Saturday, November 30, 2013
How to Add Freon to a 1995 Buick Regal

Air Conditioning does not come stock on every vehicle but some would argue that depending on where you live, its an absolute necessity. Air Conditioners work by pulling the heat of air using a coolant called Freon and then blowing it into the cab of the car. Unfortunately, the Freon is a consumable product like the oil or windshield wiper fluid and will eventually run out, leaving your air conditioner blowing out tepid air at best. When the car is out of Freon, it can be refilled or "recharged," bringing back the cool air.
Instructions
- 1
Locate the air conditioning compressor, next to the battery.
2Back-off the valve handle that comes in the kit and screw it into the refrigerant kit until the rubber O-ring is inside the threaded portion.
3Remove the dust cap from the "low-side" charging connection.
4Attach the quick fitting on the kit hose to the charging connection.
5Start the engine and let it run for about 10 minutes with the air conditioner on taking car that the hoses arent near the engine fan and other moving parts.
6Make sure the compressor is on.
7Turn on the valve handle until you hear the refrigerant release.
8Add refrigerant until the accumulator surface and the evaporator inlet pipe are about the same temperature to touch.
9Place thermometer on the air conditioning vent in the cab. The temperature should read 40 degrees if system is fully charged.
10Close the valve on the canister and store any excess.
11Put dust cover back on the "low-side" charging connection.
How to Install an Engine Guard on a Sportster

There are, it is commonly said, only two kinds of bikers: those who have crashed and those who will crash. Engine guards help protect rider and motorcycle whenever the motorcycle goes over on one side. Most of these accidents are at low speed, or even with the motorcycle stopped, and when that happens the guards dont protect engines so much as everything else on the lower front of the bike. In the kind of crashes that make wonderful stories, the ones that happen on freeways at speed, engine guards significantly improve a riders chances of emerging from the hospital with both legs and both feet. Engine guards are an easy bolt-on.
Instructions
- 1
Remove the three screws and the one flat washer from under the steering head with an Allen socket.
2Remove and discard the two top motor mount bolts, washers and nuts using a socket wrench, a hex socket and an open-end wrench.
3Insert the long screw that was packed with your engine guard through the top motor mount. Use the spacer that came with the engine guard if your Sportster does not have forward controls. Do not use the spacer if you have installed forward controls on your bike.
4Fasten the long screw to the engine mount with the washer and lock nut that came with your engine guard. Ensure that neither the oil pressure switch nor the wiring harness are effected, and then tighten the lock nut with a hex socket.
5Attach the engine guard upper mounting bracket (on top of the engine guard) to the open holes under the steering head. Use the original three screws and washer for Sportsters built after 1994. Use the hardware that came with the engine guard for earlier Sportsters.
6Attach the lower bracket to the engine guard with the included long bolt and hex nut. Tighten the nut to 30 foot-pounds of torque with a hex socket and torque wrench.
7Turn the handlebars all the way right and left and check for interference by the engine guard with the clutch and brake cables.
The 1996 Nissan Quest Alignment Specs
Making sure that the wheels are aligned correctly on your Nissan Quest is important for many reasons. Correct wheel alignment helps to prevent uneven tire wear. It is also necessary so that the vehicle tracks straight and true down the road, without pulling or wandering from one side to the other. The three angles of wheel alignment -- caster, camber and toe -- have specifications for the correct settings.
Caster
Caster is the forward and backward tilt of the upper control arm or strut in relationship to the lower control arm. If the upper suspension component tilts forward, it has negative camber. If the upper suspension component tilts backwards, then it has positive camber. Camber, like other alignment angles, is measured in degrees. The 1996 Quest caster specifications call for a positive camber range of 1/20 to 1 11/20 degrees, with the ideal being 4/5 of a degree of positive caster.
Camber
Camber is the tilt inward or outward of the wheel in relationship to the center of the vehicle. If the wheel tilts outward at the top, it has positive camber. If the top of the wheel tilts inward towards the center of the vehicle, it has negative camber. The range of camber can be from 9/20 to 1 1/20 degrees positive. The ideal measurement is 3/4 of a degree positive.
Toe
Toe is the relationship between each of the wheels in relationship to the center line of the vehicle. If the front of the wheel tilts inward, the toe is negative. If the front of the wheel tilts outward, the toe is positive. Each wheel has its own toe measurement, in addition to the measurement of total toe, which is the sum of the toe from both sides. Toe is also measured by how many inches closer the wheels are in the front of the tires than the rear. The correct setting for the Nissan Quest is 0.08 to 0.16 inches toe-in.
Adjustments
Caster and camber settings on the Quest are not adjustable. If caster or camber are out of specifications, you will need to replace the components that are causing the problem with the suspension. Toe is adjustable by turning the sleeves on the tie rods in the correct direction.
Rear Alignment
The angles on the rear are the same as on the front, except there is no caster measurement. Caster is primarily a measurement concerning turning and since the rear wheels do not steer, caster is not applicable. The rear wheels should have a camber measurement between minus 1/4 degree to 1/4 degree. Rear toe should be from minus 0.16 degree to 0.16 degree. Rear camber is not adjustable, but the toe is. If the camber is off, replace the components that are responsible for the incorrect angles.
How to Perform a Smog Test

A smog test is when a vehicles exhaust system is checked to determine the emission of pollutants and other toxins. Some states require a smog test be performed in order to register a vehicle; however, this usually depends on the age and make of the car, as most newer vehicles do not require a smog test. In order to perform a smog test, you will have to contact your local Department of Motor Vehicles (DMV) to determine your states smog emissions as each states will vary, as will their methods for testing. In addition, the DMV will need to check your smog levels prior to registering your vehicle.
Instructions
- 1
Find out if you are required to have a smog test. If your states DMV sends you a registration renewal notice that says that smog certification is required, or if you are selling your car or bringing it to a new state to be registered, you might need to get a smog test. Most smog tests are good for a couple of years, unless your DMV specifies otherwise.
2Consult with the DMV to find out the requirements for smog tests. Most states require smog tests only if the car is of a certain age or make. Usually older vehicles will be required to take a smog test before they can be registered. In California, for example, vehicles that are six years old or less are not required to get an annual smog check inspection. Some exceptions may apply depending on the type of vehicle you want to register, for example, RV or other commercial vehicles may require a smog test.
3Contact your DMV and make an appointment for a smog test. The DMV will direct you to an approved auto repair shop to schedule the smog test. Ask the representative or go to the local DMV website to find out about the requirements for passing the smog test, such as the emissions level that the smog test must not exceed.
4Bring your vehicle to the approved auto repair shop for the smog test. The mechanic will provide you with a smog certification that you bring to the DMV to complete your vehicles registration.
How to Install Pushrod Guide Plates
There are two schools of thought regarding pushrod guide plates. Some say that using pushrod guide plates is necessary only if the pushrod guides in the cylinder heads wallow out. Others, including those who sell pushrod guide plates, insist on their use in high-performance applications. Both screw-in and press-in rocker studs will accommodate pushrod guide plates. Removing the cylinder head and sending it to a machine shop is necessary when installing pushrod guide plates on a cylinder head with press-in studs, while the owner of a vehicle equipped with screw-in studs can install the guide plates themselves.
Instructions
- 1
Loosen the fasteners that hold the valve cover to the cylinder head by turning them counterclockwise with wrenches from a toolkit. Remove the valve cover from the cylinder head.
2Turn the rocker nuts counterclockwise with a ratchet wrench and socket until they are free of the rocker studs. Remove the rocker arms, keeping them in the same order as removed or marking them with a permanent marker to indicate which stud it came from. Remove the push rods.
3Slip a six-point deep wall socket on a ratchet wrench over the hex head on the base of the rocker studs and remove them from the cylinder head by turning them counterclockwise until they are free of the head.
4Slip the lower portion of a rocker stud into each of the two mounting holes of the pushrod guide plate. Thread the rocker studs back into their holes in the cylinder head, ensuring that the pushrod guide plate is not upside-down and the slots in the guide plate align with the pushrod guide holes in the cylinder head. Refer to the pushrod guide manufacturers instructions for proper positioning of the pushrod guide plates. Tighten and torque the rocker studs to factory specifications.
5Slide the pushrods through the guide holes in the cylinder head, ensuring they sit in the grooves in the pushrod guide plates.
6Reassemble the rest of the parts in the order removed, installing the rocker arms in the same position as before.
Friday, November 29, 2013
How to Replace an Oxygen Sensor in a Nissan Truck
Oxygen sensors have been installed on Nissan trucks since the early 1980s. In 1995 and 1996, an additional sensor was added to monitor the catalyst efficiency. V-6 and V-8 engines in Nissan trucks can now have as many as three or four sensors. The upstream sensors are generally in the manifold(s) (two manifolds with V-6 and V-8 engines) or just below it. The downstream sensors are located just behind the catalytic converter(s). Its possible for a do-it-yourselfer to replace these sensors.
Instructions
- 1
Park the Nissan truck up onto two car ramps and apply the parking brake. Open the hood.
2Place a wheel block behind one of the rear tires.
3Crawl underneath the truck with all the tools and a pair of safety glasses on. Locate the sensor you need to replace.
4Spray the threads of the sensor with a generous amount of penetrating lubricant and allow 5 to 10 minutes to soak in. Repeat this step if necessary.
5Locate the wire harness plug of the oxygen sensor and disconnect it.
6Use an oxygen sensor socket and a flex-head ratchet for upstream sensor removal or a 22mm box-end wrench for downstream sensor removal. Turn the sensor counterclockwise to remove it from the exhaust port. If using the ratchet and sensor socket, place the wire of the sensor into the slot of the socket. For the 22mm wrench, feed the wire through the wrench before placing the box-end side onto the sensor.
7Screw the new sensor into the exhaust port. Most quality replacement sensors will have a slight amount of anti-seize compound on the threads of the sensors right out of the box. Dont get the compound onto the thimble tip of the sensor. If the sensor does not have compound on the threads, its recommended to put a little on them for future replacement repairs.
8Tighten the sensor using the ratchet or wrench. Be extremely careful not to overtighten the sensor. The threads are very delicate and there are only four or five threads, so its easy to strip them out. Tighten them snug only. Plug the sensor wire back into the wire harness.
9Remove the wheel block and lower the truck to the ground. Close the hood and drive the truck as normal. The service engine soon light will reset within 50 to 100 miles, or you can take it back to the parts store and have it reset for you.
How to Find Service Records on an Auto

