Thursday, October 31, 2013
The Location of the Chassis Number Plate on a 1983 Mercedes
The chassis number of a 1983 Mercedes is six digits and can be found on a metal data plate on the car or on a data card in the owners documents. If you need to order new parts for your Mercedes, it is necessary to provide the chassis number. The first three digits of the chassis number represent the body style. The last three numbers represent the specific car, such as a coupe or a convertible.
Instructions
- 1
Pull the hood release, then open the hood.
2Look for the metal plate stamped into the body frame near the radiator. The six-digit chassis number will be printed on the metal plate. For a 1983 Mercedes, the chassis number will start with "123," "126" or "107."
3Consult your owners documents given to you when you purchased the car. Included with the documents should be a data card with all the important identification numbers for your vehicle. The chassis number will be printed there.
My CRF250X Wont Start After a Wash

The CRF250X is a small engine manufactured by Honda for use with dirt bikes. If you are having problems with your CRF250X after washing it, there are several things you can do before you take it to a service shop. Many engines should not washed with a garden hoses because the water can get into the starter or the alternator. You can test these items in just a couple of seconds.
Instructions
- 1
Turn the key in the ignition of the CRF250X and listen for a "clicking" noise. If you hear this clicking noise, your alternator has been damaged by the water you used to wash your bike. Take the dirt bike to a service station to get the alternator checked. Service shops have specific tools to test the alternator.
2Take the bike to a service station where they can check your starter if you dont hear a clicking noise, but the bike still will not start. The starter can get damaged by water also. Service stations have specific tools to test your starter.
3Look at the gas gauge while the electrical panel is on. If the gas gauge is low, fill the tank and try to start the bike. If the bikes gauges dont light up, you have a problem with your battery.
4Locate the battery under the seat of the bike. You should see two wires going to your battery, a red one and a black one. Make sure that these wires are securely connected to the batterys terminals. Use a pair of insulated pliers to tighten the connections to the battery. Try to restart the bike.
5Connect a voltmeter to your bikes battery if it still wont start. Connect the red lead to the positive (+) terminal on the battery. Connect the black lead to the negative (-) terminal on the battery.
6Look at the reading on the voltmeter. If your reading does not provide a result at or about 12 volts, the charge is too low. Connect jumper cables to your bikes battery terminals and then connect the other end of the jumper wires to the "+" and "-" terminals on a different battery.
7Start the other bike and then try to start your CRF250X. Allow the bike to run for 15 minutes and then cut the bike off. Try to restart the bike. Replace the battery if the bike does not restart.
How to Replace the Windshield on the 1993 Jeep Cherokee

If the windshield on your 94 Jeep Cherokee is cracked or chipped, you can replace it yourself right from home. You do need a helper to complete the job. You can find a very inexpensive replacement windshield by visiting your local junkyard. You dont need any specialized automotive or glass experience.
Instructions
- 1
Place a tarp on the entire dashboard and tape it in place.
2Use a screwdriver to remove the wiper arms.
3Pry the gasket out from around the windshield using a screwdriver. Cut the adhesive attaching the windshield to the frame using a box knife.
4Get a helper to help you remove the old windshield.
5Examine the used replacement windshield to make sure it is free of any cracks and chips. Thoroughly clean the edges of the windshield with a rag and window cleaner.
6Sand the replacement windshields edges.
7Spread silicon windshield adhesive on the edges of the Jeep Cherokee where the windshield will go. Put the replacement windshield in place with the help of your assistant. Fit the new gasket around it by hand.
8Screw the wipers back in place. Wipe any extra adhesive from the windshield. Allow one day to dry. Dont drive the Jeep while it is drying.
What Causes Water to Get Into the Exhaust System
The Combustion Engine
A natural byproduct of a combustion engine is water. It is expelled with the exhaust gases. Fuel is mixed with air and then forced into the cylinders. Once the mix is inside the cylinder, a small explosion occurs before the exhaust camshaft opens and the exhaust is released into the manifold. Because of the intense heat of the combustion engine, the water is vaporized.
The Catalytic Converter
All vehicles since 1980 have catalytic converters. The catalysts convert the unspent fuel into spent fuel before being expelled past the component downstream. Older converters were called two-way converters because they turned carbon monoxide into carbon dioxide and hydrocarbons into water vapor. Not only is water vapor present in the exhaust system coming directly from the engine, but the converter also produces more by chemically altering the hydrocarbons. Nowadays, vehicles employ a three-way catalyst which also reduces harmful nitrogen oxides.
Preventative Maintenance
Depending on your geographical region and driving habits, its not unlikely for the exhaust system to rust and corrode from the inside out. If you live in a place that has severe winter weather and uses sand and salt on the winter roadways, your exhaust may deteriorate on the outside as well as the inside.
Short commutes are a major cause of internal water corrosion of the exhaust system. The water vapors do not have the chance to expel from the system and turn back into water once the vehicle is shut off. When there is no back pressure forcing the water vapors out of the system, the vapors coat the interior of the exhaust components and then form puddles on the bottom. Many mufflers employ a manufactured seep hole in order to allow the water to drain from the muffler. But the pipes and converter do not drain.
If you take short trips, try to run your vehicle for at least 15 minutes to allow the water vapors to purge from the exhaust system.
Car owners in regions with severe weather should wash the undercarriage of their vehicles once a week during these seasons to clean off the sand and salt. Even stainless steel exhaust systems will be compromised in these areas, although they will last significantly longer than aluminized steel systems.
How to Fix the Fuel Pump in a 2001 Hyundai
Hyundai is a car manufacturer in South Korea that primarily makes compacts and subcompacts. The 2001 models use multi-port fuel injection, which requires the fuel pump to deliver fuel to the injectors at high pressure. The procedure for repairing the fuel pump in a Hyundai is generally the same for all models from 1999 to 2005. The fuel pump is attached to the fuel tank, requiring you to remove the fuel tank when replacing the fuel pump.
Instructions
- 1
Remove the rear seat cushion to expose the access panel in the floor of the vehicle. Open the access panel and disconnect the electrical connector for the fuel pump. Start the engine and allow it to stall. Turn the ignition off.
2Open the filler cap for the fuel tank and place a hose into the filler tube. Siphon as much fuel as possible from the fuel tank into a container for gasoline.
3Disconnect the cable to the negative battery terminal with a socket wrench to prevent in the accidental discharge of fuel. Raise and support the vehicle on jack stands. Disconnect the fuel supply line, fuel return line and fuel vapor line from the fuel tank. Detach the fuel fill hose and fuel vent hose from the fuel tank.
4Remove the electrical connector from the fuel level sender. Support the fuel tank with a jack and remove the fuel tank straps with a socket wrench. Disconnect the fuel tank from the vehicle and lower it to the ground. Move the fuel tank to a work area.
5Disconnect the mounting bolts on the fuel pump with a socket wrench. Disconnect the fuel pump from the fuel tank.
6Install the new fuel pump to be fuel tank, and tighten the mounting bolts for the fuel pump to between 12 and 24 inch-pounds with a torque wrench. Complete the installation of the new fuel pump by performing steps one through five in reverse order. Filled the fuel tank with fuel, and check the fuel system for leaks.
Wednesday, October 30, 2013
How to Replace a Knock Sensor in a Nissan Maxima
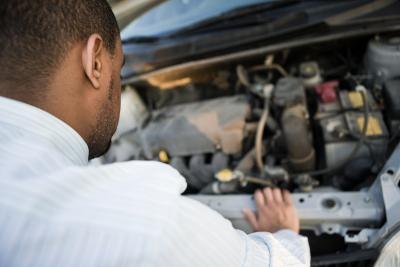
Replacing the knock sensor on the Nissan Maxima is simple, but the sensor can be expensive, so be sure to have the car properly diagnosed before assuming the sensor is bad. The knock sensor detects engine knock or ping in the engine, then transmits data to the engine-management computer, enabling the computer to retard or make other critical adjustments to the timing, spark and fuel delivery.
Instructions
- 1
Open the hood of your Maxima and locate the negative battery cable at the battery terminal. Using a wrench, remove the retaining bolt and separate the cable from the battery, isolating the cable while you work.
2Locate the knock sensor on the top edge of the engine block on the right side of the engine. It is about halfway back and is a circular part with a bolt running through the center and an electrical connector on the outer edge. Disconnect the wiring harness connector from the knock sensor by lifting the locking tab slightly and then pulling the connector off the sensor.
3Remove the bolt from the center of the knock sensor with a socket and ratchet, them remove the sensor from the engine block. Position the new sensor on the engine block and insert the retaining bolt through the center, threading it into the engine block.
4Tighten the bolt with a socket and ratchet, then install the electrical connector on the sensor. Make sure you push the connector in enough for the locking tab to engage.
5Connect the negative battery cable on the negative battery terminal. Install the retaining bolt and tighten it with a wrench. Close the hood of your Maxima.
Engines That Will Bolt Up to a Toyota Five Speed Transmission

