesnt tighten, it is not fully seated against the upper rim of the threads in the port. Reattach the installation tool and seat the injector. Tighten it with the socket and ratchet.
10Fit the saved secondary retainer ring at the base of the injector with the ring-clip tool. Connect the heat-signal wire to the injector. Reattach the air cleaner assembly and reconnect any hoses, as necessary. Fit the engine cover into place.
Wednesday, February 5, 2014
How to Remove the Sway Bar End Link on a Chevy Colorado
The sway bar on a Chevy Colorado pickup truck connects the front left and front right suspension together. When the vehicle is turning, the sway bar minimizes side-to-side lean as well as keeps the vehicle more stable. This sway bar connects to the lower control arm on each side via a sway bar end link. These links can wear down over time; and when they do, the side-to-side lean can become almost unbearable. Before you can replace the end links, you must first remove them from the truck.
Instructions
- 1
Park the Colorado on a level, paved surface and step on the parking brake pedal to set the parking brake. Lift the front of the truck with a jack and put jack stands below the frame. Lower the truck so that it is supported on the stands.
2Remove the lug nuts on the front wheels with a tire iron then pull them off the truck. Locate the sway bar end links, which go up and down parallel to the front shock absorber and connect the lower control arm to the sway bar.
3Unbolt the upper sway bar end link from the sway bar with an open-end wrench. Repeat this for the bottom link in the sway bar. Do the same on the other side of the vehicle, then pull the links away from the sway bar and the lower control arm.
How Soon After Rebuilding a Transmission Should I Change the Filter


Same as New
A transmission rebuilt by a competent mechanic should be as clean and serviceable as a new unit. Check the service interval recommendation for your vehicle, and follow it. Depending on the make and model of the vehicle, the recommended service interval may range from 25,000 to 100,000 miles; some cars may never require this service.
Change at 5K
Transmission rebuilds can become expensive; replacing your transmission will cost even more. For peace of mind, if for no other reason, change the transmission oil and filter in a rebuilt transmission after 5,000 miles. Some shops require a 5K oil and filter change as a condition of their warranty and will include this work at no additional charge.
Bottom Line
Change a rebuilt transmissions oil and filter at 5,000 miles---especially if not doing so will void the warranty. After that point, rely on the manufacturers recommendation for maintenance intervals.
Tuesday, February 4, 2014
How do I Align a 1997 Toyota Camry Vehicle
A typical front end alignment consists of adjusting caster -- forward or rearward tilt of the steering axis; camber -- inward or outward tilt of the top of the tire; and toe -- inward or outward tilt of the front of the tire -- to prevent excessive tire wear, improve handling, and straighten an off center steering wheel. Many manufacturers, like Toyota, do not provide adjustment for caster and camber from the factory. In the 1997 Toyota Camry the toe angle is adjustable on all four wheels and, while caster is not adjustable, camber can be adjusted using aftermarket bolts in the struts.
Instructions
- 1
Apply the parking brake and start the engine. Center the steering wheel and turn off the engine. Apply the brakes and lock them in place using the brake pedal depressor. Clamp the alignment machines targets securely to all four wheels and level the targets using the built in bubble level. Compensate for wheel run-out according to the machines procedure.
2Determine which wheels need a camber adjustment by comparing the initial readings of the alignment machine with the factory specifications. Remove the upper strut-to-steering knuckle mounting bolt using a wrench, socket, and ratchet.Install the adjustable aftermarket bolt in upper bolt hole and tighten it securely.
3Loosen both strut-to-spindle mounting bolts on the right rear strut. Rotate the upper, adjustable aftermarket, bolt to adjust rear camber until it is within specifications. Rear camber in the 1997 Camry should be -.75 degrees +/- .75 degrees. Camber should also be equal on both sides. Tighten the strut bolts to 145 psi using a torque wrench. Adjust the left rear camber in the same manner.
4Adjust the right rear toe angle by loosening the jam nuts on the right rear toe arm using a 21 mm wrench and twisting the adjuster nut until the toe is within manufacturers specification. The rear toe on the 1997 Camry should be .10 degrees +/- .05 degrees. Tighten the jam nuts securely. Adjust the left rear toe in the same manner.
5Adjust the front camber to -.8 degrees +/- .75 degrees in the same manner as the rear camber and tighten the strut bolts to 156 foot-pounds using a torque wrench. Loosen the jam nut on the right front tie-rod and rotate the tie rod to adjust toe to 0 degrees +/- .05 degrees and tighten the jam nut securely.
6Start the engine and center the steering wheel. Verify that the front toe angle is within specifications. Readjust front toe, if necessary. Remove the targets from the wheels and test drive the car to verify it drives properly.
How to Neutralize Battery Acid With Baking Soda

Working with a battery can be messy and dangerous due to the acid and corrosion that is typically present in a battery. Spilling the acid on your clothes will likely ruin them, while getting it in your eyes is extremely dangerous. Baking soda can effectively neutralize the corrosive nature of battery acid and washing your clothes in a solution of baking soda and water can also minimize the damage from a spill.
Instructions
- 1
Disconnect the battery from the device it has been in and/or from any terminals.
2Combine three parts baking soda and one part water to form a paste.
3Use the paste and one damp cloth to scrub the battery terminals and clean any corrosion from the inside of the battery connectors.
4Use the second damp cloth to wipe off any excess paste that remains on the battery.
5Allow the battery to air dry before re-inserting it into a device and/or connecting it to terminals.