Friday, December 27, 2013
How to Install a V Rod Air Filter
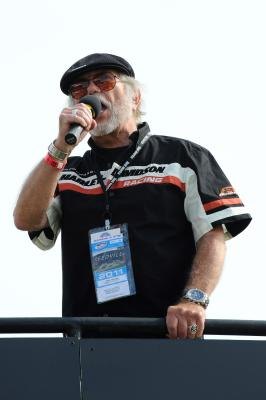
Most Harley-Davidsons are powered by technologically primitive engines. Critics call them "de-engineered." The basic nature of the machines is part of their charm for an aging customer base. The V-Rod is Harleys modern motorcycle intended to appeal to both younger and traditional customers. The V-Rod was designed to look more traditional than it actually is, so Harley designed its "air box" to look like a gas tank. Older bikers often assume it is the gas tank. The air filter is inside this air box; once you understand what to open and how, changing this filter should take less than five minutes.
Instructions
- 1
Stand on the right side of the motorcycle and lift the right side of the seat. After a gentle tug, the seat will pivot up.
2Turn the retaining ring on the back of the outer air box cover 1/4 turn counterclockwise. The outer air box cover is styled to look like a conventional Harley gas tank. Lift the outer air box cover off the bike and set it aside.
3Disconnect the intake air temperature sensor at the rear of the inner air box cover by pulling the two halves of the connector apart. The sensor is clearly visible on recent V-Rods. Early V-Rods located this sensor on the engine, and if it is there, you do not need to disconnect it.
4Unfasten the eight clips that secure the top of the inner air box, using a flathead screwdriver. There is one clip in front of the box, one in back and three on each side of the inner air box.
5Unscrew the wing nut that holds the air filter in place. Remove the old filter by pulling up, and either reinstall the original after servicing or install a new filter. Drop the new or serviced filter back on the mounting stud and retighten the wing nut.
6Resecure the inner air box top to the mounting clips. Reconnect the air temperature sensor.
7Push the outer air box cover back in place. Push down the seat.
Thursday, December 26, 2013
DIY Oxygen Sensors on 1997 BMW Z3 Roadster
The Z3 made its first appearance in the U.S. in the 1996 model year with only a 1.9-liter four-cylinder engine. In 1997, BMW added in an optional 189-horsepower, 2.8-liter in-line six-cylinder engine to complement its standard 138-horsepower, 1.9-liter engine. The base-level four-cylinder on the 1997 Z3 uses two oxygen sensors, one before the catalytic converter and one after it. These oxygen sensors are responsible for keeping close tabs on the air-to-fuel ratio and harmful exhaust emissions, by testing the oxygen density in the exhaust system. Replacing the 1997 Z3s oxygen sensors is a straightforward task that most DIYU mechanics can complete with relative ease.
Instructions
Removal
- 1
Lift the front of the Z3 with a floor jack and slide jack stands under its frame rails. Lower the vehicle onto the jack stands.
2Crawl under the center of the vehicle and find the catalytic converter the muffler-like object just after the exhaust goes from two pipes to one pipe. The upstream oxygen sensor is screwed into the exhaust pipe just before the catalytic converter and the downstream sensor if screwed into the pipe just after the catalytic converter.
3Trace the failed oxygen sensors wiring upward until you find where it connects to the vehicles main wiring . Unplug the sensors wiring harness from the Z3s wiring harness. Pull the oxygen sensors wiring from the routing clips. Remove the failed sensor, using a ratchet and oxygen sensor socket. Repeat this step for the other sensor, if needed.
Installation
- 4
Apply a thin coat of an anti-seize compound to the new oxygen sensors threads. Use caution not to get any anti-seize on the tip of the sensor. Thread the new sensor into its respective hole in the exhaust pipe by hand.
5Tighten the oxygen sensor to 37 foot-pounds using the torque wrench and oxygen sensor socket.
6Route the oxygen sensors wiring upward toward the Z3s wiring harness, pressing the wiring into its routing clips as you go. Plug the oxygen sensors wiring harness into the Z3s harness.
7Repeat steps 1 through 3 to install the other oxygen sensor, if you removed it.
8Raise the vehicle off of the jack stands and remove the jack stands. Lower the vehicle to the ground.
Wednesday, December 25, 2013
How a Car Relay Works
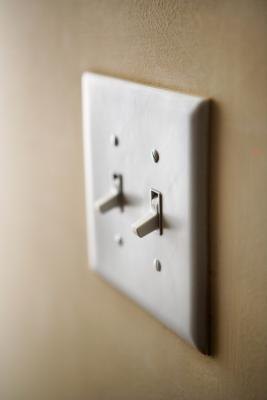
Automotive wiring systems arent the simplest thing on the planet, but they arent the most complicated either. When you break the electrical system down into its component parts, you find that it consists mainly of simple circuits and equally simple switching gear. Relays are one type of electrical switch that manufacturers install to minimize production costs and maximize safety.
Electrical Basics
A relay is essentially a switch that you dont have to flip. Electricity is the movement of electrons, and moving things, by definition, have an origin and a destination. Think of electrons like cars on a racetrack that move around it at the speed of light; if you suddenly remove a section of track, then the race stops because all the drivers fall into the hole and get smashed into atoms. Electrical circuits work the same way. As long as the circuit or track stays intact, the electrons can continue their race.
Relay Basics
A relay is basically just a switch that you dont have to flip, and a switch is a means of removing a section of the circuit. When you flip a light switch to the On position, its internal connections close the circuit and allow electricity to flow through it. Now, imagine the switch lever is made of metal instead of plastic and youre standing next to it with a magnet. Using the magnet, you can flip the switch on and off without touching it. But moving the magnet isnt practical, so what you need is a magnet that you can leave in place but turn on and off.
Induction Coils and Electromagnets
Anything moving through a gravitational field produces a magnetic wake, and it doesnt matter if that moving thing is an electron or a Boeing 747. Most metals have small regions of magnetism inside called magnetic domains, but those domains point in all different directions so they cancel each other out. Wrap a coil of wire around a metal rod and send electrons flowing through the wire and you create a magnetic "tornado" around the rod. This vortex gets all of the magnetic domains temporarily pointing in the same direction, turning the metal core into an electromagnet.
Relay Construction and Function
Youve undoubtedly connected the dots by now: a metal armature arm inside the relay is spring-loaded to stay open, but when the electromagnet under it activates, the armature comes down and closes the circuit. The idea behind using a relay is that it takes far less current to energize the electromagnet than the circuit would normally use. That means that, although your starter may require 50 amps of current to spin the motor, your ignition key mechanism only needs to pass 0.50 amps to energize the magnet. This allows manufacturers to use thinner-gauge wire and lighter-duty switching gear without risk of frying the wire or the switch.
Tuesday, December 24, 2013
Chevy Fuel Pump Problems

On October 22, 2009, General Motors and the National Highway Traffic Safety Administration announced a recall of 69,139 vehicles including 2006-2007 model year Chevy Cobalts for fuel pump problems. Registered vehicle owners should have been notified by mail and instructed where to bring the vehicle for free repair.
Defect
General Motors initiated the recall for certain 2006-2007 Chevy Cobalts because the plastic supply or return port on the modular reservoir assembly could crack. If a crack happens, fuel will leak from the area. If the crack becomes large enough, fuel may be observed dripping onto the ground.
Consequences
Per the NHTSA, vehicle performance could be affected in these vehicles. More importantly, a gas leak in the presence of an ignition source could potentially result in a fire.
Remedy
Registered vehicle owners were expected to be notified by mail of the recall on or around February 4, 2010 with instruction on which authorized dealers will replace the fuel pump modules for free, according to General Motors and the NHTSA. Vehicle owners who did not receive notice or are concerned about the recall may contact General Motors or the NHTSA to determine whether their vehicles might have been affected.
Monday, December 23, 2013
How to Disable a Car Alarm on a 1992 Pontiac Grand Prix

Some car alarms are more sensitive than others. If somebody is walking by the car and nudges it, the car could go into frenzy. Car alarms are also annoying when trying to make repairs to the cars. If you want to disable the alarm on your Pontiac Grand Prix, you can easily turn it off by accessing the alarm transmitter. This is located under the steering wheel. By engaging the valet switch, the alarm automatically disables.
Instructions
- 1
Open the Grand Prix and put your key in the ignition. Turn the ignition until you have turned on the cars electrical system, but not the engine.
2Pry off the dashboard panels around your ignition cylinder with your fingers or a flat-head screwdriver.
3Locate the alarm transmitter in the ignition cylinder. This is a small black box.
4Locate the "Valet Switch" and turn it off. This switch will be labeled. When you turn it "Off" the LED light on the transmitter will go off.
5Replace the dashboard panels around the ignition cylinder.
Sunday, December 22, 2013
How to Open a 2002 Chevy Tahoe With No Keys If I Got Locked Out

Losing your car keys is an annoyance no one wants to deal with. However, losing your keys isnt as annoying as knowing exactly where your keys are: locked in your 2002 Chevy Tahoe with no means of obtaining them. When you lock your keys in a late-model car, its not a good idea to attempt to retrieve them the same way your parents did when you were a child. Sticking a wire hanger into the door frame of your newer-model car could damage your lock mechanism, which means adding the expense of having your vehicle worked on to your already annoying day.
Instructions
- 1
Call your local police or sheriffs department or a professional locksmith or towing company. All are equipped with the necessary tools to open your Tahoes doors without damaging your locks.
2Inform the representative on the phone of your vehicles location and ask to have someone sent out right away to retrieve your car keys for you.
3Provide the tow truck driver/locksmith/law enforcement officer with proof of your identity and ownership of the vehicle. You can do this by presenting your drivers license along with your title, registration or insurance card. If you generally keep your vehicle information in your glove compartment, explain your situation, and you will be permitted to retrieve your information once your doors are unlocked.
4Pay for any services rendered. Police and sheriffs officers dont charge for helping you break into your own car.
Saturday, December 21, 2013
Oldsmobile Cutlass Vehicle Emission Control Information