When Toyota vehicles with five-speed transmissions are headed for the junkyard, owners can save money by replacing their cars engine. Engine manufacturers call the process "vehicle repowering" and owners add years to the life of the vehicle when they opt for repowering over individual engine repairs. Some automotive shops specialize in acquiring replacement Toyota engines from domestic and international locations. The kits come with all the equipment needed to bolt the engine onto the vehicle.
1990 to 1993 Celica
The Celica GT-fourth generation 5/all-trac 3S-grand turismo turbo engine is the all-wheel drive, five-speed transmission engine for Celicas manufactured between 1990 and 1993. The four-cylinder, 16-valve engine produced by Toyota weighs 600 lbs. with 225 horsepower at 6000 rpm. The engine produces 200 ft.-lbs. of torque at 3200 rpm. Redline levels occur at 8000 rpm. JDM Engine Depot supplies the engine for a suggested retail price of $1,099 (as of 2011). Engine heads, a power steering pump and all-wheel drive manual transmission are included with the engine.
1986 to 1989 Celica
Five-speed-transmission Celica vehicles manufactured between 1986 and 1989 are compatible with the Celica grand turismo-fourth generation 4/all-trac 3S-grand turismo turbo engine. The four-cylinder, all-wheel drive, 16-valve engine manufactured by Toyota weighs 600 lbs. The unit is capable of 190 horsepower at 6000 rpm and 190 ft.-lbs. of torque at 3200 rpm. Redline levels occur at 8000 rpm. The engine is available through JDM Engine Depot at a suggested retail price of $999 (as of 2011). Complete engine heads, flywheels, a wiring harness and an all-wheel-drive manual transmission are included with the engine.
1994 to 1999 MR2
The MR2 third-generation 3S-grand turismo turbo engine is compatible with the MR2 rear-wheel drive sports car manufactured by Toyota between 1994 and 1999. The four-cylinder, 16-valve engine is capable of 225 horsepower at 6000 rpm and 200 ft.-lbs. of torque at 3200 rpm. Redline levels occur at 8000 rpm. Total weight of the all-wheel drive, five-speed transmission engine is 600 lbs. JDM Engine Depot provides the engine at a suggested retail price of $1,999 (as of 2011). Engine heads, a non-limited slip differential transmission and fuel rails are included with the engine.
1991 to 1993 MR2
The MR2 3S-grand turismo turbo engine is compatible with second generation MR2 front-wheel drive sports cars manufactured by Toyota between 1991 and 1993. The four-cylinder, 16-valve engine is capable of 220 horsepower at 6000 rpm and 200 ft.-lbs. of torque at 3000 rpm. Redline levels occur at 8000 rpm. Total weight of the five-speed transmission engine is 600 lbs. JDM Engine Depot supplies the engine at a suggested retail price of $1,749 (as of 2011). The engine kit includes complete heads, sensors and distributor.
How to Clear Codes on a Chevy Silverado

You can clear the codes on your Chevy Silverado using an OBD scan tool, a hand-held computerized device available at most auto parts retailer. The tool is used to read the codes, and clear them after servicing or repairs. OBD stands for "On-Board Diagnostics." This is the computer that monitors all functions of the vehicle. When there is a malfunction within the Silverado, sensors positioned throughout the vehicle will send a trouble code to the OBD computer.
Instructions
- 1
Locate the data link connector (DLC) port that is the same size and shape as the OBD scan tools connective end. This port is located on the underside of the drivers side dash next to the steering column.
2Plug the handheld scan tool into this port. Put the key into the ignition and turn it to the "II" position, but dont start the engine. This will turn on most scan tools. If not, locate the on/off switch and turn it on.
3Wait for the scan tool to retrieve the codes, then press "Erase Codes."
4Unplug the scan tool after it has finished erasing the codes. Start the engine and check to make sure all lights have turned off on the instrument cluster.
How to Enable the Radio in My Honda Civic

If you disconnect the battery in your Honda Civic for any period of time -- even if you reconnect it properly -- you might be dismayed when you get in the car later and discover that the stock radio no longer turns on. Instead, the radios display will prompt you to enter a code. Without the code, the radio will not work. This is an anti-theft measure that makes that stock radio from your Honda Civic useless to anyone who steals it out of your car--unless they have access to your particular Civics specific security code.
Instructions
- 1
Locate your vehicle identification number (VIN); the VIN is a 17-character alphanumeric string used to identify your particular car -- no two VINs are alike. Standing outside the Civic, look through the extreme lower portion of the windshield, on the drivers side of the car, for a small, rectangular metal plate fastened to the dash. Record this number on paper. Check your work to ensure you got the VIN written down correctly.
2Call your local Honda dealer or the support number located in your Civics manual. Explain that you need the code for your radio and provide them the VIN. Write the code down and store it in a safe place. If you ever change your battery, which you or the next owner will, youll need it again.
3Turn the car ignition key to the "on" position. Enter the five-digit code by pressing the corresponding keys (preset buttons) on the radios face.
4Turn the ignition key to the "off" position then back to the "on" position to ensure that the radio functions.
How to Remove the Battery From a Sportster 1200 Low

Without a fully functional battery, no motorcycle is operational. As goes the battery, so goes a bikes performance. While removing the battery from most motorcycles requires you to simply access the battery compartment below the bikes seat and disconnect the terminal wires, Harley Sportster 1200s designed the battery compartment such that the negative terminal is directly connected to the bikes frame. Consequently, removing the battery from a Sportster 1200 Low is a slightly more complicated procedure than it is with most other motorcycles.
Instructions
- 1
Remove the black plastic cover for the battery compartment. The cover is located underneath the seat on the left side of the bike. Remove it by gently pulling on the top of the cover to unsnap its top clip. This should allow you to easily remove the entire cover and set it aside.
2Slide the plastic electronic battery harness to the right of the battery to access the negative terminal.
3Remove the bracket connecting the negative ("-") terminal to the frame of your Sportster with a socket wrench. The negative terminal grounds the battery. Removing it first will allow you to remove the wires connecting the positive ("+") terminal without shocking yourself.
4Pull the wires connected to the positive terminal off by hand.
5Cover the negative terminal with black electrical tape. This will protect you against accidentally touching the terminal to the frame, thereby grounding the battery and potentially shocking yourself.
6Slide the battery out of the compartment.
Tuesday, October 29, 2013
How to Remove a 12 Valve Cummins Injection Pump

The Cummins B series of diesel engines are best-suited for light and medium trucks. The 6BT is a six-cylinder engine with two valves per cylinder, for a total of 12 valves. The Cummins 6BT is typically turbocharged and appears in Dodge trucks from 1994 to 1998, such as the Dodge Ram 2500. This engine uses an injection pump to keep the fuel at high pressure. The removal of the injection pump from a 12-valve Cummins engine requires the No. 1 cylinder to be in the top dead center position.
Instructions
- 1
Remove the cable from the negative battery terminal with a socket wrench. Disconnect the throttle linkage from the engine and remove the fuel drain manifold. Detach the fuel lines and the electrical wiring from the injection pump. Disconnect the fuel air control tube.
2Disconnect the support bracket for the injection pump with a socket wrench. Remove the bracket for the oil filler tube from the front cover of the injection pump. Place a shop rag over the opening in the gear cover to keep debris out of the gear housing.
3Connect a turning tool to the opening in the flywheel housing and attach an extension to the turning tool. Push the top dead center pin on the flywheel housing as you turn the flywheel with the turning tool. Stop turning the flywheel when the pin drops into the gear timing hole. Remove the pin from the hole and detach the turning equipment from the flywheel housing.
4Remove the lock screw and washer from the injection pump with a socket wrench. Tighten the lock screw to 22 foot-pounds with a torque wrench to hold the crankshaft in place. Pull the drive gear for the injection pump from the crankshaft with a gear puller.
5Disconnect the three mounting nuts from the injection pump with a socket wrench and detach the injection pump from the engine. Remove the gasket for the injection pump and clean the mounting surface for the gasket with a shop rag.
Single Barrel Carburetor Types