If you have bought or are about to buy a used car, its in your interests to find out as much about the vehicles history as you can. Its impossible to be completely sure of what youre paying for when you buy a second hand car, but if you can piece together as much of the cars service history and records as you can, youll at least know if theres been any serious issues such as a major collision or mileage fraud.
Instructions
- 1
Ask the dealership or individual youre buying the car from if they have the service history of the vehicle. Professional dealers should be able to provide you with this as a matter of course. If youre buying the car from an individual seller, ask if they have its manual as this will often contain its records.
2Contact the manufacturer of the car with the vehicle identification number. You might find this in the corner of the dashboard below the windshield, on the inside panel of one of the doors or on the chassis underneath the hood. Most manufacturers should be able to provide you with the cars records, especially if its been serviced by their technicians.
3Run a Car Fax search. Car Fax works in a similar fashion to a credit reference agency with background information on cars. Youll need the vehicle identification number and it will cost you $34.99, to access the records of one car, as of November 2010. Car Fax has information on all cars and light trucks manufactured after 1981.
How to Replace a 1999 Chevy Lumina Flasher Relay

Turn signals are lights located at or near the exterior corners of all cars, including the Chevrolet Lumina, that signal the drivers intention to turn. The driver activates either the left or right turn signals via a switch usually found on the steering column. The turn signal lights blink, thanks to a module in the turn signal electrical circuit called a flasher. Sometimes, this flasher malfunctions or wears out. As a result, the turn signals either wont flash or wont come on at all.
Instructions
Test the flasher
- 1
Have an observer stand near the back of the vehicle so they can see both turn signal lights.
2Engage the parking brake if you havent done so already.
3Start the car.
4Apply the brakes. If the observer sees the brake lights working correctly, proceed. If one or both brake lights dont work, you must troubleshoot the brake-turn signal circuit or refer the problem to a certified automotive technician.
5Activate the turn signal, first in one direction then the other. If the observer doesnt see the turn signal lights flash on either side, replace the flasher.
Replace the flasher
- 6
Turn off the car.
7Find the flasher. The flasher is a cylindrical module approximately 1-inch diameter by 1-inch long, plugged into a connector. The flasher is found beneath the driver side dash, near where the steering column passes through the firewall.
8Unplug the old flasher from its socket.
9Install the new flasher.
10Perform the Step 1 test to ensure the new flasher works properly.
How to Remove Car Wheel Covers

Car wheel covers allow you to give some character to your wheels. They come in plastic or metal finish, and they clip over your existing hubcap. If you want to clean the wheel cover, change to a new style or remove a broken cover, youll need to remove the cover from your wheel. This is not challenging since they clip on. Prying the covers off the car wheel takes manual dexterity but very little brawn.
Instructions
- 1
Bend or kneel beside one of your car wheels to begin.
2Slip a flat-head screwdriver underneath the wheel cover. Push the screwdriver forward to loosen the wheel cover. Dont force it if it does not want to come up; you can break plastic wheel covers or bend metal ones.
3Move the screwdriver to another area on the wheel cover. Again push the screwdriver under the wheel cover and pry it forward. Repeat this process at several places along the cover to loosen it from your wheel.
4Grab the cover when it begins falling off the wheel.
5Repeat this process on each wheel to remove all of the covers.
How to Tell the Date on a GT Intake
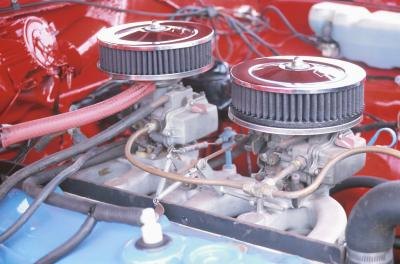
Dating automotive components is an important part of any repair or modification. Minor changes in manufacturing standards over the years can make components from certain eras more or less desirable for specific uses. Fortunately, most major components in Ford engines are stamped with a four-digit date code. Dating a GT intake manifold is as easy as reading and deciphering that code.
Instructions
- 1
Locate the four-digit damp state on the intake. This is generally on the top of the manifold, to one side of the carburetor passages.
2Compare the first digit to the date column of a Ford date code sheet. This letter will correspond to a production year.
3Compare the second digit to the month field of a Ford date code sheet. This will correspond to a month. This digit varies by production year, so it is important to determine the year first.
Thursday, November 28, 2013
How to Check a Yamaha 1982 Motorcycle Starter

The starter on your 1982 Yamaha motorcycle engages the motor to propel the bike when the rider hits the gas. If you are having problems with your 1982 Yamaha starter, you are probably thinking that you need to employ a motorcycle mechanic to get it fixed. The truth is that you can check the starter yourself with very little hassle. Testing this starter will allow you diagnose the problem yourself without spending money on a service shop.
Instructions
- 1
Put a pan under your Yamaha motorcycle and pull the 24mm oil plug from the bottom of the engine panel. Allow the oil to drain from the engine.
2Use a socket wrench to remove the screws holding the left side engine cover onto the motorcycle. The amount of screws holding the cover onto the bike will vary from model to model.
3Go to the front of the motorcycles engine and look for the starter. The starter is a large ring with a bolt coming from the center of it. Use your hands to pull the starter out enough to expose the wiring.
4Use a voltmeter to get a volt reading from the starters red and black wires. If you get a reading less than 12V from the starter, you need to replace the unit.
How to Replace a 2009 BMW 328 Brake Light

The BMW 328 is a perennial favorite of car review sites such as Edmunds, which says the vehicles look, ride and handling are "unmatched by most cars at any price." The brake lights in a 2009 BMW 328 are an important safety feature that alert other drivers when you are ready to stop. These lights should be checked regularly to ensure proper performance. Replacing your 328s brake lights is an easy job that doesnt require any special tools or experience.
Instructions
- 1
Turn off your BMW 328 and set the parking brake. Ensure the light selector switch is in the "Off" position.
2Open the trunk using the interior switch or key-fob remote.
3Use a screwdriver to gently remove the plastic plugs that secure the trim piece to the light assembly. Remove the trim and set it aside.
4Twist the bulb assembly counterclockwise to release it from the light assembly.
5Remove the bulb by pushing it into into the holder and rotating the bulb counterclockwise. Insert the new bulb by placing it in the holder and turning it clockwise.
6Replace the bulb assembly back into the vehicle and reattach the trim.
Hub Bearing Assembly Information

Todays vehicles usually have wheel bearings as part of a whole hub assembly. Wheel bearings are the only part that connects the vehicles body to its wheels. Knowing when they need to be replaced and the tools required can be useful information for vehicle owners.
Identification
There are several ways to identify a faulty wheel hub bearing assembly, most notably if the vehicles ABS warning light comes on. Strange noises, while turning the steering wheel, are another sign of a bad hub bearing assembly. These include growling or humming noises, usually at speeds around 35 MPH.
ABS Sensors
Many of todays vehicles are equipped with anti-lock brakes. Often times these vehicles will have anti-lock brake sensors built directly into the hub bearing assembly. On vehicles where this is the case, if the sensor goes bad, then replacing the entire hub assembly will be necessary to remedy the problem.
Tools
You can save money by replacing a hub bearing assembly yourself if you possess the know-how and the right tools. Some of the tools needed include a floor jack, a flat head screwdriver, sandpaper and a rubber mallet.
How to Reset the Air Bag Warning Light on a 350Z
You can reset the airbag warning light, or SRS (Supplemental Restraint System) light, on your Nissan 350z at home in your garage. If you experience a problem with the air bag, have your vehicle towed to your mechanic to have the air bag system examined and replaced if necessary. If the light is still on when you get the car home, you should turn it off. The good news is you do not need any special tools to do this reset and it will only take a few minutes of your time.
Instructions
- 1
Put the key into the ignition and turn it to the "On" position. Make sure you dont start the engine, however.
2Wait for the SRS light to illuminate on the instrument panel for seven seconds and then shut off. Immediately turn the key in the ignition to the "Off" position. Wait one minute.
3Repeat steps 1 and 2 two more times.
4Start the engine and observe the instrument panel. The SRS light should flash on for about seven seconds and then turn off for good.
How do I Replace 7 3L Diesel Injectors