The emission controls on an Oldsmobile Cutlass are fully integrated with ignition and fuel system controls. All of these control systems work together to ensure the engine works efficiently with minimal production of harmful exhaust gases.
Crankcase Ventilation System
The crankcase ventilation system controls unburned fuel vapor that leaks from the pistons into the crankcase. Normally these vapors would leak into the atmosphere since they are under pressure. If left alone they contaminate the engine oil and allow sludge to build up in the crankcase. The crankcase ventilation system recycles these gases back into the air intake so they can be re-burned in the pistons. The Positive Crankcase Valve (PCV) controls how much of the gas is recycled at any given time.
Evaporative Emission Control System
The Evaporative Emission Control System (EEC) is a carbon canister that reduces emissions of fuel vapors from the fuel system. It stores fuel vapors and vents them through a filter containing activated charcoal. The charcoal absorbs vapors while the engine is not running. The charcoal releases the vapors into the air intake manifold when the engine is running. A solenoid closes the canister to air when the engine is turned off so that fuel vapor is not lost to the atmosphere.
Exhaust Gas Recirculation System
The Exhaust Gas Recirculation System, or EGR, reduces oxides of nitrogen emissions. Nitrogen oxides are often written as "NOx" and they are harmful to human and animal health. The EGR is a valve which, under certain conditions, allows some exhaust gas to recirculate into the intake manifold. The exhaust gas then cools combustion temperature and controls detonation of the fuel/air mixture. The EGR valve is mounted on the intake manifold and uses manifold vacuum to open up and vent some exhaust gas into the intake manifold. It is activated only when the engine reaches normal operating temperature. Too much exhaust flow into the intake manifold can cause stalling after a cold start or during deceleration.
Thermostatic Air Cleaner
The Thermostatic Air Cleaner (THERMAC) warms air entering the carburetor when the engine is cool and maintains a controlled air temperature into the carburetor. This reduces the amount of time the choke needs to be on and results in better fuel economy and lower harmful emissions.
Air Management System
The Air Management System injects oxygen into the exhaust ports, exhaust manifolds and catalytic converter to burn off any fuel vapor left in the exhaust gas. The system shuts off only during deceleration or rapid acceleration to prevent backfiring. The system reduces the levels of hydrocarbon and carbon-oxygen combinations in exhaust gases.
When to Bleed a Gas Hose

Any time a high-pressure fuel system is opened for service, air is introduced into the fuel hose. Bleeding, which requires running fluid through the hose, will eliminate air from the system and help reduce vehicle stalling and intermittent operation problems. The fuel system must be bled to prevent these hazardous operating conditions.
Fuel Filter Work
The fuel hose must be bled when the fuel filter is replaced. Typically, fuel filters are ahead, behind or both ahead and behind the fuel pump. Some fuel filters are made of clear plastic or glass to make it possible to visibly locate the presence of air.
Fuel Pump Work
Modern fuel-injection systems may have two or more fuel pumps. Each of these is designed to work at high pressure. Any time a fuel pump is replaced, it needs to run for a few moments to pull enough fuel through to draw air bubbles out of the fuel line.
Fuel Hose Work
Deteriorated or damaged fuel hoses or lines may themselves draw in under the vacuum of a fuel pump. When a fuel hose or line is replaced, the fuel system should be bled under pressure to draw out any air.
Friday, December 20, 2013
California Salvage Vehicle Regulations

For the experienced mechanic or auto restoration enthusiast, bargains and challenges alike can be found at the junkyard in the form of salvage vehicles. The state of California has specific regulations governing the sale and registration of these vehicles.
Definition
The state of California defines a salvage vehicle as one that has sustained damage from an accident or other cause (fire, smoke or flood) to such an extent that an insurance company has decided making repairs is not economical and will not fix the car.
Salvage classification
If an insurance company settles with the owner of a vehicle deemed a total loss, the company must obtain a salvage certificate for the automobile. If an owner retains possession of the vehicle as part of a settlement, the insurance company is required to notify the state Department of Motor Vehicles, and the owner is required to obtain his own certificate of salvage within 10 days of the settlement.
Fee refund
Once a car is classified as a total loss, an owner who does not intend to repair the vehicle but retains possession is eligible for a refund of a portion of the vehicle registration fees previously paid to the state. Fees returned are one-twelfth the annual fee multiplied by the number of full months remaining until the cars current registration is due to expire. Drivers who wrecked their vehicles and were cited for driving under the influence are not eligible to receive these fees back.
Disclosure
State law requires owners of salvage vehicles to notify the purchaser, at or before the time of sale, of the vehicles total loss salvage status. If a seller does not make this disclosure, she can be sued.
Re-registration
If a vehicle previously designated as "salvage" is privately repaired and becomes operational, an owner can apply to re-register a car as a "revived salvage vehicle." The automobile is subject to a safety inspection by a California Highway Patrol officer, an emissions test performed at a regulated inspection station, and tests to ensure the cars brakes and lights are fully functional. Those wishing to re-register a previously salvaged vehicle must provide proof of ownership. The state of California will not consider re-registering cars using out-of-state salvage certificates.
Thursday, December 19, 2013
How to Change the Catalytic Converter on a 2004 Chevy TrailBlazer
The 2004 Chevy Trailblazer base model came with a 4.2-liter inline six-cylinder engine and a four-speed automatic transmission. Your catalytic converter is located between the exhaust manifold and the muffler. A faulty catalytic converter can result in poor performance and higher emissions levels that will cause you to fail an emissions test. Replacing your catalytic converter is a straightforward task, but the transmission mount has to be removed because of the length of the catalytic converter assembly.
Instructions
Removal
- 1
Park the vehicle on a level surface and set the parking brake. Lift the front of the vehicle into the air with a floor jack and place jack stands under the front frame rails. Lower the vehicle until it rests securely on the jack stands. Allow the engine and exhaust to cool completely before continuing.
2Position yourself under the vehicle so that you can clearly view the catalytic converter and its connection to the exhaust manifold. Locate the front oxygen sensor that is positioned just after the first flange and disconnect the pigtail from the wiring harness. Follow the catalytic converter piping after the converter to find the rear oxygen sensor. Disconnect the rear oxygen sensor pigtail from the wiring harness.
3Place the oxygen sensor socket over the front oxygen sensor so that the pig tail extends through the slotted portion of the socket. Rotate the sensor counterclockwise with a ratchet to remove the sensor from the exhaust. Apply heat with a propane torch around the base of the sensor, if it is difficult to remove. Repeat for the rear oxygen sensor and label each one accordingly; they are not interchangeable and must be installed in the same position.
4Place one jack stand at the rear and one under the front of the converter assembly, and elevate them until they make contact with the converter assembly. Remove the nuts securing the converter assembly to the exhaust manifold with a ratchet and socket. Remove the nuts securing the converter assembly to the rear muffler pipe.
5Place a floor jack under the transmission and place a small block of wood on the jack arm. Raise the jack until the wood makes contact with the case of the transmission, but do not apply any upward force. Examine the transmission support that runs between the two frame rails to find the two center access holes. Remove the bolts securing the transmission mount to the transmission support with a socket and ratchet.
6Remove the bolts securing the transmission support to the frame rails. Lower the transmission support from the vehicle and set it aside. Remove the bolts securing the transmission mount to the base of the transmission. Remove the catalytic converter and transmission mount from under the vehicle.
7Pry the rubber hangers from the old catalytic converter assembly with a pry bar and set them aside. Set the transmission mount aside, with the rubber hangers attached.
Installation
- 8
Examine the rubber hangers for any damage or wear and replace as necessary. Install the transmission mount, with the rubber hanger bracket attached, to the transmission. Install the mounting bolts and tighten to 48 foot-pounds with a torque wrench.
9Set the catalytic converter assembly onto the jack stands so that the flanges at both ends meet up with the exhaust manifold and muffler assembly. Lift the catalytic converter assembly as necessary and install the rubber hangers at the transmission mount to the metal hangers on the converter assembly.
10Lift the transmission support into place between the frame rails and install the retaining bolts. Install the transmission mount to transmission support nuts through the access holes and tighten to 35 foot-pounds.
11Install a new gasket at the front and rear of the converter assembly. Slide the converter assembly rear flange over the studs for the muffler pipe. Install the rear mounting nuts hand tight. Install the front converter flange to the exhaust manifold and install the mounting nuts hand tight. Tighten the mounting nuts for both flanges one turn at a time until they are tightened to 33 foot-pounds.
12Remove the jack stands from under the converter assembly. Clean the oxygen sensor threads with a wire brush and apply copper anti-seize to the threads. Install the both oxygen sensors to the converter assembly until hand tight. Tighten both sensors to 30 foot-pounds with a torque wrench and oxygen sensor socket. Plug the oxygen sensor pigtails to their respective wire harness connectors.
13Lift the front of the vehicle off the jack stands and remove the jack stands from under the vehicle. Lower the vehicle to the ground and remove the floor jack.
Wednesday, December 18, 2013
How to Replace 7 3 Injectors
The 7.3-liter Ford Power Stroke engine is an eight-cylinder diesel engine with fuel injection. Its most common on larger Ford vehicles made from 1995 to 2002, such as 3/4-ton and full-ton pickup trucks. Each cylinder of this engine has a fuel injector that delivers fuel to the cylinder in a precise amount and timing sequence. The replacement of the fuel injector in a 7.3-liter engine requires you to disassemble the fuel rail assembly on top of the engine.
Instructions
- 1
Place an oil drain pan under each oil drain and open the drain plug with a socket wrench. Allow the oil to drain into the drain pan and replace the drain plug. This will prevent oil from entering the combustion chamber while you replace the fuel injectors.
2Remove the valve cover with a socket wrench, and detach the electrical connectors from the fuel injectors. Remove the drain plugs on the oil rail and fuel rail. Disconnect the retaining screw for the oil deflector and remove the oil deflector. Remove the retaining bolt for the fuel injector.
3Place the fulcrum of injector remover No. T94T-9000-AH1 below the hold-down plate of the fuel injector. Fasten the remover screw into the hole in the fuel injector plate, and tighten the screw to remove the fuel injector from the injector bore. Discard the copper washer.
4Clean the injector bore of any debris with rotunda injector sleeve brush 104-00934-A and a clean shop towel. Lubricate the new fuel injectors with clean engine oil and mount a new copper washer onto the injectors.
5Push the fuel injectors gently into the injector bore to seat the O-rings. Place the open end of injector replacer No. T94T-9000-AH2 between the hold-down plate and the fuel injector. Fasten the tool to the cylinder head with the retaining bolt from the tool kit. Tighten the bolt to completely seat the fuel injector and disconnect the tool from the cylinder head.
6Install the oil deflector and tighten the mounting bolt to 108 inch-lbs. with a torque wrench. Tighten the fuel rail drain plugs to 96 inch-lbs. and tighten the oil rail drain plug to 53 inch-lbs. Connect the wiring harness for the fuel injectors and install the valve cover.
Tuesday, December 17, 2013
How to Access Jeep Liberty Error Codes