A carburetor combines fuel and air for the internal combustion engine of a motor vehicle. This device can have a single barrel, two barrels or four barrels. A single-barrel carburetor is commonly used on small engines that do not need large amounts of fuel and air. More barrels are only needed when there is a high rate of air flow and fuel displacement.
Single-Barrel Downdraft Carburetor
The single-barrel downdraft carburetor is one of the most common types of single barrel carburetors. These carburetors are suitable for engines requiring low air velocity and containing more air passages. Single-barrel downdraft carburetors use gravity to push the mixture of air and fuel into the cylinder.
Natural or Side Draft Carburetor
Natural or side draft single-barrel carburetors are best suited for use in small spaces above the engine. Unlike the downdraft carburetor, these types of carburetor move the air horizontally into the devices manifolds, which supply the air and fuel mixture to the cylinder.
Updraft Carburetor
The third type of single-barrel carburetor is the updraft carburetor. This type has been replaced by the aforementioned carburetors but some older cars still use them. The updraft carburetor is placed below the engine. Gravity forces the fuel from the tank above into the carburetor below. However, the air and fuel mixture must still be pushed upward into the engine.
How to Clean a Grease Gun

Used to apply pressurized grease to mechanical components that require lubrication, grease guns are an essential tool in many workshops, particularly automotive garages. Though grease guns certainly clean up the process of applying grease compared to the old method of applying it by hand or with a grease swab, using a grease gun is still a messy process. Cleaning a grease gun ensures that it applies grease evenly and smoothly. Clean your grease gun with clean cloth towels and water mixed with a gentle anti-grease soap, such as dish detergent.
Instructions
- 1
Remove the old grease cartridge from your grease gun according to the specifications of your specific gun. Often this process requires you to unscrew the head of the grease gun, pull out the loading rod at the bottom of the handle and then pull the cartridge out with a pair of pliers.
2Wipe all the excess grease off of the external nozzle as well as the inside of the cartridge chamber with a clean cloth. It is important to clean off all the old grease, as well as any debris which may have become trapped by the grease, including grit, dirt, metal shards or fibers. Use a durable press-fiber cloth so as to avoid inadvertently leaving fibers on or in the grease gun.
3Wash the exterior and interior components of the grease gun with a mild grease cutting soap such as dish detergent. Scrub the gun components with soapy water and a fresh press-fiber cloth.
4Soak and rinse the exterior and interior of the gun thoroughly with fresh water. Ensure that all soap is rinsed thoroughly from the gun, or the integrity of any grease you apply with the gun will be compromised.
5Dry the guns exterior thoroughly and allow the interior to air dry for at least a day before attempting to reload a fresh grease cartridge.
How to Remove Difficult Exhaust Nuts
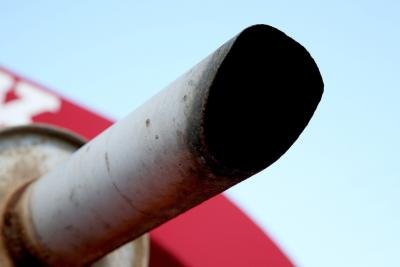
Exhaust nuts often seize due to corrosion forming on the exhaust studs that hold the exhaust clamp in place. The corrosion that forms is rust. The heat generated by the exhaust coupled from humidity and water causes the rust to form thick on the threaded section of the exhaust studs. To remove difficult exhaust nuts, you often have to use heat from a torch. If you cannot use a torch to release the nuts due to the proximity of the nuts to a fuel line, there is another option.
Instructions
- 1
Spray penetrating oil onto the difficult exhaust stud and allow the penetrating oil to soak into the exhaust nut for at least three-hours before you proceed to the next step.
2Select a socket from the socket set that fits onto the difficult exhaust nut.
3Place the socket onto the 1/2-inch drive ratchet and slide the nut onto the difficult exhaust nut.
4Set the 1/2-inch drive ratchet to loosen and turn the handle of the ratchet counter-clockwise to attempt to loosen the exhaust nut. If the nut does not loosen, proceed to step four.
5Insert the handle of the 1/2-inch drive ratchet into the 24-inch long piece of 5/8-inch I.D. pipe.
6Continue to push the pipe attached to the ratchet counter-clockwise to attempt to release the difficult exhaust nut.
7Reverse the direction and attempt to tighten the exhaust nut. If the nut does not move, slide the pipe slightly down the ratchet handle to give you more leverage and push as hard as you can. The seized nut will snap the threaded section of the exhaust stud.
8Repeat the process to snap other difficult exhaust nuts that will not release and turn off the threaded exhaust studs.
Monday, October 28, 2013
How to Replace a 1995 Honda Accord Bumper

Your Honda Accords bumpers are the first parts of defending the cars ends during a possible rear-end or head on collision. Should the unfortunate occur, you may find that replacing the bumper to your 1995 Accord is not such a difficult task. If you are able to find a matching replacement for the bumper, you may be able to perform this repair procedure from home. Luckily, there are no special tools required for the job.
Instructions
Removing and Installing the Front Bumper
- 1
Open the engine compartment.
2Remove the radiator grille by unscrewing the five screws at the top with a Phillips screwdriver. Push down on the retaining tabs, with a flathead screwdriver, located between the grill and each headlight. Remove the grille.
3Unscrew the plastic retaining screws with a Phillips screwdriver, and unbolt the bumper bolts using your socket wrench, from under the bumper.
4Unscrew the retaining screw on each turn signal light housing with a Phillips screwdriver. Pull the housings towards you to release them. To remove the bulb sockets, turn them counter-clockwise and pull. Set the housings aside.
5Remove the bolts that are located inside the turn signal recesses with your wrench. Some Accords may have more plastic screws instead of bolts in the recesses.
6Remove the remaining plastic screw along the top of the bumper with your Phillips screwdriver.
7Separate the bumper by pulling it up and then sliding it towards you.
8Follow all steps in this section in reverse to install the new bumper. There are no torquing specifications for tightening the bolts.
Removing and Installing the Rear Bumper
- 9
Pry off, with a flathead screwdriver, the rear bumper to fender well clips that retain the bumpers forward ends.
10Unscrew and remove the five plastic screws at the top of the bumper with your Phillips screwdriver. Do the same for the four screws at the bottom of the bumper.
11Unscrew the side markers (lights) retaining screws with your Phillips screwdriver and take out the light housings. Turn the light sockets counterclockwise to remove the sockets and bulbs. Set the housings aside.
12Unbolt the two lower bumper retaining bolts using your socket wrench, underneath your Accord.
13Remove the trim panels from inside your Accords trunk and unbolt the upper retaining nuts with your socket wrench.
14Pull the bumper towards you and remove it.
15Follow all steps in this section in reverse to install the new bumper. There are no torquing specifications for tightening the bolts.
How to Replace an Oxygen Sensor on a 98 Honda Civic
A 1998 Honda Civic has two oxygen sensors: one between the catalytic converter and the exhaust pipe, and a second located behind the catalytic converter in the exhaust manifold. The purpose of an oxygen sensor is to monitor the oxygen levels in the exhaust. A bad oxygen sensor can cause the "check engine" light to come on. The engine may also run poorly and blow smoke out the tail pipe. Replacing an oxygen sensor is not difficult if you have right tools and time.
Instructions
- 1
Spray penetrating oil around the base of the primary oxygen sensor where it threads into the exhaust pipe. The oxygen sensor is located in exhaust components that heat up and cool down and may be difficult to remove. You will need to be under the Civic to access the sensor .
2Disconnect the oxygen sensor from the wiring harness.
3Place the ratchet and oxygen sensor socket over the top of the oxygen sensor. The socket has a slot for the sensor wires to pass through which allows you to loosen the oxygen sensor from its mounting collar. Turn the socket counterclockwise to loosen the oxygen sensor.
4Remove the socket from the oxygen sensor when it has become loose enough to turn by hand. Remove the oxygen sensor and discard. Oxygen sensors contain precious metals and should be recycled properly or returned to an automotive store.
5Install a new oxygen sensor into the threaded collar by hand and turn it clockwise until it is tight. Place the oxygen sensor socket over the top of the new oxygen sensor to fully tighten it. Connect the new oxygen sensor to the old wiring harness.
6Spray penetrating oil around the base of the secondary oxygen sensor where it threads into the exhaust manifold. Remove the secondary oxygen sensor from the engine compartment.
7Repeat Steps 2 through 5 to remove and install the secondary oxygen sensor.
Installation Instructions for the Teflon Insert Jam Nut