Ford manufactured its eight-cylinder, 7.3-liter Power Stroke diesel engine from 1994 to 2002. This engine was a complete redesign from Fords previous 7.3-liter engine and featured electronic control with direct fuel injection. This engine is common in heavy Ford trucks, and is the standard engine for the 2002 Ford F350 Super Duty truck with four-wheel drive. The replacement of the fuel injector in this vehicle requires special tools and the removal of additional components to access the injectors.
Instructions
- 1
Disconnect the valve cover with a socket wrench, and unplug the electrical connectors from the fuel injectors. Remove the drain plugs from the oil rail to keep oil out of the combustion chamber while you replace the fuel injectors.
2Remove the retaining screw for the oil deflector with a socket wrench and disconnect the oil deflector. Disconnect the retaining bolt for the fuel injector.
3Remove the fuel injector from the injector bore with Injector Remover No. T94T-9000-AH1 and discard the copper washers. Loosen any debris in the injector bore with Rotunda Injector Sleeve Brush 104-00934-A and clean the injector bore with a shop towel.
4Install new copper washers on the new fuel injectors and lubricate the injectors with engine oil. Push the fuel injectors into the injectors bore to seat the O-rings. Seat the fuel injectors into the injector bores with Injector Replacer No. T94T-9000-AH2.
5Install the oil deflector and tighten its retaining bolt to 108 inch-pounds with a torque wrench. Replace the drain plug on the fuel rail and tighten it to 96 inch-pounds. Install the drain plug on the oil rail and tighten it to 53 inch-pounds. Connect the wiring harness for the fuel injector and install the valve cover with a socket wrench.
Wednesday, November 27, 2013
How to Install a Tail Light Relocation Kit on A Harley Davidson

Harley riders usually need to relocate their tail lights before they can install saddlebags on their motorcycles. The motor company has engineered many of its bikes so that the purchase of a set of saddlebags also requires the purchase of a kit to relocate the taillights, so the saddlebags will fit At that point, many casual riders give up and have the dealer handle the relocation, which is straightforward. Anyone attempting a taillight relocation needs a well-equipped workshop, patience and dexterity, but the job is not difficult.
Instructions
- 1
Elevate the motorcycle on a motorcycle jack. The wheel must hang down so you can access the inside of the fender.
2Unscrew the rear seat stud with an Allen wrench. Remove the seat. Disconnect the black battery cable from the negative battery terminal.
3Remove the plastic plug from the tail lamp access hole inside the rear fender.
4Remove the turn signal wires and connectors from the inside of the tail lamp housing, then remove the turn signal wires from the clips inside the fender. Separate the four-way turn signal socket housings from the rear lighting harness pin housings.
5Unplug the gray four-way tail lamp connector from the mating connector in the tail lamp housing. Mark for reference with masking tape and a pen and remove the wires from both socket housings.
6Remove the screw at the front of the fender mounting bracket, as well as the screw and washer at the rear of the fender mounting bracket. Remove the turn signal lamp, fender rail and mounting bracket from the Harley.
7Cut one piece of heat shrink tubing into two equal sections with scissors. Slide one piece of the tubing over the turn signal wires, all the way up to the lamp housing on each side of the motorcycle. Use a heat gun to shrink the tubing.
8Install the turn signal lamp wires through the small hole in the recess cover. Position the cover into the recess in the turn signal housing.
9Loosely attach the hex nut and lock washer onto the turn signal relocation bracket. Loosely attach the turn signal lamp and recess cover onto the threaded end of the turn signal relocation bracket.
10Align the relocation bracket with the rear of the fender support. Fit the round pad into the mating hole in the support.
11Install the rear fender rail with your original equipment hardware or the hardware specified in your saddlebag mounting instructions. Install the turn signal relocation bracket to the rear fender and fender rail.
12Aim each turn signal lens straight back. Tighten the hex nut and lock washer with a wrench. Complete all steps for both sides of the motorcycle.
13Install the turn signal wires and terminals into each cavity of the turn signal socket housings.
14Route the turn signal wires under the turn signal relocation bracket and under the rear fender edge on each side of the vehicle. Connect the turn signal socket housings to the pin housings on the rear lighting harness.
15Plug the gray, four-way tail lamp connector on the rear lighting harness into the mating connector in the tail lamp housing under the fender. Gently push the turn signal wires and connectors into the cavity inside the tail lamp housing and install the plastic plug into the tail lamp access hole in the rear fender.
16Route the turn signal wire under the signal relocation bracket and secure it to the bracket with a cable tie.
17Install your saddlebags or re-bolt the fender rails to your fender using the original hardware.
1999 Ford Taurus Ball Joint Torque Specs

The Ford Taurus is a mid-sized family sedan first introduced in the early 1980s. The Taurus uses a conventional front suspension, with ball joints connecting the knuckle to the wheel hub. The ball joints carry the weight of the front of the vehicle and must meet specific torque specifications when replaced.
Testing and Inspection
Raise the vehicle until its wheels fall to full down position and are off the ground. Have an assistant grasp the lower edge of a tire and move the wheel assembly in and out. As the wheel is being moved in and out, observe the upper end of the wheel spindle and the rear suspension arm and bushing. Any movement will indicate abnormal joint wear.
Torque Specifications
The torque specification for the front lower and upper ball joint nut is 68 to 92 Nm, or 50 to 67 ft. lbs.
Part Replacement
The OEM part number for a ball joint for a 1999 Taurus is 5F1Z3050A. This part is supplied by Ford and available at dealerships.
How to Tune a Carburetor on a Motorcycle

Motorcycle carburetors take in air and mix it with fuel. Numerous factors can throw a motorcycle carburetor out of tune. Typically, motorcycle carburetors are shaken out of tune by vibration. Manufacturers like Mikuni, Keihin and S & S sell original equipment and aftermarket carburetors for numerous motorcycles. Details vary but tuning principles are the same for all these devices. Here, specifically, is how to tune the carburetor Harley-Davidson has used since 1989.
Instructions
- 1
Remove the air cleaner cover with an Allen wrench. Loosen the air cleaner with a Torx wrench.
2Disconnect the two breather tubes from the top of the air cleaner with your hands. Remove the air cleaner. Remove the air cleaner backing plate with a socket wrench.
3Put the motorcycle in neutral. Start the motorcycle and let it run until the engine is hot. Leave the engine running during the following procedures.
4Spray short bursts of aerosol carburetor cleaner into the venturi (the open mouth) of the carburetor. Allow the engine to stumble and recover. Then repeat.
5Turn the idle speed adjuster screw next to the throttle cam with a flat head screwdriver until the engine idles smoothly without stumbling at the lowest possible engine revolutions per minute. Turn the screw clockwise to reduce idle speed and counterclockwise to increase idle speed.
6Turn the low speed, fuel-air mixture screw on the bottom of the carburetor 1/8 clockwise. Wait five seconds for the idle to stabilize.
7Continue to turn the low-speed screw clockwise 1/8 turn at a time with a five-second pause between turns until the engine stumbles and drops revolutions per minute. When the engine stumbles, turn the low-speed screw counterclockwise 1/8 turn.
8Wait five seconds, then open the throttle. The engine should idle cleanly and respond without stumbling when you open the throttle.
9Repeat adjustments to the idle speed adjuster screw and the low-speed, fuel-air mixture screw as needed until the engine idles cleanly at low speed and responds without stumbling when you open the throttle.
10Turn off the motorcycle. Reinstall the air cleaner backing plate, the air cleaner, the breather tubes and the air cleaner cover.
How to Loosen an Alternator Pulley Nut

An alternator provides power to your vehicle while charging your vehicles battery. The alternator turns via a belt that runs over the top of a drive pulley. When changing a bad alternator or installing under-drive pulleys, you will need to remove the pulley from the front of the alternator. A large nut located on the front of the pulley secures it to the alternator shaft. Loosening the alternator nut allows you to separate the drive pulley from the alternator.
Instructions
- 1
Spray penetrating oil on the alternator nut. Allow the penetrating oil to soak on the nut for two to three hours before continuing.
2Put a heavy leather glove on your non-dominant hand.
3Match an impact socket from a socket set to the nut located at the front of the alternator pulley. Attach the socket to an electric impact wrench.
4Hold the alternator shaft directly behind the pulley with your gloved hand. Slide the socket attached to the impact wrench onto the alternator nut. Set the direction of the impact wrench to counterclockwise.
5Pull the trigger of the impact wrench as you apply pressure to the alternator shaft with your hand. Continue until the nut breaks loose of the pulley.
How to Remove the Driveshaft on a Mercedes E320 CDI
The Mercedes E320 CDI was the first BlueTec diesel Mercedes sold in the U.S. A 3.2-liter diesel engine powered the rear-wheel drive sedan through a six-speed automatic transmission. A driveshaft transfers toque from the transmission in the front of the car to the differential in the rear. However, the driveshaft is exposed on the underbody and can be damaged by debris. A damaged driveshaft must be replaced.
Instructions
- 1
Drive or tow the Mercedes E320 CDI someplace flat and out of the way. When the driveshaft is removed, the car will be undriveable. The car can be pushed but it will be difficult because the E320 weighs close to 2 tons. Place the Mercedes into park and then turn the car off. Use a car jack to lift the front and rear corners of the E320. Then use jack stands to keep the corners elevated.
2Locate the driveshaft running down the center of the undercarriage. The driveshaft is connected by flex joints at the front and rear of the shaft. The flex joints in turn are connected to the transmission and rear differential with six bolt flanges. Use the car jack to support the transmission end of the shaft first. Then unbolt the six bolts securing the transmission end flex joint. Once the bolt flange is free, lower it to the ground with the car jack.
3Raise the car jack up to support the differential end of the driveshaft. Then unbolt the six bolts securing the flex joint to the differential. Lower the driveshaft down with the car jack. Roll the driveshaft out from under the sedan and place it to the side. If you install a new driveshaft, just repeat the removal process in reverse.
Tuesday, November 26, 2013
How to Change a 1991 BMWs Blower Motor
The blower motor on a 1991 BMW pushes the air from the air conditioning compressor and the heater core out through the vents in the dashboard, heating or cooling the interior of the vehicle. Should the blower motor fail, the climate controls will fail with it. To fix the problem, you can change out the failed blower motor for a new one, a process that should take under 30 minutes to do.
Instructions
- 1
Pop the hood on the BMW. Remove the weather stripping at the firewall with your hands, then cut the zip ties that hold the wiring to the motor cover with the side-cutting pliers. Unbolt the cover from the motor with the 3/8-inch ratchet and socket.
2Unbolt the retaining straps from the blower motor with the 3/8-inch ratchet and socket. Unplug the wiring to the motor with your hands, then take off the clamp holding the blower motor in place. Pull the blower motor out of its mount.
3Install the replacement blower motor into the mount and reengage the clamp. Plug the wiring into the blower motor and then reinstall the fan cover and the straps with the 3/8-inch ratchet and socket.
4Reinstall the blower motor cover with the 3/8-inch ratchet and socket. Reinstall the wire across the cover with the zip ties and push the weather stripping back onto the stock area.
Type of Oil Used in Electric Motors