You can access your Jeep Libertys error codes from your home, saving you time and money. Jeeps manufactured after 1996 come equipped with an On-Board Diagnostics II computer (OBD II) that retrieves and stores all trouble codes sent to it from sensors positioned throughout the Jeep. Jeeps manufactured 1996 or earlier come with an OBD I computer. When these sensors detect a malfunction in the vehicle, they send a code to the computer. The computer then illuminates warning or service lights on the instrument panel. You can retrieve these error codes using a small computerized device called an OBD I or II code scanner, which you can purchase at any auto parts retailer or online.
Instructions
- 1
Find the OBD port on the drivers side dash underneath the steering column. It is the same size and shape as the connector on the OBD code scanner.
2Plug the code scanner into this port. Turn the key into the ignition to the "ACC" position but dont start the engine.
3Wait while the code scanner powers on. Find and select "Read Codes" or a similar type of command. Wait while the code scanner interfaces with the computer. When it displays the codes, write them down on a piece of paper.
4Look up the meaning of the codes in the manual. Unplug the scanner and take the Jeep to be serviced or repaired using the information obtained from the codes.
Exhaust Manifold Torque Specs

The exhaust manifold is a large metal block bolted to the side of the engine, and it connects the exhaust pipe to the main engine block. To locate the exhaust manifold, trace your exhaust pipe to where the round pipe bolts to a two-bolt connection near the engine. The solid structure to which the pipe is bolted is the exhaust manifold. Installing a manifold requires careful torquing of the bolts.
Amount of Torque
Every vehicle has different levels of torque necessary to properly tighten its bolts. The standard is to use 20 to 30 foot-pounds of torque. Older engines often fall on the lighter side of the equation, so use 15 to 20 foot-pounds of torque if your engine is 15 years old or older. Some manifolds house different sensors and plugs, such as a check valve or exhaust plug. The different elements require less torque than the bolts on the manifold. Use between 10 and 17 foot-pounds of torque for those elements. The precise torque for your vehicle can be identified in the vehicle-specific repair manual, available from an auto parts retailer.
Torque Sequence
Clean off any used gasket material, and install a new gasket when you take the manifold off the vehicle. Torquing the bolts properly requires following a set pattern. The pattern helps the new gasket sit correctly against the engine blocking leaks. Hand-tighten all bolts initially. Torque the bolts in sequence to half the amount of torque necessary. Start with the middle bolts, and work your way toward the edges one bolt at a time. Repeat the process using the full torque necessary.
Additional Information
In most vehicles, the manifold is covered by a heat shroud, which is a simple piece of formed aluminum. The metal acts as a heat damper to prevent excessive heat from bouncing around in the engine. You must remove the heat shroud before working on the manifold. When installing the shroud, use 10 to 12 foot-pounds of torque. You also should inspect the length of the exhaust pipe for damage. When servicing the exhaust, you should disconnect each bolted connection, clean the surface of the connection and install new gaskets at each joint. You can unbolt each connection and separate the joint by several inches without removing the unit from the vehicle.
Monday, December 16, 2013
Purpose of Catalytic Converters
The catalytic converter is part of a vehicles exhaust system and serves to reduce the amount of toxic gases emitted into the atmosphere. These surprisingly simple components have served to dramatically reduce the amount of vehicle emissions produced over the past few decades. Today, they are installed on all factory-produced vehicles sold in the United States.
History
The Engelhard Corporation invented the first production-ready catalytic converter in 1973. A couple years later, the Environmental Protection Agency introduced more stringent regulations relating to vehicle emissions. Confronted with these new requirements, auto manufacturers quickly embraced the new earth-friendly product. The 1975 vehicle model year was the first time that the catalytic converter came pre-installed on new cars.
Effects
The first catalytic converters on the road were known as 2-way catalytic converters. Cars with such technology are capable of converting hazardous carbon monoxide to harmless carbon dioxide. They also break down toxic hydrocarbons into carbon dioxide and water. In 1981, 3-way catalytic converters became commonplace. Cars with this newer technology are also capable of reducing nitrogen oxides to regular nitrogen and oxygen.
Function
The catalytic converter converts toxic gases to harmless gases via a platinum-iridium catalyst. As the hydrocarbons and carbon monoxide pass through this catalyst, the gases are oxidized. This causes them to break down into less toxic elements. Nitrogen oxides require a separate process, known as reduction, to eliminate toxicity.
Considerations
The catalytic converter is typically situated below the front passenger seat, between the engine and the rear exhaust. In order to function properly, the combustion chamber must be fed the correct ratio of gasoline to oxygen. If too much oxygen or gasoline is introduced, excessive hydrocarbons and other toxic gases will be produced. These extra particles make it hard for the catalytic converter to keep up with the inefficiency of the engine. To eliminate such a scenario, most modern-day vehicles feature fuel injection and oxygen sensors to monitor the oxygen-to-gas ratio entering the combustion chamber.
Potential
Though catalytic converters have been integral in reducing vehicle emissions, there is still more that can be done. The biggest downside to catalytic converters is that they require a great deal of heat to function properly. This heat is generated by the engine, but it takes several minutes after you turn your car on before the catalytic converter becomes effective. Currently, engineers are tinkering with ways to speed up the heating process so that vehicle emissions are cleaned by the catalytic converter during these first minutes of vehicle operation.
Chevy S 10 Blazer Alignment Specifications

Chevrolet introduced the S-10 Blazer as a two-door, compact SUV inspired by the S-10 Pickup truck in 1983. Chevy dropped the "S-10" from the vehicles official name in 1995, when the second generation of Blazers came out. The 1994 S-10 Blazer came in several two-wheel-drive and four-wheel-drive trims. All trims shared the same alignment specs. The alignment was not adjustable on the rear end of the 1994 S-10 Blazer because it came with a fixed rear axle. The caster angle, camber angle and toe were adjustable on the font end.
Caster
The caster angle of a vehicles wheels is an imaginary line drawn through the upper ball joint and lower ball joint of the wheel when viewed from the side of the car. If the line were perfectly vertical, the caster angle would be zero. For most cars, the top of the line would fall to the right of the vertical line when looking at the drivers side of the vehicle, meaning that the line would slant toward the rear of the car. This is known as a positive caster.
For the 1994 Chevy S-10 Blazer, the caster angle can range from +1.5 degrees to +2.5 degrees, with the ideal setting being +2.0 degrees and the cross tolerance being +0.5 degrees.
Camber
The camber is the angle that a wheel leans when looked at from the front of a vehicle. If the wheel is perfectly vertical, the camber is zero. If the top of the wheel leans out, away from the engine block, it has a positive camber. If the top of the wheel leans in, toward the engine block, it has a negative camber.
The camber angle on 1994 Chevy S-10 Blazers can range from +0.3 degrees to +1.3 degrees, with the ideal setting being +0.8 degrees and the cross tolerance being +0.5 degrees.
Toe-in
The toe is the angle the wheels of a vehicle are pointed in relation to the centerline of the vehicle. It is rare for a vehicle to be designed so that the wheels are perfectly perpendicular to a vehicles centerline. In most cases, the wheels point slightly toward each other at the front to help relieve pressure on the steering joints and suspension. This is referred to as toe-in.
The toe-in on the 1994 Chevy S-10 Blazer can range from +0.1 degrees to +0.5 degrees, with the ideal setting being +0.3 degrees.
Sunday, December 15, 2013
Impact Tools for Rusted Bolts