A jam nut is used in the same area as a locking washer and performs the same duty. Jam nuts are thinner than a traditional nut and contain a Teflon lining inside to hold tightly to bolt threads and secure it in place. Tightening a traditional nut on top of a jam nut causes stress on the jam nut and reverses the bolt strains so that each nut presses on the threads in opposite directions. Installing jam nuts on mechanical components that vibrate will keep the nuts from loosening.
Instructions
- 1
Insert a washer onto a hex head bolt and push it down to the head. Insert the threaded end of the hex head bolt into the items you are holding together. Slide a washer onto the end of the bolt threads and push it toward the material it is holding together.
2Insert a Teflon insert jam nut onto the protruding end of the bolt. Turn the nut clockwise and tighten it by hand. Tighten the jam nut completely with an adjustable wrench.
3Insert a nut on the protruding end of the bolt. Hand-tighten the nut clockwise and then tighten it completely on top of the jam nut with an adjustable wrench.
How to Replace a 2003 Grand Prix Thermostat

The 2003 Pontiac Grand prix uses a mechanical thermostat designed to increase the flow of radiator coolant through the engine when the temperature of the coolant surpasses 180 degrees. The thermostat prevents the engine from overheating. If the thermostat stops working, the design allows it to fail in a save position that allows fluid to flow unrestricted through the engine. This prevents overheating, but it also prevents the engine from producing enough heat to warm up the inside of the vehicle. When the thermostat breaks, replacement is the only option to correct the issue.
Instructions
- 1
Drain approximately 2 gallons of coolant into a clean drainage pan from the petcock located on the bottom of the radiator. You will reuse the coolant.
2Follow the upper radiator hose from the radiator on the Grand Prix to the intake manifold, where the hose connects to the water outlet housing. The thermostat rests inside the water outlet housing.
3Clean any debris away from the outlet housing with a towel or compressed air. It is common for leaves and other road dirt to build up around this area. A clean surface prevents any contaminants from getting into the cooling system.
4Remove the two bolts that secure the water outlet housing to the intake manifold on the Grand Prix with a socket and ratchet. Lift the housing off the intake manifold to expose the thermostat.
5Lift the old thermostat out of the intake manifold and shove a shop towel into the newly exposed hole.
6Scrape the old gasket off the surface of the intake manifold with a metal scraper or small wire brush. Do the same with the bottom of the water outlet housing.
7Remove the shop towel from the hole in the intake manifold and place the new thermostat into the hole. The end with the spring goes into the hole while the end with the pin sticks out.
8Place a new gasket over the thermostat and place the water outlet housing on top of the gasket. Secure everything with the two bolts.
9Open the lid on the radiator expansion tank and drain the 2 gallons of fluid back into the radiator.
How to Repair Damage to Chrome
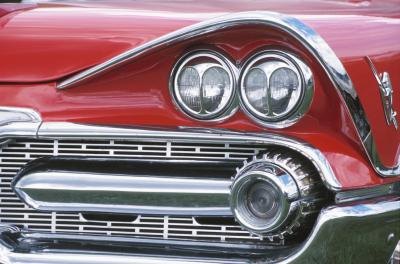
Chrome is not a metal surface, but is actually painted on to wheels, bumpers, and many other surfaces. When chrome is damaged it can sometimes be buffed out, but in the case of deep damage and scratches, will need to be treated and repainted. Before taking your damaged chrome in for expensive professional rechroming, you can try to fix the problem yourself with chrome primer, chrome paint and sandpaper.
Instructions
- 1
Sand the damaged spot and the surrounding area. Use 320-grit sandpaper on light scratches. For deeper scratches, holes or rusted areas use sandpaper with rougher grit such as 120 or 60.
2Clean off any sanding residue with a clean cloth.
3Fill in any holes or uneven surfaces with a glazing compound. Allow the compound to dry.
4Use 320-grit sandpaper to sand over the glazing compound to make it even. Use a clean cloth to remove sanding residue.
5Spray on a light coat of chrome self-etching primer to the entire chromed surface. Allow to dry, then apply a second coat. Allow the second coat to dry.
6Apply regular chrome primer over the self-etching primer. Use two to three coats, allowing each coat to dry thoroughly before applying the next.
7Wipe the surface gently with lacquer thinner.
8Apply chrome paint. Spray two to three thin coats of chrome paint to the entire chromed surface, allowing each coat to dry thoroughly before applying the next.
Sunday, October 27, 2013
How do I Remove a VE30DE Harmonic Balancer
The VE30DE is a six-cylinder 3.0-liter engine that Nissan used in the Maxima from 1992 to 1993. This engine has a crankshaft damper, or harmonic balancer, which reduces the harmonic vibrations that the crankshaft produces when it spins rapidly. The VE30DE engine has a solid pulley that also serves as the crankshaft damper and uses the same procedure to remove the crankshaft damper as other engines in Nissan Maximas made from 1992 to 1998.
Instructions
- 1
Disconnect the accessory drive belts from the crankshaft damper. Place a breaker bar between the teeth of the flywheel ring gear to hold the crankshaft in place. Remove the bolt that attaches the crankshaft damper to the crankshaft with a socket wrench.
2Attach a gear puller to the crankshaft damper and pull the crankshaft damper straight off the crankshaft. You may also be able to remove the crankshaft damper by hand. Ensure you dont lose the wood-ruff key when the crankshaft damper comes off the crankshaft.
3Discard the oil seal for the crankshaft and replace it with a new seal.
4Place the crankshaft damper onto the crankshaft, and install the wood-ruff key to the crankshaft. Coat the mounting bolt for the crankshaft damper with clean engine oil. Tighten the mounting bolt to between 123 and 130 foot-pounds with a torque wrench.
5Mount the accessory drive belts to the crankshaft damper.
How to Place a Timing Belt on a 1994 Toyota Tercel