Electric motors convert electrical energy into mechanical energy, and are incorporated in different commercial and household applications. These motors require specially developed lubricating materials called motor oils for their continuous and cohesive performance. There are different categories of motor oils, which find their respective distinction mainly on the basis of different chemical compositions and sources of origin. In other words, all categories of motor oil perform similar functions of lubricating the electric motor components, but their categorization is made on the basis of their compositional properties, which define their level of efficiency within an electric motor.
Conventional Oils
Conventional motor oil is obtained as crude oil, or unrefined petroleum, from the ground, and is further processed through different chemical additives in the refinery. This type of oil is viscous and has a pungent odor, and is specifically used in commercial and industrial electric motors. Conventional motor oil is not refined on the molecular levels, which means it always contains organic and inorganic impurities, and, for this reason, is not employed in sensitive or low-power electrical motors.
Synthetic Oils
Synthetic motor oil also originates from crude petroleum and is refined, or processed, through extensive chemical procedures. However, this type of oil is constituted by uniform organic molecules and contains a minimum level of impurities. For this reason, synthetic motor oil has minimal odor and can be used in both high- and low-power electric motors. This is in contrast with conventional motor oils, which is constituted by variable molecular sizes and large amount of organic impurities. Some common applications of synthetic motor oils include automobile electric motors, jet engine motors, household water pumps and motorcycle engines.
Semi-synthetic Oils
Semi-synthetic motor oils are composed by chemical mixing of synthetic and different crude oils in appropriate ratios. This type of oil is less costly than fully synthetic motor oil, and can be used as a cheap replacement in both low- and high-power electric motor applications. Semi-synthetic oil is also known as synthetic blend, and is usually composed within ratios of 30 to 40 percent synthetic and 60 to 70 percent crude organic oils. This proportion indicates the performance level of semi-synthetic motor oils, which increases with increasing ratio of fully synthetic oil within.
Bio-base Oils
Bio-base oils have long been used as lubricants and heat-absorbing viscous materials. This type of oil includes all biologically existing organic liquids, which have been used as fuels as well as lubricants in different household tasks. However, this type of oil is not used in industry for lubricating electric motors, and is specifically employed in the form of grease or wax in small household electric motor applications like fans, hand blowers and miscellaneous power tools.
How to Install Conical Valve Springs

Conical valve springs return an engine cylinders valve to its neutral position after it has been moved by a cycle of the engine. The purpose of their tapered shape is to provide a progressive action. A straight spring compresses evenly, but with a conical spring, the narrower portion is more difficult to compress that the broader section. This means that the more the spring compacts, the greater the force required to compress it even further.
Instructions
- 1
Remove the cylinder head, rocker arms and push-rods from the side of the engine on which you plan to work first. set all the components aside, noting which bolts and fixtures go with which part.
2Unscrew the first spark plug using the spanner. When you feel it disengage from the thread, remove the spanner and use the magnetic grabber to lift it out of the cylinder. With the tops of the springs exposed, the locking nuts compressing the spring are now visible.
3Make sure the valve-removal tool you have is compatible with conical valve springs as well as straight ones. Apply the lever or stud-mount valve-removal tool to the top of the spring and compress it downward. Compress the spring just enough to allow you to access and remove the lock from the center of the spring. Any more risks binding the coils of the spring together.
4Undo the locks and carefully lift them out of the spring, the magnet may be useful for this. The old springs will now lift freely out of the chamber. Place the new springs into the chamber, narrow end at the top, and replace the retainer disc over the top.
5Compress the spring with the lever or stud-mount tool and replace the lock in the top of the retainer. Repeat with all other springs.
How to Find and Replace the Blower Motor Resistor on a 2007 Nissan Versa
When a blower motor resistor fails, the blower motor will only operate in one speed; this is often the first and only sign of a faulty blower motor resistor. This malfunction occurs because the resistor regulates the amount of current flowing to the blower motor in relation to the position of the fan speed control knob. Since the blower motor switch in a 2007 Nissan Versa is located behind the brake pedal assembly, a number of components must be disassembled in order to perform this repair.
Instructions
Removal
- 1
Shut off the engine and open the hood. Disconnect the negative battery terminal with a metric box-end wrench.
2Open the drivers side door and remove the fuse panel cover. Remove the screws holding the lower panel finisher with a metric nut driver. Pull the lower panel finisher away from the dashboard until it pops loose. Disconnect the diagnostic data ports electrical connector and remove the finish panel from the vehicle.
3Disconnect the accelerator pedal position sensors electrical connector. Remove the stop lamp switch from the brake pedal assembly by gently popping it loose.
4Remove the snap and clevis pins from the brake booster with a small flat-head screwdriver and needle-nose pliers. Remove the nuts holding the brake pedal assembly bracket to the vehicle with a metric socket and a ratchet. Remove the brake pedal assembly from the vehicle.
5Locate the blower motor resistor. It is situated directly behind the brake pedal assembly on the rear of the firewall. It is held in place by two screws and is rectangular in shape. Disconnect the blower motor resistors electrical connector. Remove the screws holding the blower motor resistor to the vehicle with a screwdriver and remove it from the vehicle.
Installation
- 6
Set the new blower motor resistor in place and reinstall its retaining screws. Reconnect its electrical connector.
7Inspect the brake pedal assembly for deformations, bends, cracks, and any sub-standard condition. Measure the lapping length of the sub-bracket and side plate with a metric caliper. Ensure that the length is at least 6.9 mm. If any of these conditions are out of specification, replace the brake pedal assembly before proceeding.
8Set the brake pedal assembly in place and reinstall the nuts holding the brake pedal assembly to the vehicle with a metric ratchet and socket. Reinstall the snap and clevis pins to their original location.
9Reinstall the stop lamp switch into the brake pedal assembly. Check the brake pedal assembly to ensure that it operates properly.
10Set the lower panel finisher into place and press down on it until it snaps into position. Reinstall the lower panel finisher screws. Reconnect the diagnostic data ports electrical connector and reinstall the fuse panel cover.
11Reconnect the negative battery terminal. Turn on the ignition and test the blower motor to ensure that it operates properly at all speeds.
How to Connect Rod Journal Measurements
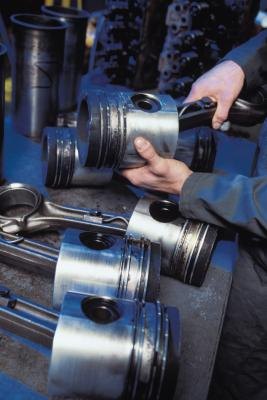
Connecting rods connect the piston to the crankshaft; as the crankshaft rotates, the connecting rods move the piston up and down in time with the rest of the engine. A connecting rod journal is where the connecting rod attaches to the crankshaft, making the journal a crankshaft feature. Measuring connecting rod journals is an important part of an engine rebuild, helping you determine the proper size connecting rod you need. To measure connecting rod journals, the crankshaft must be already removed from the engine.
Instructions
- 1
Locate the connecting rod journals on the crankshaft. The number of connecting rod journals depends on the number of cylinders. A four-cylinder engine has four, and an eight- cylinder has eight. Journals are smooth, polished surfaces, located in between the crankshaft counterweights. Crankshafts also have main journals, allowing them to rotate. Connecting rod journals are the smaller journals.
2Feel the journals with your fingers, and determine if they require machining. Journals should be polished and smooth. If theyre rough, pitted, or rusted, they need to be machined by a professional prior to measuring, as machining changes the journals measurements.
3Use a micrometer to measure the connecting rod journal. Open the micrometer by turning the handle until the journal fits inside. Place the micrometer at the journals center, turning the handle until it closes on the journal.
4Record the measurement given. The measurement is found on the micrometer sleeve, directly in front of the turning handle, or thimble. Connecting rod journals are commonly measured in millimeters.
Monday, November 25, 2013
How to Replace the Water Pump in a 1999 Mirage 1 5L
The Mirage is a subcompact car that Mitsubishi Motors made from 1978 to 2002. The 1999 model most often had a 4-cylinder 1.5-liter engine with multi-port fuel injection. The water pump in a 1999 Mitsubishi Mirage is located on the front of the engine block. You can access it from the top of the engine compartment.
Instructions
- 1
Let the vehicle to sit overnight to ensure the engine and radiator fluid are cold.
2Disconnect the cable for the negative battery terminal with a socket wrench. Put a container under the radiator and open the radiator drain. Wait for the radiator fluid to drain into the container. Seal the container and replace the radiator drain plug.
3Remove the undercover for the engine with a socket wrench. Disconnect the bolt from the power steering hose and detach the hose. Remove the drive belts on the engine and support the engine with a floor jack. Disconnect the bracket for the engine mount.
4Disconnect the timing belt with a socket wrench. Remove the bracket for the power steering pump and the brace for the alternator with a socket wrench.
5Disconnect the mounting bolts for the water pump. Detach the water pump from the water inlet pipe. Remove the gasket from the water pump and discard it.
6Clean the gasket surfaces with a shop rag and wet the new O-ring with water. Place the O-ring into its groove on the water inlet pipe. Install the new water pump to the water inlet pipe and tighten its mounting bolts to 17 ft. lbs with a torque wrench. Complete the water pump installation by performing steps 2 and 3 in reverse order.
7Fill the radiator with coolant and connect the cable for the negative battery terminal with a socket wrench. Start the engine and allow it to idle until the thermostat opens. Allow the vehicle to cool and adjust the coolant level in the radiator to the correct level.
Common Symptoms of a Bad Oxygen Sensor