A rusted bolt is the result of iron or steel which has been exposed to water and air and has oxidized. When a bolt cannot be removed by using standard hand tools, the entire bolt is probably rusted. Heating a bolt will sometimes loosen it, but if heat is not an option for safety reasons, then impact or pneumatic tools may be the best and easiest way to remove the stubborn bolt.
Impact Wrench and Socket
An impact wrench can be manually operated or powered by electricity or compressed air. When powered by compressed air, the impact wrench is called a pneumatic wrench. To use a manual impact wrench, place the impact socket over the head of the rusted bolt. Hit the other end of the wrench with a hammer while holding down the wrench. The wrench is designed to transform the downward force into a turning motion which will slowly loosen the bolt. Spraying the rusted bolt with penetrating oil and letting it sit for 24 hours may help the process. Electrical or air-powered impact wrenches work the same way but use a trigger to supply the rotary motion. If the threads of the bolt are very rusted, the force of the electrical or air-powered impact wrench may break off the head of the bolt.
Pneumatic Cut-Off Tool
A pneumatic cut-off tool can be used to cut through a small-to-medium size rusted nut or cut off the head of the bolt. The pneumatic cut-off tool is air-powered and has an abrasive disk that rotates at a speed of up to 20,000 rpm. Be sure to wear gloves and safety glasses, as the cut-off tool will create a shower of sparks.
Pneumatic Hammer
A pneumatic hammer and a cold chisel attachment will shear off large bolt heads and nuts. A pneumatic hammer is an air-powered device with a metal piston that mimics the movement of a hammer. The chisel attachment will quickly pound off the head of the bolt or break the rusted nut. Be sure to wear gloves and safety glasses.
Pneumatic Needle Scaler
A pneumatic needle scaler or needle gun can be used to remove rust from around the bolt. A pneumatic needle scaler is an air-powered, hand-held tool that uses little chisels or needles spinning at high speed to remove paint and rust from hard metal. You can use a needle scaler in conjunction with penetrating oil and the impact wrench and socket.
Friday, December 13, 2013
How do I Remove VW Polo Wing Mirror Glass
The VW Polo is a compact car based off of the VW Golf. In the North American market, it is classed as a sub-compact. It actually uses many of the same parts as the Golf, including the side mirrors. While the Polo is a very small car, it can break its side mirrors too. This broken glass must be removed before a new glass mirror can be put in. Luckily, the glass is just held in by glue, so all it takes is some hard scraping.
Instructions
- 1
Park the VW Polo in a well-lit garage or in your driveway during a bright day. Make sure to pull the emergency brake to keep the car from moving while you work on it.
2Use a flathead screwdriver as a pry bar and slip the tip under the lip of the mirror glass. Pry the mirror off with gentle rocking motions along the edge of the glass. Dont worry if the glass shatters. Just work the individual pieces off.
3Scrape the remaining glue off with a razor. Use short scraping motions to get off the big pieces. Once all the lumps are off, soak the tip of a towel in solvent and work it on the back plate of the mirror. This prepares the back plate for the glue that will hold the new mirror in place. The cleaner the backplate, the better the new glue will bond.
What Is the Function of an Instrument Cluster in a Car

The instrument cluster contains the various gauges and indicators that drivers depend on to learn important information on the current status of the automobile. If this information wasnt accessible to drivers, potentially hazardous problems could occur and youd never know.
Function
The function of the instrument cluster is to keep the driver informed with the most current information as they drive. Gauges provide the information for speed, distance, heat and fuel. Indicator lights provide warnings and updates like the check engine light and the low fuel light. Different vehicles have different warnings available.
Identification
The instruments in the instrument cluster are gauges that are circular, and in most cases back lit. The instrument cluster includes the speedometer, fuel gauge, tachometer and odometer; it is located on the drivers side on the dashboard, in front of the steering wheel.
Components
The speedometer tells you how fast the vehicle is moving. The fuel gauge tells you how much fuel is currently in your gas tank. The tachometer provides the driver with the rotation rate of the crankshaft in the engine. The odometer tells you how many miles the vehicle has traveled.
Thursday, December 12, 2013
How to Replace a 1996 Ford Explorer O2 Sensor
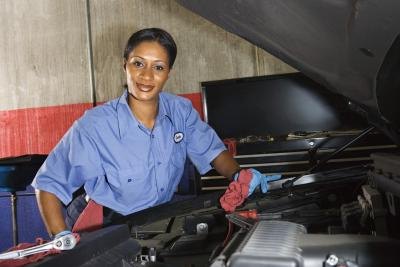
If the gas mileage in your 1996 Ford Explorer has noticeably decreased or the engine is running rough, you may have a failing oxygen sensor. The 1996 Explorer uses four oxygen sensors in the emissions system. The sensors are located to the front and rear of the dual converters and mount straight into the exhaust pipes. You can easily change the oxygen sensors on your truck at home with a few common hand tools.
Instructions
- 1
Raise your Explorer with a jack and position a set of jack stands beneath it for support. Remove the jack once the jack stands are stable.
2Disconnect the electrical connection from the oxygen sensor. Remove the oxygen sensor using an oxygen sensor socket and ratchet. Discard the old sensor.
3Install the new sensor and thread it by hand. Torque the sensor to 30 pound-feet with a torque wrench. Press the wiring connection into place until it clicks.
4Repeat the process on the remaining sensors if needed. Raise the truck slightly with the jack and remove the jack stands. Lower the truck to the ground and remove the jack.
How to Fix a Manifold Leak
Having a manifold leak in your vehicle can cause it to have performance problems. Making sure that the leak gets fixed is important if you want your vehicle performing at its peak. Because the intake manifold is primarily responsible for distributing the mixture of both fuel and air to each of the engines intake ports, fixing these types of leaks is paramount when trying to get the most out of your engine.
Instructions
- 1
Check your vehicle to see if theres any oil leaking from the manifold. Identify where the leak is.
2Disconnect the battery. Remove the nylon fuel rail and the air ducts. Once the fuel rail is removed, press the wires of the injector connectors with your fingers in order to detach them. Use a screwdriver to help make the rubber rings loose. This will aid in removing them easier.
3Use a socket to take the throttle cables, alternator brace and throttle cable cover off. You must also remove from the intake manifold, the throttle body. Once this has been accomplished, you will need to loosen the two nuts that are attached to the EGR pipe and detach that as well. When you do this, youll find a gasket on the EGR pipe, but leave it there for later use.
4Inspect the manifold of your engine. Remove any gaskets that seem to be loose or broken, and replace them. Clean existing gaskets with WD-40, and make sure theyre free of debris by wiping them with the cloth. Replace all of the parts you just took off. This should fix the leak. If it does not, take your vehicle to a professional.
How to Install KA24E Oil Pumps
The KA24E is a four-cylinder 2.4-liter engine that Nissa made from 1988 to 1996. It appears in a variety of Nissan vehicles from this period, such as the Stanza from 1990 to 1992. An oil pump circulates oil through the engine to keep the moving parts lubricated while the engine is running. The oil pump in a KA24E engine consists of an inner and outer gear, which require replacement at the same time.
Instructions
- 1
Disconnect the negative battery cable with a socket wrench to prevent the engine from starting. Remove the front engine cover with the oil strainer tube still attached. Discard the gasket for the front engine cover.
2Remove the retaining screw and mounting bolts from the cover of the oil pump with a socket wrench. Detach the cover for the oil pump from the front engine cover. Remove the inner and outer gears for the oil pump from the gear cavity.
3Clean the mating surfaces of the oil pump cover and the gear cavity with a shop rag. Place the new outer gear for the oil pump into the gear cavity. Place the new inner gear into the gear cavity with the grooved side facing up. Ensure the two gears mesh together properly and pack petroleum jelly into the gear cavity.
4Replace the cover for the oil pump and tighten the retainer screws to between 22 and 36 foot-pounds with a torque wrench. Tighten the mounting bolts for the oil pump cover to between 12 and 15 foot-pounds.
5Install a new gasket for the front engine cover, and replace the engine cover with a socket wrench. Attach the cable for the negative battery terminal and start the engine. Correct any oil leaks.
How to Repair Car Leather with Glue

Although the leather seats are durable, they can still be damaged accidentally. A small hole or tear in the leather can grow and become a bigger problem; therefore it is important to repair the damage to maintain the value of the car.
Instructions
- 1
Cut off any rough areas or loose thread from the edges of the tear or hole. Clean the tear or hole using a cloth and rubbing alcohol. The area above and beneath the tear should be cleaned as well. If the area is losing color, cleaning should be stopped.
2Cut a piece of leather to a patch one inch larger than the tear or hole.
3Apply the adhesive around the edges of the tear and then place the leather patch over the top. Allow a few hours to dry and then lightly sand around the edges to smooth edges and remove excess glue.
4Dye the replacement leather to match the color using a small cloth to apply. Gently rub off any excess dye with a clean cloth.
5Apply leather conditioner over the patch with a small cloth. This will produce a glossy finish to the repair work.
Wednesday, December 11, 2013
How to Put Fog Lights in a 1992 95 Honda Civic

If you own a 1992 to 1995 Honda Civic there will be fog lights installed in the lower front bumper. However, over the years these fog lights have certainly seen their share of wear and tear and it may be time to upgrade to a Euro-styled halogen, or an amber colored lens, or maybe youve had an accident and you simply need new ones. Rather than go to the local garage, this is a perfect do-it-yourself job.
Instructions
- 1
Make sure the engine is off and you have applied the parking brake. Never work on an automobile that is on or that is not securely parked. Let the car cool if it has been running a while. When the hood is cool to the touch it should be safe to begin.
2Lay a blanket under the front bumper and crawl down underneath the front end of your Civic. Look directly behind the drivers side fog light and notice the wiring harness plugged directly into the lights socket. Unplug this wire.
3Use an adjustable wrench to loosen and remove the three mounting bolts holding the old fog light assembly to the bumper. Then pull the entire assembly out and discard of it appropriately.
4Insert you chosen replacement fog light assembly. Secure it in place in the Civics bumper with the supplied mounting screws or bolts. Plug the wiring harness back in. Then repeat this same process on the passenger side light and you are finished.
Tools Needed for Pad Replacement on a PT Cruiser