The Tercel is a subcompact car manufactured by Toyota from 1978 to 2000. The fourth generation of this series includes 1991 through 1994. The standard engine for the 1994 Toyota Tercel is the 3E-E, a four-cylinder, 1.5-liter engine with a single overhead camshaft. The recommended replacement interval for the timing belt in a 1994 Tercel is at least 60,000 miles.
Instructions
- 1
Remove the cable from the negative battery terminal with a socket wrench. Disconnect the undercover on the right side of the engine, and detach the cables for the throttle and accelerator. Detach the PVC hoses and the accessory drive belts.
2Disconnect the air cleaner, air intake assembly and spark plugs with a socket wrench. Detach the vacuum valve from the mounting insulator on the right side of the engine.
3Place a floor jack under the engine and support the engine to take the weight off the engine mounts. Remove the insulator assembly for the right engine mount. Disconnect the valve cover with a socket wrench.
4Turned the crankshaft clockwise to align the timing mark on the crankshaft sprocket with the zero mark on the crankshaft housing. Disconnect the crankshaft pulley with a socket wrench. Remove the covers and guide for the timing belt.
5Detach the spring for the timing belt tensioner, and remove the tensioner spring. Loosen the idler pulley for the timing belt with a socket wrench, and push the idler pulley as far to the left as possible. Tighten the idler pulley to hold it in place temporarily.
6Remove the timing belt from the pulleys and disconnect the idler pulley with a socket wrench. Mount an adjustable wrench to the camshaft to hold it in place and remove the center bolt from the camshaft sprocket. Disconnect the sprocket from the camshaft.
7Remove the spring for the timing belt tensioner. Measure the free length of the spring at the inside faces of the hooks and replace the spring if this length is greater than 1.512 inches.
8Align the camshaft pin with the No. 1 mark on the bearing cap of the camshaft. Align the pin hole on the camshaft with the 3E mark on the camshaft sprocket. Install the camshaft sprocket onto the camshaft and tighten the retaining bolt to 37 foot-pounds with a torque wrench.
9Align the timing mark on the crankshaft timing pulley with the timing mark on the oil pump. Place the new timing belt onto the crankshaft sprocket and camshaft sprocket. Attach the spring for the timing belt tensioner and loosen the bolt for the idler pulley to apply tension to the timing belt.
10Tighten the bolt for the crankshaft pulley with a socket wrench. Rotate the crankshaft two full turns clockwise and align the timing marks again. Torque the bolt for the idler pulley bolt to 13 foot-pounds with a torque wrench.
11Replace the guide and covers for the timing belt with a socket wrench. Connect the crankshaft pulley and tighten its mounting bolt to 112 foot-pounds with a torque wrench. Perform steps 1 through 3 in reverse order to install the remaining components.
Specifications of a Stepper Motor
An electromechanical device, a stepper motor converts electrical pulses into mechanical movements. The motors spindle rotates in step increments when electrical pulses are applied in proper sequence. The speed of the motor directly relates to the frequency of these pulses.
Benefits
Step motors respond well to starting, stopping and reversing. With no contact brushes, step motors are extremely dependable and run until the bearings wear out. Step motors can achieve a wide range of rotation speeds due to speed being directly linked to the frequency of electrical impulses.
Specifications
A size 23 stepper motor has a shaft run-out of .001 inches. Radial play is a max .001 inch per one pound of force, while end play is .001 inches per 9 lbs. of force. Perpendicularity measures at .003 inches, with concentricity measuring at .002 inches. Operating temperature ranges from -4 degrees Fahrenheit to 122 degrees Fahrenheit with a insulation class of 266 degrees Fahrenheit. Stepper motors should be fitted with an American wire gauge (AWG) standard lead wire gauge of 26. The engine has a max radial load of 15 lbs. and max thrust load of 25 lbs..
Types
Size 11, 14, 17, HT17, HT23, 34, HT34 and 42 stepper motors have slight variations on their specifications than to the size 23 motor.
How to Repair a Spark Plug on a 2002 Ford Taurus

Spark plugs ignite the fuel in your engine to create even-burning combustion. Without properly functioning spark plugs, your car cannot burn gasoline efficiently. The only way to repair spark plugs is to replace them. Removing and replacing the spark plugs in your 2002 Ford Taurus is a very straightforward operation. With the right instructions and few tools, you can replace your own spark plugs to save a few bucks and a trip to the dealership.
Instructions
- 1
Park your car on a level surface and apply the parking brake. Allow your engine to thoroughly cool before you begin to remove and replace the spark plugs.
2Pop open your 2002 Ford Taurus hood and located the spark plugs. If you cant find the spark plugs, consult your owners manual (if you have lost your manual, see the link in the Resources section).
3Gently remove the spark plug wire by pulling on the boot and not the wire itself to avoid any damage.
4Attach a spark plug socket to a socket wrench (attach a swivel or extension if you need any added length to reach the spark plug) and remove the spark plug by turning it counterclockwise. Thoroughly clean the spark plug hole with rubbing alcohol and a clean rag.
5Apply a thin coat of anti-grease onto the new spark plug. Start the spark plug in the spark plug hole using just your hand. Tighten the spark plug with the spark plug socket until its tight, but be sure not too over tighten. Reconnect the spark plug wire. Remove and replace all the spark plugs one by one until you have finished replacing all damaged spark plugs.
What Is a Normal Shock Absorber Life
Although all shocks give a manufacturers suggested replacement period, there isnt any way to determine the actual lifespan of an individual shock absorber. The normal lifespan is influenced by real world driving conditions.
Suggested Maintenance
The majority of car manufacturers suggest replacing shocks every 60,000 to 80,000 miles. Most shock replacements fall into this time frame.
Normal Lifespan
According to the website Basic Car Repair, "shock absorber life depends primarily on the roads over which you drive." They might fail almost immediately, at say 5,000 miles, or might last well into the 60,000 to 80,000 mile range. The average manufacturer suggested replacement time is between 20,000 and 30,000 miles.
Individual Shocks
An individual shock may be structurally defective and should be checked periodically, whenever you do basic maintenance. Because there is no way to predict the life expectancy of shock absorbers your best bet is to pay attention to the way your car feels when it goes over bumps. If there is a sudden change and you start to feel residual bouncing after hitting a bump, it is probably time to check the shocks.
Saturday, October 26, 2013
Steels Used in Piston Rings
The piston ring is a seal between the piston and the cylinder designed to prevent gas leakage around the piston. Piston ring material must withstand high temperature and friction to function properly. Engine technology has changed over time and so has piston ring material.
Cast Iron
Cast iron piston rings are good choices for engines. The material is compatible with the sides of a cast iron block so it wont gall. With newer high-performance engines, it isnt as good of a choice. Cast iron is heavy and somewhat brittle. It requires a thicker ring to handle engine loads.
Steel
Modern engines use steel piston rings. Steel is thinner and can withstand higher pressures and heat that modern engines produce. Because they are thinner, lighter and stronger, steel is a better choice for higher performance engines.
Coatings
To further improve wear and reduce friction and corrosion, it is possible to coat steel piston rings with chrome or other materials. Steel rings accept coatings easier than iron rings.
How to Install a Brake Controller on a 1999 Suburban
A Suburban is a sport utility vehicle that General Motors manufactures under its Chevrolet brand. The anti-lock braking system (ABS) is a standard feature on late-model Suburbans that allows the vehicle to stop more effectively in an emergency. A brake controller, or electronic brake control module (EBCM), reduces the braking force to a wheel when it rotates significantly more slowly than the other wheels. The installation procedure for the EBCM is generally the same for all Suburbans made from 1999 to 2005.
Instructions
- 1
Disconnect the cable from the negative battery terminal with a socket wrench to prevent an electrical discharge during the EBCM installation procedure. Raise the vehicle with a floor jack, and support it on jack stands.
2Locate the Electronic Hydraulic Control Unit, or EHCU, under the vehicle on the drivers side. It is bolted on the frame next to the drive shaft. The EHCU is an assembly of the EBCM, the brake pressure modulator valve (BPMV) and a mounting bracket. The mounting bracket attaches to the frame of the vehicle, the BPMV attaches to the mounting bracket and the EBCM attaches to the top of the BPMV. The EHCU is generally a black cube about 3 inches on a side with connections for the brake lines and the ABS pump motor when it is fully assembled. Wash the area around the EHCU with a shop rag to avoid contamination of the EBCM.
3Detach the electrical connector from the EBCM. The EBCM is a thin, black, rectangular box mounted atop the BPMV. Remove the fittings for the brake lines with a socket wrench and disconnect the brake lines from the BPMV. The BPMV is the component under the EBCM that has connections for the brake lines and attaches to the EHCU mounting bracket. Remove the mounting bolts for the EHCU bracket with a socket wrench and disconnect the bracket from the vehicle.
4Disconnect the mounting bolts for the BPMV with a socket wrench and detach the BPMV from the EHCU. Disconnect the electrical connector for the ABS motor from the EBCM. Remove the mounting bolts for the EBCM, and detach the EBCM from the BPMV.
5Clean the mounting surface on the BPMV with a clean shop cloth. Mount the new EBCM onto the BPMV, and fasten the EBCM with the retaining bolts that came with the EBCM. Tighten the retaining bolts to 39 inch-pounds with a torque wrench. Attach the electrical connector for the ABS motor to the EBCM.
6Install the BPMV to its bracket and tighten the mounting bolts to 80 inch-pounds with a torque wrench. Connect the EHCU to the vehicle and tighten the EHCU bracket bolts to 18 foot-pounds. Attach the electrical wiring harness to the EBCM.
7Attach the brake lines to the BPMV and tighten the fittings to 18 foot-pounds with a torque wrench. Lower the vehicle, and connect the cable to the negative battery terminal with a socket wrench. Bleed the brake system.
How to Reset the Computer in a Jeep Cherokee