All vehicles come equipped with small engine components called engine oxygen sensors. Many different types of oxygen sensors perform an array of different functions, and a faulty oxygen sensor can wreak havoc on engine operation and performance.
Rough Engine Idle
Vehicle engines that have a bad oxygen sensor often run irregularly or roughly. Oxygen sensors can control or contribute to many different engine functions, including fuel/air mixture, engine timing and engine combustion intervals. A faulty oxygen sensor can disrupt any of these things and cause a rough engine idle.
Engine Missing
A bad oxygen sensor can impede the air/fuel mixture of an engine or interfere with the engine combustion, both of which can cause an engine to miss, or run irregularly. An engine miss is normally most pronounced at idle or at lower engine speeds; a faulty oxygen sensor can inhibit the normal fuel delivery/combustion within an engine and cause a miss.
Engine Pinging
If a bad oxygen sensor is aligned with the ignition system on a cars engine, it can retard or advance engine ignition timing, which can cause an engine to ping. Pinging occurs when an engines combustion gases are ignited at the wrong times.
Poor Gas Mileage
Depending on the type and/or location of a faulty oxygen sensor, the fuel-delivery and the fuel-combustion systems can be thrown off or made irregular by a faulty oxygen sensor. If too much fuel is injected into an engines cylinders or a faulty oxygen sensor disturbs the delicate air/fuel mixture of an engine, gas mileage will suffer.
Increased Vehicle Emissions
Vehicle oxygen sensors play a critical part in keeping a vehicles emissions within certain parameters. A vehicle can fail a state-mandated smog test because a bad, or faulty, oxygen sensor will not accurately measure various engine ratios or air/fuel mixture concentrations or adjust certain engine operations accurately enough to keep a vehicles emissions in check.
Jetta Exhaust Removal
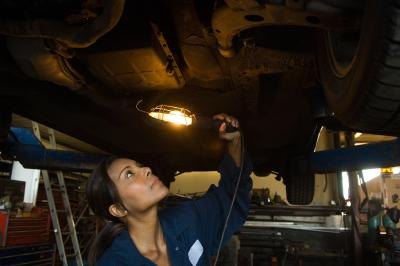
The method of removing the exhaust manifold in a Volkswagen Jetta varies greatly, especially based on the type of engine the car has. No matter what the case, it is a complex procedure that should only be attempted by someone with extensive knowledge of the exhaust system. Consult with your mechanic before taking on this task.
1.8 Liter Engine
To remove the Jettas engine cover, pry off the plastic caps covering the screws, remove all the retaining nuts and detach the cover. Next, remove the air intake duct by squeezing the tabs on its hose clamp. Take off the cowl cover by disconnecting the windshield wiper arms, pulling off the weatherstrip at the covers front end, removing the pollen filter cover and releasing the clips on the covers sides.
On a 1.8 liter engine, you will need to remove the turbocharger and all of its related components. Drain the engine coolant into a container by removing the plug at the radiator and then at the engine oil cooler. Raise and support the Jetta on jack stands and then remove the engine compartment undercover. Remove the nuts attaching the exhaust pipe to the turbocharger. Next, lower the exhaust pipe by removing its support bolts. Disconnect all hoses and parts connected to the turbocharger; this includes the support bracket, the vacuum hose from the wastegate actuator, outlet pipe and elbow, the coolant return pipe and the oil supply pipe. Locate and remove the heat shield, then take off the bolts connecting the turbocharger to the manifold lower and tilt the turbocharger so you can disconnect the coolant supply pipe, allowing you to completely disconnect the turbocharger.
Once you have the turbocharger off, you can remove all of the nuts and bolts for the manifold and detach it with its gasket.
2.0 Liter Engine
For 2.0 liter engines, you may need to remove the oil dipstick when you detach the engine cover. After taking off the air intake duct (disconnect the accelerator cable with the duct) and cowl cover as described above, remove the upper intake manifold--clamp off the coolant hoses connected to the throttle body with hose clamps, disconnect the hoses and electrical connectors along with the ones connected to the upper manifold, and remove the bolts at the rear of the manifold for the warm air deflector plate. Disconnect the vacuum hose leading to the brake booster, and loosen each manifold bolt a quarter turn at a time with the wrench until they are all loose. You can then remove them and the manifold with the throttle body attached.
Next, take off the hoses on the secondary air injection control valve. Raise the cars front end and support it on jack stands, then unbolt the inner CV joint on the right side, pushing the axle out of the way and securing it with a wire. Disconnect the electrical connectors to the oxygen sensor and the one to the front O2 sensor; detach the latter from the manifolds retaining bracket.
Finally, separate the air injection pipe by disconnecting its union nuts from the fittings on the manifold and the secondary air injection control valve. Remove the warm air deflector plate, then remove the exhaust manifolds nuts and bolts and detach it with the gasket.
Why Did My Head Gasket Fail
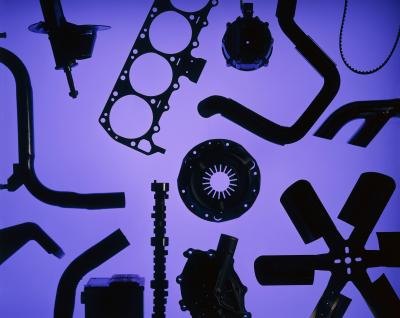
When a head gasket fails, coolant begins to leak into the crankcase and mixes with the engine oil. This mixture creates a milky-like substance that will coat anything and everything it touches. Coolant will ruin the crankshaft and connecting rod bearings, and the milky remnants of the mixture will clog oil passages, causing precisely oiled components to fail. In most cases, a blown head gasket can be prevented if the driver knows what leads to head gasket failure.
Overheating
Overheating is the No. 1 cause of head gasket failure. When the engine overheats, the engine head and block will expand and can crush the head gasket, creating an immediate leak. Even if the engine doesnt get hot enough to warp the cylinder head, excessive operation at high temperatures can cause the material on the gasket to become brittle and crack, creating a number of leaks.
Preignition
Preignition puts serious strain on the head gasket and is commonly associated with an overheating engine. Preignition occurs when hot spots develop within the combustion chamber, which become a source for ignition. When this happens, combustion will occur before the spark plug actually fires. The force created by the premature combustion puts undo stress on the head gasket and over time will cause it to fail.
Detonation
Detonation, also known as spark knock, is essentially improper combustion. When this happens, multiple flames are created inside the combustion chamber instead of one, causing a sudden spike in pressure within the combustion chamber. This extra pressure causes excessive stress to the head gasket as well as the pistons, valves and piston-connecting rods and is accompanied by a pinging noise during acceleration. Detonation is commonly caused by fuel with a low octane rating, a problem within the exhaust gas recirculation system and over-advanced spark timing.
Improper Cylinder Head Installation
If major engine work was recently performed and the cylinder head had to be removed, it is possible the mechanic doing the work failed to torque the head bolts properly or failed to torque the head bolts in the proper sequence during installation. Head gaskets require a certain amount of pressure to be maintained between the cylinder head and the engine block to load and keep a good and tight permanent seal.
Preventative Measures
Always keep an eye on the temperature gauge. Any time overheating begins to occur, shut the engine down, and diagnose and repair the problem. If you notice spark knock or pinging while driving, increase the octane rating of your fuel and check the exhaust gas recirculation system for faults. On older cars, adjust your air-to-fuel ratio accordingly. It is also very important to keep up on the maintenance of the engine ignition system; if your vehicle uses a distributor system, replace the cap and rotor according to the manufacturers maintenance schedule and always replace your plugs and wires every 15,000 miles or so for optimal performance.
Edelbrock Carb Specifications
Carburetors help to regulate air and fuel flow through an engine. Edelbrock carburetors have been a household name since the early 1930s and 1940s. Edelbrock carburetors today are designed to fully operate as soon as you install them into your engine. They are cast from aluminum, which makes them lighter than other brands of carburetor. Each carburetor also features a design that keeps gaskets or seals above the fuel line to reduce the risk of fuel leaks.
Performer Carburetors
The Performer series of carburetors do not have backfiring issues because they use metering rods. The rods also allow you to change the fuel and air mixture without disassembling the carburetor. With any of the Performer carburetors you can select a manual or electric choke. This series gives you the option of carburetors that have a measurement of 500, 600, 750 or 800 CFM, or cubic feet per minute.
Thunder AVS Carburetors
The Thunder series of carburetors has an AVS system, or an adjustable valve secondary. This feature allows you to adjust the carburetor by tightening or loosening only one screw. By adjusting the screw, you are adjusting when the carburetor opens depending on what the engine needs. As with the Performer series, you can select either a manual or electric choke. The Thunder series is available in 500, 650 or 800 CFM sizes.
Marine Vehicle Carburetors
The Marine series is designed specifically to be used on boats. You can select between 600 and 750 CFM sizes. These carburetors do not have vacuum ports, and adhere to the safety standards set forth by the Coast Guard. The Marine series is coated in Teflon to protect it from salt and fresh water. You only have the option of an electric choke with the Marine carburetor.
94 Two-barrel Carburetors
The two-barrel carburetors are specifically for restored vehicles or hot rods. These carburetors are designed for small caliber engines to meet the original carburetor specifications.
Sunday, November 24, 2013
Dielectric Vs Silicone Grease
Silicone and dielectric grease are used to seal objects from foreign materials and dust. Both materials are used in electrical applications because of their resistance to high temperatures and electrical charges.
Appearance
Dielectric and silicon grease are translucent allowing light to pass through them; dielectric grease distorts the light passing through it. Silicon grease is also used as a polish for kitchen equipment and in the manufacture of food packaging products.
Electrical
The most common use of dielectric grease is in electrical applications as it does not allow foreign material to stick to conductors or allow an electrical charge to pass between contact points. Silicon grease is used in plumbing applications as it provides a waterproof seal.
Applications
Dielectric grease is often used in electrical applications, such as sealing cables and terminals from moisture. Silicone grease is used for a variety of applications including in the automotive industry and rubber parts manufacturing.
How to Replace 2000 Grand Vitara Headlights
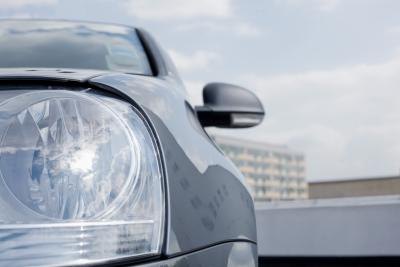
Replacing the headlights on the Suzuki Grand Vitara may be required if the lights have damage or if they are extremely discolored or cloudy. Replacement headlights are available from the Suzuki dealer network and through some specialty parts stores. Used headlights can often be found in salvage yards at a much lower price, but check them over to make sure they are not damaged or discolored as well.
Instructions
- 1
Open the hood of your Grand Vitara, then locate the screws in the perimeter of the grill from the front. Remove them with a Phillips screwdriver and lift the grill off the car.
2Locate the electrical connector on the back of the headlight assembly and disconnect it by pulling it straight away from the back of the headlight assembly. You will need to depress the locking tab on the connector before you can remove it.
3Locate the screw in the radiator support above the headlight assembly. Remove it with a Phillips screwdriver. Move to the front of the light and remove the two screws at the bottom of the headlight assembly with your Phillips screwdriver, then pull the headlight assembly straight out. Disconnect any wires that are still attached.
4Position the new headlight in the front of your Suzuki and install the three retaining screws. Tighten them with a Phillps screwdriver. Connect the electrical connector to the rear of the headlight assembly, pushing it in until the locking tab engages. Repeat the process on the opposite side of the truck.
5Position the grill in place on the front of the vehicle and install the retaining screws. Tighten the screws with a Phillips screwdriver. Close the hood.
What Causes Low Oil Pressure in a 1989 Camaro TBI
Low oil pressure can be extremely damaging to an engine. It is also a good prognosticator of a more serious problem. This is something that you do not want to allow to continue because it will cause severe damage to your engine or even destroy it. Being able to diagnose these issues is a skill that the average car owner can acquire.
Oil Viscosity
Using an oil with a viscosity that is too heavy will cause the pressure to run low. One way to fix this is to try a thinner oil. Make sure to read the owners manual and change the oil to a viscosity that is appropriate for your area and climate.
Clogged Oil Filter
Check the oil filter to make sure that it is not clogged with debris. Sometimes a large clump or grit will build up and cause the filter to clog. An oil change can fix the problem.
Oil Pump is Failing
Failure of the oil pump is another issue. If the oil pump is beginning to go out it will cause the oil pressure to drop. These need to be professionally checked.
Bad Oil Gauge
Failure of the oil gauge is also a possibility. Before taking the oil pan off or getting a major repair you should have the cars oil pressure checked by a local auto store. They will do this for free, and this will back up the result you are getting from your oil pressure gauge. A professional needs to repair this issue.
Faulty Gaskets
Examine the gaskets around the engine head and around the oil pan underneath the car. The best way to do this is to wipe the edges clean with a cloth and then drive or run the car for a few minutes. Make sure that you do get the oil warmed up, since this will allow it to leak and show you where the issue is. If you see large amounts of oil leaking, this can force the engine oil pressure to drop.
What Is a Hub Bearing Assembly