Brake pads are anti-skidding parts found in disc brakes. They assist in decreasing heat whenever brakes are applied to stop your car by cushioning the brakes, while increasing the longevity of the rest of your brake system. Maintaining your PT Cruisers brake pads requires certain tools for replacement of these pads.
Tools
Youll need a tire iron to remove the lug nuts on your brake rotor, and a metric wrench set to remove the caliper mounting bolts from your brake caliper. A C-clamp is necessary to fully contract the brake calipers piston, and a torque wrench and 19-mm socket are used to tighten the lug nuts on the brake rotor after replacing your brake pads.
Lubricant
Silicone brake lubricant applies to the wheel mounting studs and the bearing hub of your brake rotor, as well as to the caliper mounting bolts, ensuring your new brake pads are snug fits once installed.
Other Items
Youll need a hydraulic jack to hold up the edge of your PT Cruiser, allowing easy access to the brake pads, and a jack stand to hold the hydraulic jack in place, moving it up or down while giving more or less room for removing brake pads. Use a brake fluid siphon to funnel excess brake fluid from your old brake pads during their removal, and use a bowl to catch the excess brake fluid as it flows through the siphon. A pair of replacement brake pads are installed onto your PT Cruiser once the old pads are taken off. Use a cloth to wipe down the wheel mounting studs, the bearing hub on the brake rotor and the caliper mounting bolts, after your old brake pads are removed.
How to Remove an Electric Fuel Pump
Electric fuel pumps force fuel from the fuel tank through the fuel injection system. In older vehicles, before fuel injection systems, the fuel pump was not electric and the fuel was pumped to a carburetor. In newer cars, electric fuel pumps are located in the gas tank, and their removal can be a tricky operation. There are many safety precautions to take before attempting to remove an electric fuel pump from a vehicle.
Instructions
- 1
Put the vehicle in park and set the parking brake. Brace both front tires with safety blocks to ensure the vehicle wont move during the repair.
2Siphon the remaining fuel in the gas tank into a fuel container. The gas tank will need to be nearly empty for this repair. Unscrew the fuel cap on the side of the vehicle and insert a length of hose into the fuel tank. Use a hand pump to start the siphoning action and catch the fuel inside the fuel container.
3Lift the vehicle by placing two jacks at the back corners of the vehicle, one on each side. Using two jacks will provide more support for the vehicle.
4Disconnect the filler and vent hoses from the fuel tank. These will be held on with a clamp.
5Use a socket wrench to remove the bolts that hold the tank to the vehicle on the side that the hose is connected on. Gently lower the fuel tank down a bit. This will allow sufficient space to disconnect all of the wires and connections from the pump to the fuel tank by using wrenches or pliers.
6Disconnect the other two bolts holding the fuel tank in place. Place the tank on the ground.
7Remove the fuel pump by releasing the clamps on the pump. Sometimes the pump is also held in place by screw nuts which require a wrench to remove. Extract the fuel pump from the fuel tank and set the pump aside.
Can an Exhaust System be Clamped Together

Motor vehicle exhaust systems are all either welded or clamped into place. Each has its benefits and drawbacks; some parts will require one or the other.
Types of Exhaust
Auto exhaust systems typically come from the factory welded together. It is with the replacement of pipes, mufflers and catalytic converters that you will see clamps put into use, though some new cars will come with a combination of clamps and welding. The customization of exhaust systems will also result in frequent clamp use, as will older model vehicles mainly because they have had parts changed.
Benefits of Each
The benefits of welding are the complete seal and prevention of leakage that it provides. This reduces pollution and improves engine compression and possible rattle. Clamped exhaust systems make it far easier to replace parts when necessary and remove the cutting and welding elements from the equation.
Considerations
The drawback to welded exhaust systems, especially when it comes to replacement parts, is the potential for cracking should the weld not be done perfectly. The main drawbacks to clamping are the imperfect seals that are formed, the potential for loosening and the loss of compression and pollution into the air.
Combination Systems
Exhaust elements near to the engine including catalytic converter often require welding because of the high pressure exhaust they withstand due to their placement. Clamps tend to be used at the back end of the car.
How to Get a New Key for My Hyundai Elantra

Lost Hyundai car keys can be replaced relatively easy. However, it can be expensive, so is important to explore your options in order to save money. Many of the modern Hyundai keys are laser cut are can be replaced by matching the vehicle identification number, or VIN. Depending on your vehicles year, the Hyundai Elantra keys can either be replaced at a locksmith or at your nearest Hyundai dealer.
Instructions
Instructions
- 1
Look near the base of the drivers side windshield. Locate a slim metal plate along the side of the windshield that will have the VIN number. Record the number and have your drivers license, registration and insurance documents on hand. This will be needed to prove ownership.
2Visit you local hardware store if you are looking to simply make a duplicate of a non-computerized car key. Some later Hyundai Elantra car keys have computerized chips at the base of the key to open the locks. These cannot be made by the hardware store.
3Look for area locksmiths. There are many locksmiths that have the technology and capability to cut and reprogram duplicate car keys. The prices are typically cheaper than the dealer.
4Visit the dealer as a last resort. Visit the Hyundai USA website and click on "Find a Dealer." Enter your zip code and it will reveal a list of the nearest dealers and service centers.
5Call the dealership and ask for the parts department. Arrange a time or appointment to have the key replaced.
Should I Use Umbrella or O Ring Valve Seals


Umbrella Seals Cut Down on Oil Seepage
An umbrella seal scrapes against the valve stem and guide as they are moving. This can mean less oil getting through and less blue smoke on engine startup. These valves are a traditional style and are particularly popular on older cars and rebuilds. Some engines do not have room for umbrella seals.
O-Rings Diminish Excess Oil
O-rings do not scrape the valve stem clear of oil, but they do stop excess oil from falling into the combustion chamber after the engine is shut off. Some people feel this allows the guide and valve stem to remain properly lubricated.
Bottom Line
In an older vehicle or one with worn valve stems, an umbrella seal may help reduce engine smoke without an entire engine rebuild. More important is to get seals made of silicone or other advanced materials. Older seals and cheaper seals are made of nitrite, which corrodes quickly.
Tuesday, December 10, 2013
Do It Yourself Timing Belt Changes for a 2005 Toyota Sienna

The Toyota Sienna is a family minivan that has been in production since 1997, and the second generation of this vehicle includes the 2004 through the 2010 model years. The only engine available for the 2005 Toyota Sienna is the 3MZ-FE model, which has a double overhead camshaft. The majority of the timing belt installation for this vehicle deals with keeping the crankshaft and camshafts in the proper position during the procedure.
Instructions
- 1
Remove the negative battery cable with a socket wrench. Disconnect both windshield wiper assemblies and the panel cover for the front cowl. Remove the hose to the windshield washer reservoir and both cowl top ventilator louvers. Detach the electrical connector for the windshield wiper motor. Remove the outer front cowl panel.
2Raise the vehicle and support it on jack stands. Remove the right front wheel with a lug wrench. Disconnect the pivot bolt, adjusting lock bolt and and adjusting bolt on the accessory drive with a socket wrench, and remove the accessory drive belt. Unplug the electrical connector for the alternator and disconnect the alternator.
3Loosen the adjusting bolt for the power steering pump and detach the drive belt. Disconnect the hose for the coolant reservoir. Remove the engines right mounting stay and moving control rod. with a socket wrench. Disconnect the No. 2 mounting bracket on the right side of the engine.
4Disconnect the crankshaft pulley bolt with pulley holding tool 09213-54015, companion flange holding tool 09330-00021 and bolt tool 91651-60855. Detach the crankshaft pulley from the crankshaft with puller set 09950-50011.
5Remove the lower timing belt cover and disconnect the timing belt guide from the crankshaft with a socket wrench. Remove the wire protector clamps from the upper cover of the timing belt, and disconnect the upper cover. Remove the right engine mounting brace.
6Replace the crankshaft pulley bolt, and rotate the crankshaft clockwise to align the timing marks. The notch on the oil pump must align with the dimple on the crankshaft sprocket. The timing marks on the camshaft sprockets must also align with the marks on the rear timing belt cover.
7Disconnect the timing belt tensioner and timing belt with a socket wrench. Turn the crankshaft clockwise to realign the timing marks if necessary. Install the new timing belt to the crankshaft sprocket and proceed with the installation in a counterclockwise direction. Place the timing belt on the water pump pulley, left camshaft sprocket, No. 2 idler pulley, right camshaft sprocket and No. 1 idler pulley.
8Depress the pushrod for the timing belt tensioner into its housing with tool 981-9807 and secure it in place with a 1.27mm Allen wrench. Connect the timing belt tensioner and torque its mounting bolts to 20 foot pounds with a torque wrench. Pull the Allen wrench from the timing belt tensioner housing to release the tensioner.
9Rotate the crankshaft clockwise two full turns to align the timing marks again, and disconnect the crankshaft pulley bolt. Fasten the engines right mounting bracket with a socket wrench and torque the mounting bolts to 21 foot pounds with a torque wrench.
10Connect the upper cover for the timing belt with a socket wrench. Install the timing belt guide to the crankshaft so that the cup side faces outward, and replace the lower timing belt cover.
11Connect the crankshaft pulley with pulley holding tool 09213-54015, companion flange holding tool 09330-00021 and bolt tool 91651-60855. Tighten the crankshaft pulley bolt to 159 foot pounds with a torque wrench. Install the remaining components by performing steps one through three in reverse order.
How to Replace an In Tank Pump on a 2005 Dodge 2500
A Dodge 2500 is a pickup truck with a carrying capacity of at least 3/4-ton. The 2005 model may have several different engines, most often an eight-cylinder 5.7-liter engine with sequential fuel injection. This requires a fuel pump to maintain the fuel under high pressure. The fuel pump in a 2005 Dodge 2500 is inside the fuel tank, requiring you to remove the fuel tank to replace the fuel pump.
Instructions
- 1
Disconnect the cable from the negative battery terminal with a socket wrench. This prevents the accidental discharge of fuel during the fuel pump replacement. Detach the electrical wiring harness and fuel lines from the fuel pump.
2Siphon the fuel from the fuel tank into a container approved for gasoline. Place a floor jack under the vehicle and support the fuel tank with a floor jack. Disconnect the mounting bolts for the fuel tank with a socket wrench and release the retaining straps for the fuel tank. Lower the floor jack to remove the fuel tank from the vehicle.
3Attach special tool 6856 to the lock nut on the fuel pump and connect a socket wrench to the special tool. Turn the lock nut for the fuel pump counterclockwise with the socket wrench and remove the lock nut from the fuel pump. Lift the fuel pump out of the fuel tank.
4Install the new fuel pump into the fuel tank and attach its lock nut. Fasten the lock nut by turning it clockwise with a socket wrench and special tool 6856.
5Raise the fuel tank in position with the floor jack. Attach the retaining straps to the fuel tank and connect the mounting bolts to the fuel tank with a socket wrench. Lower the floor jack.
6Attach the fuel line and wiring harness to the fuel pump. Connect the negative battery cable with a socket wrench. Fill the fuel tank with fuel, start the engine and check for fuel leaks.
How Replace the Timing Belt on a 2001 Civic
The timing belt is the part of your 2001 Honda Civic that keeps your engine valves operating with the correct rhythm. The timing belt is an absolutely vital part of your vehicles engine. If the belt breaks and the valves are not kept in time, it is likely that your engine will experience a catastrophic failure. For this reason, you should replace the timing belt on your Civic at least as often as recommended by the manufacturer. This will help to ensure your cars engine lasts for a long time.
Instructions
- 1
Disconnect the vehicle battery at the negative terminal. Block the rear wheels, and release the parking brake. Loosen the left-front lug nuts and jack up the front of the vehicle. Place jack stands securely under the Civic for safety. Remove the left-front lug nuts and wheel from the vehicle.
2Pull the splash shield and drive belts out from under the vehicle. Remove the bolts that hold the power-steering pump in the vehicle, but do not disconnect the hoses that supply the power steering fluid. Set the pump out of the way.
3Remove the bolts holding the alternator and valve cover in place. Pull these parts out and set them aside. Support the engine of the Civic with your floor jack. Place a piece of soft material like wood between the jack and the oil pan so you dont damage the pan. Disconnect the upper left engine mount bracket from the engine.
4Rotate the crankshaft counterclockwise until the No. 1 piston is at top dead center; never rotate the shaft clockwise. Disconnect the top dead center sensor once the piston is in place. Remove the side engine mounting bracket from the vehicle.
5Pull off the upper timing belt cover. Hold the crankshaft pulley stationary with a chain wrench, and loosen the pulley bolt using a socket and ratchet. Attach a breaker bar if the bolt is too tight to be removed with a regular ratchet. Pull the crankshaft position sensor out from underneath the Civic.
6Loosen the tensioner bolt for the timing belt. Press the tensioner to release the tension on the belt and tighten the bolt in position where the belt is loose. Slip the belt off of the pulleys.
7Line up the holes on the tensioner pulley and the base. Place a 0.12-inch pin into the holes to keep them aligned. Place the new timing belt around the crankshaft sprocket and then the tensioner pulley and other pulleys it was originally on. Loosen the tensioner bolt, and put a small amount of tension in the belt. Turn the crankshaft two full revolutions. If it will not turn two full revolutions, the timing is off and you have made a mistake installing the belt; remove it and try again until the crankshaft will spin properly. Tighten the tensioner mounting bolt, and remove the pin from the pulley and base.
8Reinstall the engine mounts, valve cover, alternator, power-steering pump, drive belts, splash shield, and wheel in the reverse manner of how they were removed. Reconnect the battery.
9Run the engine to check that it operates properly. If anything seems to be incorrect, check your work for mistakes before attempting to drive the vehicle.
How do I Install Floor Boards on a 78 Harley Electra Glide