You can reset the computer in your Jeep Cherokee from your home garage, saving yourself time and money. The PCM (power train control module) or computer controls the Cherokees ignition, fuel system, emission and other systems. When it detects a malfunction in any of the vehicles systems, it will alert you with a warning light on the instrument panel. It will also let you know when your Jeep needs regular servicing. After you have had the repairs or servicing done, you or your mechanic will need to reset the computer to keep it functioning properly.
Instructions
- 1
Find the Data Link Connector port next to the fuse panel under the drivers dashboard. Plug the computerized scan tool into this port.
2Check the computerized scan tools owners manual on exactly how to clear the codes and reset the computer because each model is a little different. Most scan tools will have a "delete codes" command on the faceplate or within the menu that you can scroll to and select.
3Delete all codes. This will reset the vehicles computer. Unplug the scan tool.
4Put the key into the ignition and start the vehicle. Verify that all warning lights and service lights have shut off on the instrument panel.
How do I Remove a Rear Window on a 1973 GMC Pickup
Removing the rear window from your GMC pickup is necessary to replace it with a new one or to upgrade to an aftermarket window. Sliding rear windows, tinted windows or a new window from GM are all great options if your truck needs new rear glass. Most auto glass shops can sell you a new window or an aftermarket replacement. Some salvage yards sell replacement glass as well, but keep in mind that used glass may not hold up as well. Small stress points could cause it to break during installation.
Instructions
- 1
Open the doors of the truck so you can work on both sides. Then slide the bench seat as far forward as it will go. Lean the seat back forward and climb in behind the seat.
2Slide a small, thin screwdriver between the body and the rubber gasket surrounding the window. Pull down on the gasket without prying on the glass or it will chip. All you are trying to do is get the gasket below the metal around the window.
3Pull the gasket down several inches away from the first spot, using an additional screwdriver. Hold the gasket down and work along the edge of the window while pushing out on the glass lightly.
4Push the glass and gasket out until the top section is outside of the body. Then pull the window up and out of the rubber gasket. Remove the gasket from the window opening by pulling it away from the body all the way around.
Why the Brake Lights Stopped Working

Brake lights are an important safety feature on cars, trucks and other vehicles. Brakes lights that have stopped working need to be fixed as quickly as possible. Fortunately, most brake light problems are easy to diagnose and repair.
Bulb Problems
When one brake light stops working, the most common reason is that the bulb has burned out. Bulbs are inexpensive and easy to replace, though accessing them can be difficult on some vehicles. Some brake light housings must be removed from the outside, while others are accessed behind the trim inside the trunk of the car.
Blown Fuse
If all of a vehicles brake lights stop working at once, the most likely reason is a blown fuse. The owners manual for the vehicle will direct the car owner to the location of the fuse box. The manual will typically have a diagram of the fuse box (a diagram may also be included on the fuse box cover), allowing the car owner to quickly locate and replace the fuse for the brake lights.
Other Problems
Wiring may break or become loose, causing problems with the brake lights. A visual inspection of the brake wiring may show damaged areas that need repair. The brake lights may also fail if bulb sockets become too worn.
Friday, October 25, 2013
95 Camaro Troubleshooting

The 1995 Camaro is a sportscar manufactured by Chevrolet. The 1995 model comes with a V-6 engine along with a multipoint fuel injection system. If you are having problems with your 95 Camaro, there are several things you can do before taking it into a service shop. Common issues occur with the fuel, battery or the spark plugs on the car. These repairs dont have to be done by a technician. You can do them yourself.
Instructions
- 1
Pop the hood to gain access to the battery. Make sure that the connections from the cables are tight with the battery terminals. Use a pair of insulated pliers to tighten the connections. Look over the connections for any corrosion. Clean the connections with soda and a wire brush to remove the corrosion.
2Turn the ignition to the "On" position to engage the instrument panel. Look over the gauges to make sure you have enough fuel to start the car. Fill the tank if you need more fuel. If the gauges will not turn on, you have a problem with your battery. Connect the battery to a battery charger and leave it overnight. Try to restart the car. Replace the battery if the car will not restart.
3Look over the coolant levels if the car is overheating. The cooling system is on the left side of the engine under the hood. Fill the coolant system with 50/50 coolant to remedy the problem. You can use regular water if needed until you can get coolant.
4Pull the spark plug from the spark plug housing on the engine. This is labeled as "Spark Plug" on the engine. Touch the spark plugs wire to the metal on the car. Look for a blue spark from the spark plug. Blue sparks mean that the spark plug needs to be replaced. Spark plugs can be found at local auto repair shops.
5Look at the bottom of the car for any leaks. If you do find a leak, have the Camaro towed to a service shop for further inquiry. Repair shops have specific tools for diagnosing leaks.
How to Fix a Toyota Corolla Door Handle That Wont Open

Toyota Corollas door handles can get stuck or simply not opening doors. The 2004 Toyota Corolla repair manual includes a little information on how to remove the inside door panel, but you may need help from a professional. In a few easy steps, your car door handles can be replaced or fixed.
Instructions
Removing the Car Door Panel
- 1
Remove the interior door panel. Remove the screws holding the panel to the door and "unsnap" the plastic panel siding. The 2002 Corolla has three screws as well as the snaps. The handle casing has one screw and two underneath the armrest in the middle of the panel.
2Open the door and keep it open while manually locking the door, then use a screwdriver to unscrew the broken door handle. Set this screw in a safe place. You must remove the broken piece entirely. If you cannot remove the broken handle entirely, there is another solution later.
3Remove the armrest by pulling it up from the snaps. You may need to wedge a flathead screwdriver under the pad to push it up and reveal the screws beneath. Unscrew these two screws and set aside with the other.
4Check inside the door handle compartment for possible broken parts or pieces missing. There may be something lodged or wedged inside the handle. Take a wiping cloth or wet towel and clean the area, then check the door handle from the outside. If it is still stuck, then you simply need to replace the car door handle.
Replacing a Toyota Corolla Door Handle
- 5
Remove the door handle by starting at the bottom left or right side of the doors panel. Put your fingers under the plastic and pull it from the snap. It should come loose with a bit of pressure.
6Unsnap each part of the door panel. This is a tedious process but the entire door panel must come off. Then lift the panel up and over the locking device once the panel is free. Try supporting the panel with your legs. Try to not let the panel fall to the ground. You may need assistance. If you have power windows and locks, there will be wires coming from inside the door panel, which will restrict how far the panel can be moved. Do not disturb these wires.
7Lift the panel up and over the locking device once the panel is free. Support the panel with your legs. Try to not let the panel fall to the ground. You may need assistance. If you have power windows and locks, there are power chords andd wires coming from inside the door panel which restricted how far the panel could be moved. Do not disturb these wires in any way.
8Look inside the door for a metal arm with an L-shaped end extending out to where the door handle was before. The tip of the metal arm needs to insert into the new door handle.
9Take the metal arm and attach it to the door handle. The door handle needs to be inserted into place inside the door panel. Snap the metal arm once inside the door handle. You may need pliers for this.
Reattach the Door Panel
- 10
Attach the door handle in the door panel to the door itself. Three arms extend from the back of the door handle. There are two L-shaped arms, and one is a cylinder. They match the receiving pieces in the door frame. Line each of these as you push the door panel back on.
11Realign the door panel by lifting it up and over the locking device before lowering it back into position.
12Slide the door panel to one side as the door handle slides into place into the door. This brings the hole of the screw into line with the corresponding hole in the door.
13Snap the door panel back into place. You will need to press hard on the door panel and listen to each one snap to make sure that it is securely fastened back to the door.
14Test the handle after closing the door. Screw in the three screws from before and replace the armrest pad by snapping it back on.
How to Adjust Rhoads Lifters
Proper adjustment of Rhoads lifters, or any hydraulic lifters, is crucial to engine performance. If the rocker arms are not tight enough, tappet noises or bent push rods may result. If the rocker arms are too tight, the lifter may bottom out or the valve may not completely close, causing either poor engine performance or internal engine damage. While all that seems scary and adjusting Rhoads lifters is a time-consuming proposition, the procedure is relatively simple.
Instructions
- 1
Bring the piston in the No. 1 cylinder to TDC on the compression stroke. TDC, or top dead center is when the piston reaches the top of its travel and both the intake and exhaust valves are closed. Both the intake and exhaust lifters will be sitting on the low sides of their respective cam lobes when the piston is in TDC.
2Tighten the rocker arms on that cylinder using any tools necessary from a toolkit until the push rods starts compressing each lifters plunger. Continue tightening the rocker arms until the push rods compress the plungers cylinder 1/16 inch below the retaining ring. This normally takes three-quarters of a turn on the nut.
3Repeat for all other cylinders.
What Are Typical 134A Manifold Gauge Pressures