The hub bearing assembly is part of the mechanism of a car wheel. It is the assembly of hubs and bearings that facilitate the rotation of the wheel on the road surface.
Assembly
The hub bearing assembly consists of a wheel hub on which the bearings are mounted. The hub is attached to the axle and the bearings keep the wheel spinning smoothly. Hub bearing assemblies differ between front and back wheel sets.
Wear and Maintenance
A new wheel hub assembly should last up to 150,000 miles, after which it will probably need to be serviced and, eventually, replaced. If possible, replacement parts for specific makes and years should be found.
Problems
Signs that wheel bearings are faulty include wobbling of wheels, or a low growl or hum indicating too much friction. On detecting these warning signs, it is critical that you take your car to a mechanic to avoid further damage.
How to Recycle a Cat Converter
The "cat converter," another name for a catalytic converter, is a part of a vehicle designed to reduce emissions. Car makers have been required to install the devices, containing valuable palladium and platinum, in new cars since 1975, though in recent years car makers have been finding ways to make them without valuable metals. Still, because of the metals inside many converters, scrap metal recyclers will accept them for recycling.
Instructions
- 1
Search to find the best price for your cat converter. In 2010, platinum is worth about $1,700 an ounce. Youre not likely to get even close to that for the amount of platinum inside your cat converter, but its good to know how much platinum is worth. Look for a model number on your cat converter and search classified ads to find what that type of cat converter is selling for. Use this research as a guide when you go to recycle your converter.
2Find a scrap metal recycler near you. Many cities have at least a few scrap metal recyclers that you can find under "scrap metal" in business listings. Also check with the local garbage hauler to find out which places they recommend, or search the database of Earth911 under "scrap metal." Once youve found a place to accept your cat converter, note their hours and location.
3Take your cat converter to the scrap metal recycling center of your choice. Bring your identification, as many states have laws that track metal recycling to cut down on theft.
Saturday, November 23, 2013
How to Repair the Oxygen Sensor in a Ford Explorer
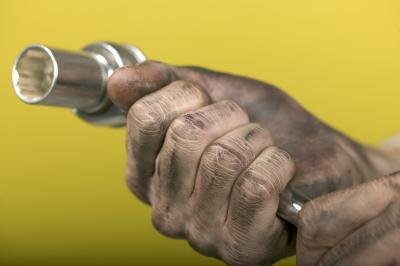
Oxygen sensors monitor the oxygen saturation in your Ford Explorers exhaust. The fuel to air ratio is regulated based on the readings from the oxygen sensors. A failing oxygen sensor can cause decreased fuel economy. Improve your fuel consumption as well as your Explorers emissions by replacing faulty oxygen sensors. You can purchase a new oxygen sensor at an auto parts store or Ford dealership.
Instructions
- 1
Disconnect the battery cable from the negative battery terminal. Set the cable in a secure area away from the terminal.
2Lift the truck with a jack and position a set of jack stands securely beneath it to support the vehicle while you work under it. Remove the jack when your Explorer is secure.
3Locate the O2 sensors along the exhaust. Depending on the engine your Explorer is equipped with, there are anywhere from one to four O2 sensors along the exhaust pipes and the manifold. Change your O2 sensors one at a time to make the process easier.
4Disconnect the electrical connection from the top of the sensor. The electrical connection plugs into the wiring pigtail on the top of the sensor.
5Unscrew the sensor from the manifold or exhaust pipe using an oxygen sensor socket and ratchet. Discard the old sensor.
6Coat the threads of the new sensor carefully with anti-seize compound if your new sensor is not pre-treated with it. Many sensors are pre-treated with anti-seize.
7Install the sensor using an oxygen sensor socket and ratchet to tighten it securely. Attach the electrical connector to the pigtail.
8Raise your Explorer with the jack and remove the jack stands. Lower the truck to the ground.
Bleeding the Clutch on 2003 F 150
Ford equipped the 2003 F-150 trucks that have the optional standard transmission package with a hydraulic clutch system. The clutch system consists of a master cylinder, slave cylinder and a hydraulic clutch line. Depressing the clutch pedal actuates the clutch master cylinder, which pressurizes the hydraulic line and slave cylinder, similar to how a hydraulic brake system works. Air bubbles suspended in the hydraulic fluid will lead to a spongy feel at the clutch pedal and could cause clutch drag and gear grind as the transmission is put into gear. Bleed air from the clutch with the engine cold.
Instructions
- 1
Place the vehicle in neutral and set the parking brake.
2Open the hood and locate the clutch master cylinder on the right side of the engine compartment against the firewall. Wipe dirt or debris from the clutch master cylinder reservoir cap, using a clean shop rag
3Remove the reservoir cap and diaphragm. Fill the clutch master cylinder reservoir up to the Full mark with brake fluid.
4Depress and release the clutch pedal through the full range of travel several times.
5Locate the bleeder screw on the drivers side of the transmission, just above where the clutch hydraulic line enters the transmission. Remove the rubber bleeder screw cover.
6Attach a 1/4-inch inside diameter clear vinyl hose to the bleeder screw. Pour a small amount of new brake fluid into a clear container. Submerge the free end of the hose in the brake fluid to prevent drawing air back into the system.
7Have a helper fully depress and release the clutch pedal five times, then hold the clutch pedal down.
8Loosen the bleeder screw, using a wrench, and observe the fluid escaping through the hose. Tighten the bleeder screw once fluid flow has stopped.
9Repeat steps 7 and 8 as necessary until no air is visible in the escaping fluid stream. Occasionally check and top off the fluid level in the reservoir to prevent introducing air into the system. Do not allow the reservoir to run dry.
10Tighten the bleeder screw securely, using a wrench. Remove the clear vinyl hose. Install the rubber bleeder screw cover.
11Have your helper slowly pump the clutch pedal through the full range of travel several times and check the bleeder screw for leaks.
12Depress the clutch pedal halfway and release it twice, then depress and release the clutch pedal through the full range of travel three times.
13Check and top off the fluid level in the reservoir with brake fluid. Install the reservoir diaphragm and cap.
14Start the vehicle and check for proper operation of the clutch before operating the F-150 in traffic.
How to Remove the Back Seat From an Infiniti I30
There may come a time when you will need more room in your Infiniti I30. It could be for extra storage in the trunk, or to lay something flat thats too long to fit in the back seat or the trunk. Whatever the reason, removing the back seat of an Infiniti I30 is a fairly easy task requiring no tools. You can create extra room in the back seat of your Infiniti in no time.
Instructions
- 1
Open the trunk and both rear doors of the Infiniti. Hold the seat bottom away from the back of the seat and lift directly up. It should unlatch itself fairly easily. Repeat for the other seat bottom.
2Undo the bolts and hooks that are holding the seat back in place at the bottom of the seat back. If you do not find the bolts and hooks, you may have to access them through the trunk. Repeat on the other seat back.
3Lift the seat back up and forward to remove it. Lift the seat out of the Infiniti. Repeat for the other seat back.
How to Change a 2000 Chevrolet S10 2 2L Valve Cover Gasket