The 75th Anniversary 1978 Electra Glide came equipped with what Harley-Davidson calls rider "footboards," or floorboards. The boards were fixed rather than retractable, shaped like half-moons and covered with rubber. Replacements are still available from aftermarket suppliers. The original boards had two female mounts and bolted to a footboard mount. If all of that has disappeared in the last 30 years, both contemporary and original equipment replacement floorboard mounting kits are available.
Instructions
- 1
Remove your right foot peg by turning the bolt head with a socket wrench while you immobilize the nut with a box wrench.
2Bolt the replacement right footboard mounts to the frame of the Electra Glide with a socket wrench, using the nut, bolt and washers that came with your mount. Put thread locker on the bolt threads. Tighten with a breaker bar.
3Bolt the right footboard bracket, if one came with your mounting kit, to the right footboard mount or mounts. In most cases, the components bolt together with a single hex nut and lock washer. Some contemporary footboard mounts may be secured with an Allen bolt.
4Put thread locker on the threads of the exposed footboard mounting stud or the original equipment replacement mounting bolts. Tighten the hex nut with a socket and breaker bar. Alternately, put thread locker on the threads of the Allen bolt of your contemporary footboard mount and tighten with an Allen wrench.
5Bolt the fixed right footboards to the right footboard mount by inserting the two male mounts into the two female mounts. Secure the two pairs of mounts by turning the hex bolt heads with a socket wrench, immobilizing the nuts with a box wrench. Some mounting kits require you to secure the two pairs of mounts by tightening an Allen head bolt with an Allen wrench.
6Repeat these steps to mount the left footboard.
Monday, December 9, 2013
Black Exhaust Soot Problems