A vehicles air conditioning system is an important component in hot weather. The 134A refrigerant, and its resulting manifold pressure, provide a way to maintain the coolest air for the vehicles occupants.
Function
Run through a cars air conditioning system, 134A refrigerant acts as the cooling conductor for the air. Periodically, the refrigerant can become low, resulting in warmer air through the system and into the vehicle.
Features
While recharging the system with refrigerant, the 134A manifold gauge pressure should be monitored so the proper amount of refrigerant is used. Two different pressure gauges can be used, either low or high. For a low pressure gauge, a reading of 25 pounds per square inch (psi)to 40 psi is optimum. On the other hand, a high pressure gauge should read between 225 psi and 250 psi.
Considerations
If the refrigerant becomes low after a few months of circulation, there may be a leak in the system. AA1 Car recommends having the leak repaired before trying to recharge the system again.
How to Turn Off the Seat Belt Warning Sound in a 2003 F150

A 2003 Ford F150 is equipped with a seat-belt warning sound that reminds you to fasten your seat belt. This chiming turns on when you start the car, and the quickest way to stop it is to fasten your seat belt. You can disable this sound if you want. Just keep in mind that in many states its illegal to drive without your seat belt fastened.
Instructions
- 1
Get inside the drivers side of the truck and make sure all doors are closed. Set the parking brake. Make sure the headlights are off, and your seat belt is unbuckled.
2Put the key into the ignition and turn it to the "off" position. Next, turn the key to the "on" position and wait about two minutes or until the seat-belt warning sound shuts off.
3Fasten and unfasten the seat belt three times, making sure that you end with the seat belt unfastened.
4Turn on the headlights for three seconds then shut them off.
5Repeat the step of fastening and unfastening your seat belt three times. Wait for the seat-belt warning light to illuminate and then disappear. When it turns off, fasten and then unfasten the seat belt one more time to disable the seat-belt warning sound.
Thursday, October 24, 2013
How to Get the Front Wheel Off of a 2005 F250 Super Duty 2WD Truck
The front wheels on a 2005 F250 Super Duty truck are designed to withstand heavy duty work. Because the F250 is a heavy duty truck, the wheels have eight lug nuts, instead of the usual five or six lug nuts found on light duty trucks. The lug nuts are a special swivel-type nut, designed to stay tight in situations where normal fixed nuts can loosen. Its also important that you never apply any lubricant such as engine oil to the wheel studs or lug nuts, because this could also cause them loosen under certain circumstances.
Instructions
Removal
- 1
Park the F250 on a flat, level surface and turn off the engine. Shift the transmission into park, or first gear for F250s equipped with a manual transmission.
2Press the parking brake pedal down to engage the parking brake. Place one wheel chock behind each of the rear wheels. Pry the hub cap loose, if equipped, with a large flat-head screwdriver.
3Break each of the eight lug nuts loose with a lug nut wrench. This is important, because if you try to loosen the nuts when the vehicle is lifted, the wheel will spin and you wont get any leverage.
4Lift the front of the truck with a jack and place a jack stand under each side of the front frame. Lower the truck onto the jack stands and make sure theyre secure.
5Remove the lug nuts with the lug nut wrench and pull the tire off of the truck.
Installation
- 6
Set the wheel onto the studs and reinstall the lug nuts. Snug them tight with the lug nut wrench while holding the wheel to make sure it doesnt turn.
7Lift the truck with the jack, then remove the jack stands and lower it back to the ground.
8Tighten the lug nuts to 165 foot-pounds with a torque wrench an metric socket in an alternating, criss-cross pattern.
9Place the hub cap onto the wheel and tap it down into position with a rubber mallet.
How to Lower the Fork Springs on a Harley Davidson Road King