Changing the valve cover gasket on a 2000 Chevy S10 2.2L requires some mechanical skill, as there are a few components that need to be removed in order to reach that gasket. However, with the right tools and some patience, the do-it-yourself repair is well worth the effort, because it will save a lot of money. The job is somewhat labor-intensive, which makes it costly at repair shops. The new gasket is inexpensive and easy-to-find, most auto parts stores should have one in stock for a model as common as the 2000 Chevy S10 2.2L
Instructions
- 1
Let the engine cool completely.
2Remove black plastic air duct on the left side of the engine by separating it from the intake hose. In most S10 models built between 1998 and 2003, including the 2.2L version, you need to loosen a few clamps with a screwdriver to pull the air duct off the hose. In some models, the air duct is just stuck on the hose and comes off when you pull hard enough.
3Locate the throttle to the left off the valve cover. Pull the cable to unsnap it from the bracket.
4Pull the brake booster hose from its point on top of the valve cover.
5Remove the valve cover bolts by using the ratchet, the extension and the socket set. There should be eight No. 10 bolts.
6Take off the valve and scrape out the old gasket, which most likely will be hard from wear. Make sure no residue of the old gasket is in the mold. Clean the mold with a rag and wipe off gunk and dirt that might be stuck.
7Place the new gasket in the mold, making sure it fits tightly. Reassemble the other components in the same order you disassembled them.
How to Flush Automatic Transmission Fluid
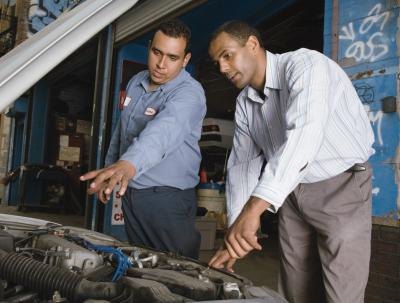
Prior to the invention of the automatic transmission flush machine, a transmission service was nothing more than removing the pan, replacing the filter, reinstalling the pan and adding five or six quarts of fluid back into the transmission. While this was better than ignoring your transmission altogether, it really only allowed for the replacement of 30 percent of the transmission fluid. Fortunately, transmission flush machines do exist, and theyre in the hands of trained transmission technicians.
Instructions
- 1
Fill a 5-gallon bucket with the recommended amount of transmission fluid for your vehicle. Make sure to use the fluid specified by your vehicles manufacturer for your type of transmission.
2Insert the suction hose from the automatic transmission flush machine into the bucket and turn the machine on to the "Fill" setting. Fill the machine and shut it off when done.
3Disconnect the transmission cooler lines from the transmission with a box wrench. Attach the suction and discharge hoses from the flush machine to the cooler lines with a socket set.
4Start the vehicle and turn the flush machine to the "Flush" setting. Wait for the new transmission fluid to empty into the transmission. Shut the machine and the vehicle off.
5Remove the suction and discharge hoses from the cooler lines with the socket set. Reconnect the cooler lines to the transmission cooler with the box wrench.
Friday, November 22, 2013
How to Check Engine Codes for the Mazda B2200

The 1992 Mazda B2200 came equipped with a "Power Control Module" that helps control and diagnoses the functions of the engine and other vital parts of the vehicle. Each vehicle, regardless of make and model, come equipped with a system that assigns a code to each issue and stores it in the "tester" box. With the right tools and knowing how to interpret the codes, check engine codes of your Mazda B2200 without having to take it to a repair shop.
Instructions
- 1
Warm up the engine for one to two minutes before shutting it off. This will cause any problems with the Mazda to show up during the diagnostic reading.
2Pop open the hood and locate the "Tester" box, which is a 2-by-2-inch box on the driver side of the engine.
3Find the connections labeled "STI and "SIG RTN." Securely connect a 3-inch metal wire, with a plastic protective covering, from the SIG RTN to the STI slot. Wiggle the wire to ensure the wire will not become loose during the test.
4Turn the ignition on, but do not start the engine. Watch for the blinking "Check Engine" light. With a paper and writing utensil, write down the pattern of short and long intervals between flashes of light. The intervals corresponds with codes in a repair manual. Check your local library, repair shop or online database for a list of engine codes.
1996 Chevy Silverado Coil Removal
Removal of the ignition coil from the engine in your 1996 Chevy Silverado may be necessary to access parts of the engine behind or below the coil or if the coil is failing and replacement becomes necessary. The ignition coil supplies high-voltage electricity to the spark plugs, by way of the distributor, to produce the spark required to fire the fuel in the engine cylinders. If the coil begins to fail, lower voltage to the spark plugs will result in weak spark and the engine will run poorly if at all.
Instructions
- 1
Locate the negative battery cable end on the battery terminal and loosen the clamp bolts with a wrench. Remove the cable from the terminal and set it aside, isolating it from the battery terminals.
2Locate the ignition coil on the top of the engine, near the front on the drivers side. Pull the high-tension cable off the top of the coil and lay it off to one side. Locate the wiring harness connection on the side of the coil.
3Depress the locking tab on the side of the wiring harness connector and remove the connector from the coil. Locate the two mounting bolts on the mounting bracket and remove them with a socket and ratchet.
4Lift the coil and bracket off the engine. If you are installing a new coil, you will need to reuse the mounting bracket so do not discard it once you remove it from the engine.
How to Identify Subaru Parts