Discolored vehicle exhaust is a telltale sign of a foreign liquid inside of the cylinder combustion chamber. Black smoke indicates the air fuel mixture is rich. Black smoke is caused many ways, including issues with the spark plugs or air filter.
Air Fuel Mixture
The combination of air and fuel combusting inside of an engine cylinder creates horsepower and torque. When the air fuel mixture is heavier in gas as opposed to air it is considered rich. A lean mixture is heavier in air.
Spark Plugs
Dirty spark plugs cause black exhaust smoke. Dirty spark plugs do not fire into their specified cylinder at the right time, which forces an unburned air fuel mixture into the exhaust system.
Air Filter
A dirty air filter is a very common reason for black exhaust smoke. Dirty or clogged air filters reduce the amount of air injected into the air fuel mixture while the amount of fuel used stays unchanged.
Performance Affects
Black smoke is an indication your vehicle is not running efficiently. A rich air-fuel mixture burns more gas, reducing fuel efficiency. Drivers may also smell a gas odor.
How to Troubleshoot a Freightliner Air Pressure Sensor
Freightliner tractor trucks are used to transport goods around the country and for other heavy-duty tasks. Air pressure monitors are used to let the driver know whether or not the air pressure in one of the tires is too low for driving. If the Freightliner is driving on a tire in which the pressure is too low, the tire could blow. This increases the chance of losing control of the vehicle. You can troubleshoot an issue with your tire pressure monitor, but it will take a professional to replace it.
Instructions
- 1
Park the Freightliner on a level surface. The weight of the vehicle should be evenly distributed on all of the tires. Park near an air pressure machine, such as at a truck stop or large service station.
2Go to the first tire on your Freightliner that you think may have a defective pressure monitor.
3Make a note of the required pressure from the label on the tire. If you do not know the required pressure, contact the manufacturer or the tire retailer.
4Turn the key inside the Freightliner to the "Accessory" or similar position so the electrical system turns on. The trucks dashboard gauges need to be functioning so you can get a reading from the pressure monitor.
5Locate the valve stem on the tire and remove the cap from the stem. Use a small flat-head screwdriver to press down on the tip inside the valve stem to release the air out of the tire.
6Wait until the tire is about halfway flat and then check the gauges inside your truck. The pressure monitor should be lit. Replace the pressure monitor if it is not lit. Replace the air removed from the tire.
How to Replace a Traction Control Module in a 2004 Mustang
Traction control may be any method of reducing the loss of traction that occurs when the driver applies too much throttle for the current road conditions. It is a secondary function of the anti-lock braking system, or ABS, in a 2004 Mustang. A hydraulic control unit, or HCU, typically has a hydraulic line for each wheel and and an additional line for the master brake cylinder. An HCU with traction control has a sixth hydraulic line for the traction controls brake cylinder.
Instructions
- 1
Disconnect the cable from the negative terminal of the Mustangs battery with a socket wrench. Detach the electrical connector from the ABS control module. The ABS control module is a small, box-shaped component that sits on top of the HCU in the engine compartment. The traction control module, or ABS control module, determines the braking force to apply to each wheel in order to minimize the loss of traction.
2Remove the brake lines from the HCU with a socket wrench. Plug the open ends of the brake lines with shop rags to prevent brake fluid from leaking out of the brake lines.
3Remove the nuts that attach the HCU to its bracket with a socket wrench, and detach the HCU from its bracket. Detach the electrical connector from the brake pump motor.
4Disconnect the mounting screws from the ABS control module with traction control by using a socket wrench. Separate the ABS control module from the HCU.
5Mount the new ABS control module with traction control to the HCU. Fasten the mounting screws for the ABS control module with a socket wrench. Connect the electrical connector for the brake motor pump.
6Mount the HCU to its bracket, and tighten the bracket nuts to 13 foot-pounds with a torque wrench. Remove the shop rags from the open brake lines, and attach the brake lines to the HCU. Tighten the fittings for the brake lines to 14 foot-pounds with a torque wrench.
7Attach the electrical connector for the ABS control module. Connect the battery cable to the negative battery terminal with a socket wrench.
How to Repair a Ford Escape EGR Valve
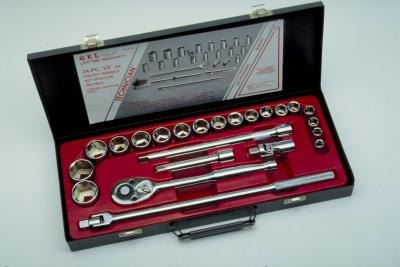
Replacing the EGR valve on the engine of your Ford Escape may become necessary if the valve is not working or damage occurs to the valve or tube. The EGR valve sits on the top of the engine near the rear of the block and looks like a round disk with a small vacuum tube attached to the top center of the disk. A steel tube runs from the base of the valve to the exhaust manifold that threads into the side of the EGR valve.
Instructions
- 1
Open the hood and locate the EGR valve. Remove the vacuum line from the top of the line. It pulls loose if you grasp the boot and pull straight up. Lay it aside.
2Locate the tube coming into the side of the EGR valve from the exhaust manifold. Locate the nut on the tube where it meets the EGR valve and turn it counterclockwise with a wrench and then pull the tube away from the valve.
3Locate and remove the two bolts on the base of the EGR valve with a socket and ratchet and then remove the valve and gasket from the engine. Discard the old valve and place a new valve on the engine, making sure to install a new gasket between the valve and engine.
4Install the two retaining bolts and torque them to 18 pound-feet with a socket and torque wrench. Install the riser tube into the side of the EGR valve and tighten the nut to 30 pound-feet with a torque wrench and crows foot wrench.
5Install the vacuum line on the top of the valve, pushing it straight on until it seats tightly. Close the hood of your escape.
How to Fix a Scuff Mark on a Headlight
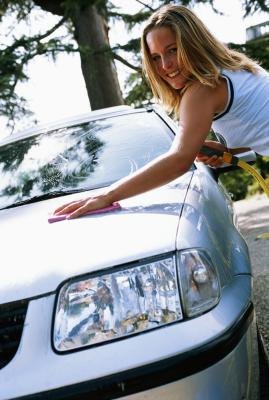
Plastic headlight covers are prone to physical damage due to their prominent position at the front of the vehicle. Proximity to the bumper, front grille and molding offers only marginal protection from contact with foliage and other commonly encountered driving hazards. An object brushing the face of the headlamp can scuff it, as the polycarbonate material is rather soft and easily damaged. Fortunately, the softness of the material simplifies the removal of superficial scratches and scuffs by using common tools and techniques.
Instructions
- 1
Park the vehicle in a well-lit area.
2Apply low-tack tape to the painted area adjacent to the scuffed headlight. Use wide tape or make several passes of narrow tape to make certain you have a generous area of protection around the headlight.
3Wipe the headlight, using a wet rag to remove all foreign material. Scrape any paint residue or debris from the scuff with a fingernail or a piece of 320-grit sandpaper.
4Attach a piece of 320-grit sandpaper on the rubber sanding block. Spray water on the scuff and on the sandpaper. Sand the damaged area by using the sandpaper and block in a direction 90 degrees to the direction of the scuff, and continue until the marks are no longer visible.
5Attach a piece of 600-grit sandpaper on the rubber sanding block. Spray the sandpaper and the scuff with water. Sand the damaged area by using the sandpaper and block in a direction perpendicular to the previous sanding step. Continue sanding until the 320-grit scratches are removed from the headlight.
6Sand the headlight again, using the 1000-grit sandpaper. Sand until the 600-grit scratches are removed from the headlight. Follow again with 1500-grit sandpaper until the 1000-grit scratches are removed from the headlight.
7Apply a small amount of fine buffing compound to a soft rag. Buff the damaged area vigorously by using a circular motion until the damaged area is free of sanding haze and has a shiny appearance.
8Apply a small amount of plastic polish to a soft rag. Rub the damaged area by using a circular motion to give the headlight its final finish.
9Carefully remove the tape. Rinse the area with clean water to remove excess sanding slurry.
Sunday, December 8, 2013
How to Chrome Aluminum
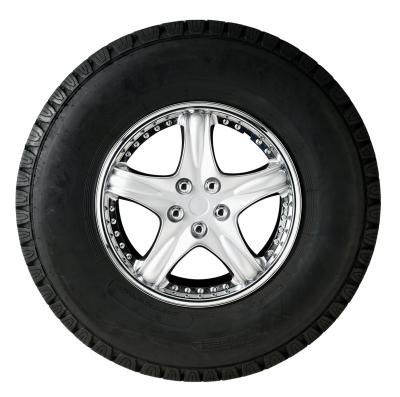
Chrome is a mixture of two metals that are applied to another metal using electricity and chemical processes. Many motorcycle parts and some car parts are chromed to give the vehicle a sharp edge or offset trim versus the base paint color of the vehicle. The chrome process is the same, regardless of purpose, but with aluminum parts its a bit more complicated. This is because aluminum has to be treated first before it can be chromed. Otherwise, the chrome mix wont adhere to the aluminum.
Instructions
- 1
Clean the aluminum part thoroughly with soap and water. If it is covered with grease and oil, use a degreaser to break down the material and wash it off. Use a polisher to take the last bit of dirt off if any is left. Place the aluminum part on a metal hook so you can suspend it without using your hands.
2Treat the aluminum surface with a type of acid to prep it to receive the chrome. Use an acid cleaner, such as sodium hydroxide, to eat the surface slightly. Be careful to wear goggles, a spill apron and acid-proof gloves while treating the aluminum in an appropriate container.
3Pour some etching solution in another container. Dry off the aluminum part from the acid bath and place it in a a second container with etching solution. Allow sufficient time for the etching process to occur on the aluminum parts surface. Wash it off with water when finished.
4Use a third container that can charge the liquid inside with charging plates. Fill it up with sulfuric acid while wearing safety gear. Put the part to be chromed inside the container. Heat the container so that the acid inside reaches approximately 115 degrees. Continue the electrical charging through the liquid. Treat the aluminum for at least 10 minutes. Pull the part out when finished and wash it off with water again.
5Take the washed off part and dip it into a fourth container with heated and liquid copper using a hook. When fully dipped, go to a fifth container and dip the part in liquid and heated nickel. Pull the part out via the hook. Let the metal cool and harden. Wash the part again with water to remove any last impurities and cool the metal completely.
6Place the aluminum part again on a hook and dip it in a last container filled with hex chromate. Let the part soak until fully immersed. Remove the part and let it dry.
2004 Subaru WRX Timing Belt Installation
The Subaru Impreza is a four-door passenger vehicle with all-wheel drive which has been in production since 1992. The WRX is a version of the Impreza that has a turbocharger. The 2004 model features a four-cylinder, 2.0-liter engine with a double overhead camshaft. This engine uses a timing belt to drive the camshafts with the crankshaft, allowing the cylinder valves to open and close in the correct sequence.
Instructions
- 1
Remove the cable on the negative battery terminal with a socket wrench. Disconnect the V-belt and the crankshaft pulley from the engine. Remove the left timing belt cover, right timing belt cover and front timing belt cover in that order.
2Disconnect the guides for the timing belt with a socket wrench if your vehicle has a manual transmission. Remove the No. 1 idler pulley, timing belt and the No. 2 idler pulley in that order. Disconnect the timing belt tension adjuster assembly.
3Push the adjuster rod on the timing belt adjuster down with a constant pressure of 66 lbs. until the end of the adjuster rod reaches the surface of its cylinder. Place a 0.08-inch Allen wrench into the pin hole of the cylinder to hold the adjuster rod in place.
4Install the timing adjuster and tighten its retainers to 29 foot-pounds with a torque wrench. Attach the the No. 2 idler pulley and No. 1 idler pulley in that order. Tighten the retainers for both pulleys to 29 foot-pounds.
5Turn the crankshaft sprocket clockwise to align its timing mark with the timing mark on the oil pump. The double lines on the left intake camshaft must align with the double lines on the left exhaust camshaft sprocket. The double lines on the right intake camshaft must align with the double lines on the right exhaust camshaft sprocket.
6Place the new timing onto the sprockets with the arrow pointing in the clockwise direction. The "A" mark on the timing belt must align with the timing mark on the crankshaft, The "B" mark aligns with the left intake cam shaft, the "C" mark aligns with the timing mark on the left exhaust camshaft, the "D" mark aligns with the timing mark on the right intake camshaft and the "E" mark aligns with the right exhaust camshaft.
7Attach the belt idlers and tighten their mounting bolt to 29 foot-pounds with a torque wrench. Remove the Allen wrench from the cylinder on the timing belt adjuster.
8Replace the guide for the timing belt if your vehicle has a manual transmission. Ensure that the clearance between the guide and the timing belt is between 0.019 and 0.059 inches Tighten the retainers for the timing belt guide to 7 foot-pounds.
9Replace the timing belt covers and tighten their mounting bolts to 3.5 foot-pounds with a torque wrench. Connect the crankshaft pulley and tighten its mounting bolt to 94 foot-pounds. Install the V-belt.
How to Test Exhaust Emission
Exhaust emissions contribute to a large amount of the pollution that now exists in the atmosphere. To reduce the emissions that are released by cars, state laws require that many vehicles be tested in order to determine whether the car meets emission standards.
Instructions
- 1
Visit your states inspection center. A routine part of each inspection is to test your vehicles emissions. The inspection sticker on your mirror will let you know when you are due to have your exhaust emissions and car inspected.
2Wait for your car to be placed on the machine used by the inspection station for the test. An on-board diagnostic test and idle test are the tests used to inspect emission systems. The system is going to check how well your emissions system works and if its up to state standards.
3Find out if your exhaust emissions have passed the test. The inspection station is going to let you know immediately whether your car meets the standards or not.
4Take your car in for repairs if you fail. If your car fails the test, you need to go to an emissions repairman to fix the problem. Once the repair has been done, you can return to the inspection station to test the exhaust emissions again.
How to Repair a Cracked Muffler Pipe
It used to be a lot easier before the days of catalytic converters and resonators and other complicated and integrated exhaust components to repair a cracked muffler pipe. Now the exhaust systems contain many variables that create difficulty when trying to attempt simple repairs. However, with this in mind, the aftermarket exhaust industry has also found some clever ways to work around the complicated systems. If you do indeed have a cracked muffler pipe, you may have some options left before you have to spring out the cash to replace the entire system.
Instructions
- 1
Lift the vehicle safely and securely on a car lift.
2Put on the safety glasses.
3Locate the cracked muffler pipe.
4Put on the welding shield and weld the cracked muffler pipe if the crack is located on a bend in the pipe and a sleeve clamp or buddy sleeve would not be a viable option.
5Use the sleeve clamp to cover the crack in the muffler pipe if the crack is small, located on a the seam of the pipe, or if the pipe is broken in a straight section of the muffler pipe. Wrap the clamp around the cracked pipe, place the nut and sleeve brace on the other side of the bolts, and tighten using the ratchet, socket and a hand wrench.
6Use a buddy sleeve to reconnect a separated muffler pipe. This would only be an option if the pipe was completely broken in half on a straight section of the muffler pipe. The buddy sleeve would reconnect the two halves of the pipe and you would use to exhaust clamps of suitable size to tighten the buddy sleeve to the cracked muffler pipe.
Saturday, December 7, 2013
How to Repair a 2001 Nissan Maxima PCV
The Positive Crankcase Ventilation valve, or PCV valve, in your 2001 Nissan Maxima prevents the crankcase emissions from flowing back into the engine, causing a rough idle and poor-running car. When the PCV valve wears out, replace it to keep your Maximas engine running at its best. Buy a replacement valve from an auto-parts retailer and change it at home in minutes.
Instructions
- 1
Open the hood of the Maxima. Locate the PCV valve on the drivers side of the valve cover, near the firewall. It is a black, elbow-shaped valve with a rubber vacuum hose attached to the end.
2Pull the vacuum hose from the exposed end of the valve. Grasp the top of the valve and pull it straight out of the valve cover.
3Insert the new PCV valve into the cover, pushing it into place until it is secure. Push the vacuum line onto the open end of the valve and make sure it is tight.
4Start the engine and listen for any skipping or rough noises during idle -- they would indicate that you may not have inserted the valve completely.
Error Codes for a 2001 Chevrolet Venture
The Chevrolet Venture is a General Motors (GM) minivan produced between 1997 and 2005, and the 2001 version generally featured a V-6 engine and a four-speed automatic transmission. When something is wrong with your vehicle, you often receive a diagnostic trouble code (DTC), but you need to know the definition of these codes before you can fix the problem. Because this is an on-board diagnostic II (OBD-II) vehicle, it has standardized codes unlike OBD-I vehicles, in which codes were only relevant to vehicle where you obtained the coding.
P0300
This code means that something is wrong with the wiring in your electrical system. If you have replaced a valve body assembly, then you may have stretched a wire harness either too much or just incorrectly or the orientation of the purge control solenoid is incorrect. You should also check the cross injector wires as well as they may be misfiring, and they may misfire all the time you are driving.
P0716
This error code falls under the Unknown or Other category, but it generally means that something is wrong with your powertrain system, which is the system that creates power, including driveshafts, the engine and the transmission. You should check your turbine speed sensor A circuit if you receive this message. This circuit could make your transmission slip if its not working properly. With this error code, you may also receive other DTCs, and your Check Engine light may come on. If you do receive this DTC, have your vehicle serviced as soon as possible.
P0741
This is another powertrain DTC, and you will receive this message only if you have an automatic transmission. The P0741 DTC refers to your torque converter clutch, and this device moves power from a rotating prime mover like your motor or engine to a driven load, which is also rotating. This DTC means that this clutch is stuck in the on position, meaning either your transmission is slipping, or you are having trouble shifting. Take your vehicle for service as soon as possible.
P1811
This error is for manual transmission 2001 Chevrolet Ventures. This is also a powertrain DTC, which means that your transmission is either slipping, or you are having trouble shifting. You may also experience random shuddering, or just overall bad engine performance. With this DTC, you may also receive the P0757 DTC as well, which means that something is wrong with your PCS A electrical system.
How to Remove Steering Wheels in 1990 Chevy Trucks