If you need to have body work done on your Subaru, select a body shop that uses genuine Subaru parts. When you take your vehicle to a Subaru dealer, you can be sure they use genuine parts. If you take it to another body shop, you can verify that the replacement parts are Subaru-built by a simple examination. If you order parts for a do-it-yourself repair project, there is a way you can confirm that the parts are genuine Subaru parts. Many parts do not have the Subaru name or symbol imprinted on them.
Instructions
Inspecting Body Work
- 1
If you have a fender, door or hood replaced on your vehicle. You can visually inspect it to verify it is a genuine Subaru part.
2Search the inside edges of the replacement part for the name Subaru. Use a flashlight to look for the marking. Hold the flashlight at an angle to the medal edges to spot the name.
3The word "Subaru" will be stamped into the formed sheet metal margin of the body parts. The name is imbedded so it is the same color as the vehicles paint. The size is approximately 3/16 inch tall by 1 3/8 inches long. It may be difficult to see.
Identifying Replacement Parts
- 4
A massive number of parts that go into a Subaru will also go into a Mazda, Chevrolet or Ford. The manufacturers who make mechanical parts for Subaru also make parts for other auto makers because some items such as bearings or clutch plates are uniformly sized and formed. Knowing this, there are some replacement parts that you cannot identify as Subaru parts unless they are still in their packaging. Genuine Subaru parts meet Subaru specifications and come in packaging labeled "Genuine Subaru Parts."
5Select a repair shop that pledges to use genuine Subaru replacement parts or take your car to a Subaru dealer.
6Before work begins on your vehicle, ask the repair shop to retain all boxes and bubble packs from the parts they will install on your car. This way you can see that the parts came in Subaru packaging.
7If you plan to work on the car yourself, order parts from a Subaru dealer or online Subaru part supplier.
8Some Subaru parts feature the official Subaru symbol of a six-star constellation. If you have a steering wheel or wheel hubs replaced, you can tell if they are genuine parts because these items feature the star constellation insignia.
How to Remove Headrests in a 1997 Lincoln Town Car
The Lincoln Town Car first reached the market in 1981. In 2003, Ford Motor Company began offering a bulletproof model of the Town Car for security purposes. The Town Car is also one of several models used by limousine companies as a transportation vehicle. The front headrests of the 1997 Lincoln Town Car are adjustable and removable. Remove the headrests from your Town Car to clean, detail or replace them.
Instructions
- 1
Push in on the retaining tab located on the outer edge of the headrest, near the top of the seat.
2Hold the retaining tab in while lifting up on the headrest. Pull the headrest all the way up until you remove it completely from the mounting holes.
3Line up the metal posts of the headrest with the mounting holes to replace it. Push in the retaining tab and insert the headrest. Push the headrest all the way down against the seat, then release the tab.
Thursday, November 21, 2013
Power Steering Components for a 350 Monte Carlo Engine
The power steering components on your Chevrolet Monte Carlos 350-cubic-inch V8 engine actually have very little to do with the engine itself. The power steering system uses power generated by the running engine to provide you with easy handling and steering. Without power steering, your car would be extremely difficult to steer or control.
Power Steering Pump
The power steering pump is a pump that supplies the hydraulic power for the power steering system. Without the power steering pump, the Monte Carlos power steering system will not work. The power steering pump takes the power generated by the pulleys and belts from the engine and converts it to compensate for the steering and assist you in turning and handling the vehicle. There is a reservoir on the power steering pump that holds the hydraulic power steering fluid.
Hoses
The power steering hoses allow the power steering fluid to travel. The hoses connect the power steering pump into the steering mechanisms themselves, normally the gearbox or power steering box, depending on the model of Monte Carlo you own. The power steering systems have been updated and improved since Chevrolet originally introduced the Monte Carlo in the 1970s.
Belt and Pulleys
The power to run the Monte Carlos power steering pump is generated by a belt and pulley system that turns power generated by the engine into the force that generates the hydraulic power for the steering system.
How to Properly Measure a Driveshaft

The drive shaft is responsible for transferring torque from the engine to the axles. It is subject to a great deal of wear and occasionally may need to be replaced. You may also want to change the drive shaft if you are modifying your car to increase speed and power. In order to get the correct replacement part, it is imperative to have the correct measurements. Fortunately, this is not difficult to do, and can be accomplished with just a tape measure or ruler.
Instructions
- 1
Determine if you have a single piece or multi-piece drive shaft and which type of connection you have. You can determine this by looking at the mounting. It will be either a universal joint (U joint) and yoke, a flange mount, or a one-piece drive shaft that connects to the rear differential with a cap mount.
2To measure a U joint drive shaft, measure from the center of one U joint to the center of the other. You should also measure the U joint cap diameter that fits into the pinion yoke.
3To measure a drive shaft connected by flanges, place one end of your measuring tape at the inside face of the flange and measure across to the inside face of the opposite flange. In addition to the overall length, you should also measure how far the shaft sticks out of the flange.
4To measure a one-piece drive shaft, place one end of your tape at the end of the transmission shaft and measure to top of the cap at the opposite end.
5To measure a drive shaft with a center support bearing, measure the overall length from the end of the transmission case to the center of the center support. Then measure from the center of the center support to the flat surface on the pinion yoke. You will also need to measure the width of the pinion yoke, the the U joint cap diameter, how far the shaft sticks out past the end of the case, and note if the hole in the end is threaded or not.
6To measure a drive shaft that has two different types of connections; for example a U joint on one side, and a flange on the other, simply combine the instruction for each type of mount. In the example, you would measure from the center of the U joint to the inside face of the flange on the opposite side.
7Some companies will also require you to measure the space between the locating tabs, or two flat surfaces on the yoke. This should be done with a small six-inch ruler or caliper. Depending on the type of drive shaft, you may also be asked for the number of splines in the yoke, the diameter of the splined hole, and the height of the yoke.
Bumper Requirements for Vehicles in Texas

Although Texas vehicle inspection requirements dont directly address bumpers and bumper specifications, several requirements are indirectly tied into it. Additionally, some vehicles in Texas are also required to meet bumper standards issued by the National Highway Transportation Safety Administration for passenger cars, which dictate durability and placement of bumpers on passenger cars.
NHTSA Standards
All passenger cars sold in the United States must meet NHTSA requirements for front and rear bumpers. These standards require bumpers to be able to withstand a collision of 2.5 mph on the front and rear sections, and 1.5 mph on the corners; this impact rating is equivalent to hitting a parked car of the same mass at 5 mph. Bumpers must guard a section of the front and rear of the car between 16 and 20 inches off the ground. These standards apply only to passenger cars, and light trucks and SUVs bumpers are not regulated by the NHTSA.
Lights and Bumpers
To pass vehicle inspection as regulated by the Texas Department of Public Safety, the lights mounted inside or above bumpers must be visible. Texas requires all cars to have at least two red or amber stop lamps, which may be mounted inside the rear bumper, and must not be obscured by it. These lights must be visible for at least 300 feet. Additionally, rear bumpers should feature red tail lamps visible for 1,000 feet behind the vehicle. Head lamps need not be mounted on or inside front bumpers, but if they are, they must be between 54 and 24 inches from the ground in front of the vehicle.
Reflectors on Bumpers
Texas motor vehicle inspectors require that all vehicles must carry at least two red reflectors, visible for 350 feet when illuminated by head lamps. These may be mounted on or in the rear bumper or independently affixed to the vehicle.
License Plate Lamp
The Texas Department of Public Safety declares that if a license plate is mounted on the rear bumper, it must be equipped with a license plate lamp that illuminates the plate when the vehicles operating lights are on. This light must be firmly and permanently affixed to the bumper, and must not shine a glaring light at cars behind the vehicle.
Different Sizes of Headlights

Automobile headlights have gotten progressively smaller, brighter, and more focused on the road. In early cars headlights were mounted in big, hulking, self-contained units to the front of the grille. As vehicles got more sophisticated headlights were integrated into the body, though they remained self-contained units. In modern vehicles the headlamp is usually a shell which houses replaceable light bulbs.
The First Headlamps

The earliest cars used gas or oil and acetylene-powered headlights mounted to the hood, which were about as big as a basketball and externally powered. Drivers had to get out of the car to turn them on. They had to be frequently repaired or replaced, especially if operated in rainy weather. Electric headlamps finally came into use in 1912. They were still bulky and externally powered, but held up better in inclement weather.
Electric Headlights

As electric headlamps became powered by the cars electrical system, they got smaller and more frequently integrated into the body of the car. They were about the size of a grapefruit or smaller. Mounted at the far, outside corners of the hood, the brighter, smaller electric lights could be focused lower to provide a wide sweep of the road ahead while creating less glare in the eyes of on-coming drivers.
Halogen Headlights
Halogen headlights came of age in the mid-60s. Using a tungsten filament they produce a much brighter light than the older electric lights and last much longer. Because of the improved brightness, they allowed an explosion in headlight shapes and sizes. In the 70s and 80s rectangular-shaped headlights about the size of a checkbook were popular. They were made possible by the superior brightness of halogen lights. They remained self-contained units that plugged into the headlight frame on the car.
High Intensity Discharge

Halogen lamps remain the most common form of car headlight. In modern cars, though, the lamp casing is part of the car. Only the bulbs are replaced. Most manufacturers also offer high-intensity discharge, or HID bulbs. HID lamps use no filament at all. They use an inert gas, usually xenon, that glows brilliantly when a high-voltage arc is present. These lamps can produce twice the brightness of halogen, use less energy, and can appear in different colors. The bluish-white headlights on some high-end cars is produced through HID lamps. Some manufacturers now make bluish halogen bulbs to imitate HIDs, but the halogens do not produce as bright or clear a light.
How to Remove a Battery Tray on a 1997 Dodge Caravan
Removing the battery tray from your 1997 Dodge Caravan may be necessary if the tray has cracks or damage that may compromise the integrity of the tray. The tray is made of plastic, and has to not only support the battery but also retain it to the engine compartment of the van. The battery hold down is an integral part of the tray and if it fails, the battery may come out of the tray, causing damage to the battery, the cables or part of the engine.
Instructions
- 1
Locate the negative battery cable on the top of the battery. Loosen the clamp bolt with a wrench, then remove the cable from the battery.
2Loosen the clamp bolt on the positive battery cable with a wrench and remove it as well. Isolate the battery cables so that they are out of the way and cannot fall back against the battery.
3Locate the retaining clamp and bolt near the bottom of the battery on the inboard side of the tray. Remove the nut from the retaining clamp with a socket, extension bar and ratchet. Remove the retaining clamp and lift the battery out of the van.
4Locate the three retaining bolts that hold the battery tray into the van. There are two in the base of the tray and a third just to the front of the retaining clamp location. Remove the two in the tray with a socket and ratchet then set them aside.
5Remove the third retaining bolt with a wrench, set the bolt aside, and lift the tray out of the engine compartment.