Removing a steering wheel from 1990 Chevrolet trucks requires a specialized pulling tool. You will need this puller because hammering on the shaft can cause damage. You might have to remove the steering wheel if you need to do repairs on the steering system or components in the dashboard or instrument cluster. Experienced home mechanics can do the job in a few simple steps.
Instructions
- 1
Pop the hood on the Chevy truck and disconnect the negative cable from the battery. Wait two to five minutes so residual power drains out of the truck. This is a safety precaution because you will be working with electrical components. Also, this will temporarily disable air bags, if the truck is equipped with them.
2Pry up the horn pad with a screwdriver. You might want to use a screwdriver with the tip wrapped in tape so none of the screwdrivers edges cause any accidental damage.
3Disconnect the horns grounding wire.
4Remove the nut from the center of the steering wheel with a socket wrench.
5Inspect the shaft of the steering wheel for any markings that denote position. If see any, mark the shaft yourself. It will help you reinstall the steering wheel correctly.
6Fit the pulling tool at the center of the steering wheel. Turn it until the steering wheel becomes detached or can be pulled from from the shaft.
How to Replace a Catalytic Converter On a Ford Escape
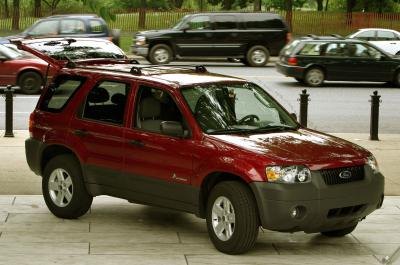
The catalytic converter neutralizes some of the poisonous gases from the exhaust of internal combustion engines common in most modern automobiles. The catalytic converter on the Ford Escape is engineered to work with the Escapes specific engine and exhaust system. In the event a catalytic converter replacement is necessary on an Escape, be sure to purchase an exact replacement for the existing unit. Failure to use the proper replacement catalytic converter will lead to problems with the emissions system.
Instructions
- 1
Be sure the vehicle is cold and slide under the passenger side. Bring along the wire coat hanger, socket set, box wrenches and replacement catalytic converter.
2Wrap the coat hanger around the exhaust pipe behind the catalytic converter and up through the frame to keep the pipe suspended.
3Use the socket set and box wrenches to unbolt the fasteners in the front and rear flanges of the existing catalytic converter. Set the fasteners aside and put the old catalytic converter on the ground, out of the way.
4Position the new catalytic converter between the collector pipe and exhaust pipe and reinstall the bolts into the front and rear flanges with the socket set and wrenches.
5Remove the coat hanger from the frame and exhaust pipe and slide out.
How to Replace a Hyundai Elantra Door Release

A door release latch is prone to break when the latch has not opened all the way, causing it to snap shut while the door is still open. If the door is subsequently shut with a moderate amount of force, the outside of the latch when it slams against the door striker can fault. The result might leave the door no longer closing or releasing properly. Changing the door release latch on a Hyundai Elantra is actually fairly easily, but getting to the latch without ruining your door panel does require some finesse.
Instructions
Removing the Door Panel
- 1
Unscrew the door lock button on the inside of the door.
2Pull down gently on the armrest and remove the two screws.
3Unscrew the inside door handle trim.
4Remove the window handle by pushing in on the panel and then pulling out the clip.
5Unscrew the outside mirror mounting cover, followed by the mount and mirror.
6Remove the weather stripping. Sometimes scraping it off with a chisel or knife is necessary.
7Slide the door panel remover around the sides of the panel to locate the clips. When you find a clip, gently pop it out of place. If your car is older, the panel may be weathered so you should take care not to pull the clip out of the panel.
8Disconnect the speaker wire.
Replacing the Latch
- 9
Unscrew the door latch from the door.
10Disconnect the latch from the door handle rod and the safety lock rod.
11Make sure the new latch is open.
12Reattach the safety lock rod and the door handle rod. Some doors may not have the safety lock rod; in either case, take care not to bend the rods.
13Fasten the latch back to the door frame and make sure it opens and shuts correctly.
14Put the door panel and hardware back on.
How to Retrieve 1993 Toyota Codes

You can retrieve the codes from your 93 Toyota right from your home using an OBD I code reader. This tool can be purchased from any auto parts retailer. "Trouble codes" or "error codes" are alphanumeric numbers that are generated and stored by the vehicles computer for the purpose of troubleshooting malfunctions within the vehicle. The code reader reads the codes and allows you to know what maintenance or repairs are needed. This will save you time and money before visiting a mechanic.
Instructions
- 1
Plug the OBD I code reader into the diagnostic port that is located near the steering column on the drivers dash.
2Put the key into the ignition and turn it to the "II" position, taking care not to start the engine. Wait for the code reader to power on.
3Select "Retrieve Codes" from the code reader. Write down the codes it displays on a piece of paper.
4Select "Retrieve Codes" from the code reader. Write down the codes it displays on a piece of paper.
5Look up the meaning of the codes in the code readers manual. Unplug the reader from the port and turn off the vehicle.
Friday, December 6, 2013
How to Locate an Exhaust Leak

If your "check engine" light comes on, if your engine ticks or if you smell antifreeze, your vehicle might have an exhaust leak. Whether you do the repairs yourself or take your car to a mechanic, locating the leak helps ensure the repair is made correctly and that you dont overspend. Fortunately, it doesnt take long to locate an exhaust leak.
Instructions
- 1
Let the car cool down. When the engine gets warm, the metal expands, hiding small leaks from view.
2Examine the exhaust system without the engine running to see if any holes or slits are visible. Start at the engine and work your way to the tailpipe. Check each connector because they they are most prone to leakage.
3Check the exhaust manifold. Its possible for the exhaust manifold to become warped and cause a leak. This is more common in older vehicles. A simple hand inspection should tell you if anything feels out of place or if any holes have formed. Check the gasket that connects the manifold to the cylinder head. Its common for that gasket to crack and cause a leak.
4Look for holes in the exhaust pipe, especially where the pipe bends over the rear axle. That portion frequently cracks or leaks. Check rusty spots to see if its just surface rust, or if it goes all the way through the pipe.
5Feel for leaks. Have your helper cover the tailpipe by sticking a piece of metal over it and start the engine. This restricts the flow of exhaust gases and pressurizes the exhaust system. Without touching hot metal, carefully move your hands around the outside of the entire exhaust system to feel for any exhaust fumes coming out of strange places.
6Using a mechanics stethoscope, listen for an exhaust leak. The stethoscope isolates the sound of the engine, making it easier for you to hear escaping exhaust fumes.