Lowering the forks on a Road King is a much tougher job than lowering the forks on a Softail, Dyna or Sportster. Harley sells a parts kit to help you accomplish the job. Three special tools are required to install the kit to Harley specifications. You must also replace 8 sets of parts that are not included with the kit. But if you have been yearning for an excuse to take your forks completely apart, you enjoy collecting tools, you own a beach towel you have always hated and you have a spacious, well equipped place in which to work, then this is the right job for you.
Instructions
Remove The Forks
- 1
Detach the windshield from the Road King using the quick detach clips. Elevate the motorcycle on a motorcycle jack until the front tire leaves the floor.
2Loosen and detach the front caliper using a hex socket and a socket wrench. Hook a bungee cord to the caliper. Hook the other end of the bungee cord to the handlebars.
3Loosen the axle nut with a hex socket and socket wrench. Pull the complete axle assembly out of the wheel. Remove and set aside the front wheel.
4Loosen the fender mounting screws using a socket wrench and socket and an Allen wrench. Remove the four screws and the front fender.
5Loosen, mark for reference with tape, then remove the upper and lower fork bracket pinch bolts using an Allen wrench, a socket and a socket wrench. Carefully lower the fork assembly out of the fork brackets. Wrap the forks in a beach towel.
Disassemble The Forks
- 6
Remove the nuts, lock washers, flat washers and axle holder from the studs at the end of the fork slider with an Allen wrench and an open end wrench.
7Clamp the Harley-Davidson fork tube holder or equivalent horizontally in a bench vise. Clamp one fork tube vertically, with the fork cap bolt up, between the rubber pads of the fork tool. Tighten the knobs on the fork tube tool by hand.
8Remove the fork cap bolt from fork tube plug with a large adjustable wrench. Remove and discard the quad ring seal.
9Remove the fork tube plug as if you know there is a compressed spring in the fork tube under the plug. Remove the fork spring from the fork tube.
10Unloosen the fork from the fork tube holder. Insert the opposite fork tube in the holder and remove the fork cap bolt, fork tube plug and spring from the opposite fork.
11Remove the fork assembly from the fork tube holder. Turn the fork upside down and drain the fork oil into a drain pan.
12Put the old fork spring back into the right fork tube. Work on one fork at a time.
13Put a folded shop rag on the floor. Turn the fork assembly upside down and push the end of the fork spring against the rag to compress the spring. Compress the spring and remove the remaining screw on the bottom of the fork slider with an Allen socket and an air impact wrench.
14Discard the copper, crush gasket and the screw.
15Remove the fork spring and the damper tube from the fork. Remove the rebound spring from the damper tube. Save the rebound spring and discard the fork spring and damper tube.
16Reinstall the forks into the fork tube holder. Remove the remaining screw on the bottom of the slider, the crush gasket, fork spring and damper from the left fork tube using the same procedures that you applied to the right fork tube.
17Remove the retaining clips between the fork sliders and the fork tubes with a mechanics pick or a dental pick.
18Remove the fork tubes from the fork sliders. Slide the fork oil seals, slider spacers and slider bushings off the end of the fork tubes. Discard fork oil seals and slider bushings.
19Pry open the split lines on the fork tube bushings with a flathead screwdriver and remove them from the grooves at the end of the fork tubes. Discard the fork tube bushings.
20Remove the two lower stops from the two fork sliders. Clean all disassembled parts with solvent and rags.
Reassemble The Forks Part 1
- 21
Coat the replacement fork tube bushings with new, clean fork oil. Expand the fork tube bushings at split line with a flathead screwdriver and slip each over the ends and into the grooves on the two fork tubes.
22Install replacement wear rings in the grooves at the tops of the two new damper tubes included with the lowering kit. Install the old damper springs on the new damper tubes.
23Slide the new damper tubes into the old fork tubes. Reinstall the lower stops into the new damper tubes.
24Push the fork sliders into the fork tube holders. Slide the fork tubes into the fork sliders.
25Coat the replacement slider bushings with fork oil and slide the new bushings down the fork tubes. Push the slider spacers included with the kit down the fork tubes until each contacts the slider bushing on that fork tube.
26Cover the lips of the fork tubes with masking tape. Coat the replacement fork oil seals with fork oil. Slide the new fork seals spring side down into the fork tubes until they contact the slider spacer. Remove the tape from the fork tubes.
27Slide the fork seal/bushing tool down one fork tube at a time and use it like a slide hammer to drive the fork oil seal into that fork tube until, using a flashlight, you can clearly see the retaining clip groove in the fork slider. Repeat this on the opposite fork tube.
28Slide the old retaining clips down the fork tubes until they contact the fork oil seal.
29Slide one of the new fork springs included with the kit down the right fork tube. Place a folded shop rag on the floor.
30Remove the fork assembly from the fork tube holder. Turn the assembly upside down and forcefully press the end of the fork spring against the folded rag.
31Install a replacement end screw and replacement copper crush washer. Tighten the end screw to 18 foot pounds of torque with an Allen socket and a torque wrench. Remove the fork spring from the tube and place it in the opposite fork tube.
32Repeat the procedures you just completed to install the end screw in the opposite fork tube. Remove the fork spring from the fork tube.
Fork Reassembly Part 2
- 33
Shove one fork tube into one of the fork sliders. Clamp the fork slider, fork tube side up, into the fork tube holder.
34Measure 11.2 ounces or 300 milliliters of Type E fork oil or equivalent into a pint measuring cup. Pour the fork oil into one of the fork tubes. Pump the fork tube four times to remove air from the fork. Repeat for the opposite fork tube.
35Loosen the thumbscrew on the metal ring on the fork oil level gauge. The gauge looks like a bicycle pump with a transparent tube. The metal ring is attached to the transparent tube.
36Slide the metal ring up or down the transparent tube and tighten when exactly 4.92 inches, or 125 millimeters, of transparent tube extends beyond the metal ring.
37Completely depress the handle of the fork oil level gauge. Rest the metal ring on top of the fork tube.
38Pull the fork gauge handle up to suck excess oil out of the fork tube. When no oil comes out of the fork tube the fork oil level is just right.
39Pour 11.2 ounces of fork oil into the opposite fork tube and correct the fork oil level with the fork oil level gauge as above.
40Install new, replacement O-rings onto the 2 original fork tube plugs. Screw the fork tube plugs into the tops of the fork tubes and hand tighten both plugs.
41Install new quad ring seals onto the two old fork cap bolts. Thread the fork cap bolts into the fork tube plugs and tighten 55 foot pounds of torque with a 1 1/8 inch socket and torque wrench.
Final Reassembly
- 42
Carefully slide the fork assembly up and into the fork brackets. Replace and tighten the upper and lower fork bracket pinch bolts using an Allen wrench, a hex socket and a socket wrench. Tighten the pinch bolt nuts to 30 foot pounds of torque with a hex socket and torque wrench.
43Replace the front fender and tighten the four mounting screws using a socket wrench and hex socket and an Allen wrench.
44Replace the front wheel and axle assembly. Tighten the front axle nut to 50 pounds of torque with a torque wrench and hex socket.
45Reattach the brake caliper and tighten the mounting bolts to 35 pounds with a torque wrench and hex socket.
46Lower and remove the motorcycle jack. Replace the windshield.
How to Remove a 96 Galant ECM
All 1996 Mitsubishi Galants contain an engine control unit, also referred to as the ECM or ECU. This unit is fastened to the underside of the dashboard, beneath the radio and climate controls in the center section of the vehicle. The ECU is responsible for controlling the engine, transmission and other powertrain components. A malfunctioning ECU can cause an extremely wide range of symptoms due to the number of components that it controls. Some Galant owners are focused on the increasing the horsepower and performance of their engine. These owners may opt to remove and replace a properly functioning ECU with a unit that has been custom programmed to increase engine performance.
Instructions
Removal
- 1
Open the hood and locate the battery on the left side of the engine bay. Disconnect the negative battery terminal using a metric wrench.
2Remove the two screws holding the radio console panel to the dashboard with a Phillips screwdriver. Insert a flat-head screwdriver in between the radio console panel and the dashboard. Pry around the outside edge of the console panel until it pops loose. Remove the console panel.
3Remove the screws holding the radio and cup holder unit to the dashboard with a Phillips screwdriver. Slide the assembly out of the dashboard. Remove the screws from the bracket holding the cup holder to the radio assembly, then remove the bracket and the cup holder assembly.
4Disconnect the electrical connectors from the radio and remove it from the vehicle.
5Locate the ECU. It is a square metal box located directly underneath the radio. Remove the bolts holding the ECU to the vehicle with a ratchet and metric socket, then lift the ECU up and out of the console area. Disconnect the ECUs electrical connector and remove it from the vehicle.
Installation
- 6
Reconnect the ECUs electrical connector and set the ECU into position.
7Install the ECUs retaining bolts and tighten them to 43 inch-pounds with a torque wrench.
8Reconnect the radios electrical connectors and set the cup holder assembly into position under the radio. Set the side bracket into position and reinstall the bracket screws.
9Set the radio and cup holder assembly back into the dashboard and reinstall the radio retaining screws. Set the radio console panel into position and press down on it until it snaps into place.
10Reinstall the radio console panels retaining screws. Reconnect the negative battery terminal.
How to Replace Catalytic Converters on a Lexus LS 400
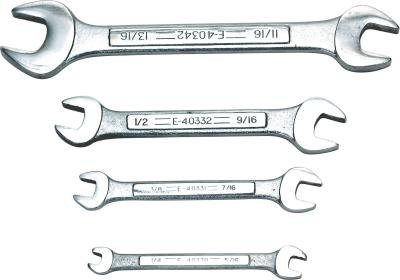
The catalytic converters in your Lexus LS400 are three-way converters that lower exhaust emissions through a chemical reaction between the exhaust gas and the substrate in the converter. This type of converter features the reduction capabilities of a reduction converter to lower oxides of nitrogen (NOx) and the oxidation capabilities of an oxidation converter to lower carbon monoxide (CO), carbon dioxide (CO2) and unburned hydrocarbons. Replacement catalytic converters in the Lexus LS400 come installed in an exhaust pipe assembly making replacement easier.
Instructions
- 1
Apply the parking brake and set wheel chocks behind the rear wheels. Raise and support the front of the Lexus using a floor jack and jack stands positioned under the front sub-frame. Lower the car onto the stands slowly so that the weight of the car is supported evenly by the jack stands. Remove the floor jack.
2Allow the exhaust system to cool completely. The catalytic converters on the LS400 operate at a high temperature (over 600 degrees Fahrenheit) and can cause severe burns if not allowed to cool sufficiently prior to working on the system.
3Spray the attaching bolts on the converter with a liberal coating of penetrating oil and allow it to sit for a few minutes. Remove the two rear mounting bolts that attach each of the converters to the exhaust system using a 13mm socket and ratchet to turn the bolt while holding the 15mm nut with a wrench. Pry the exhaust system back away from the converter and pull the exhaust downward.
4Remove the three 13mm nuts that attach the converter to the exhaust manifold and pull the converter off the manifold studs. Use a new exhaust gasket between the converter and manifold. Bolt in the new converter, leaving the nuts loose so the converter can be moved slightly while lining up the rest of the exhaust system.
5Raise the exhaust system and pry it back until it can be slipped onto the converter. Place a new gasket between the converters and the exhaust system. Install and tighten all of the nuts and bolts securely.
Wednesday, October 23, 2013
How to Install a Brake Controller on a Chevy
An anti-lock brake controller prevents the brakes from locking the wheels in an emergency stop. It accomplishes this by varying the braking force to each wheel during emergency stops or when skidding on a slippery surface. Anti-lock braking systems became standard on most Chevrolet vehicles by about 1991. The procedure for installing a brake controller is the same for many General Motors cars made from 1988 to 1996, such as the Lumina, Grand Prix, Cutlass Supreme and Regal.
Instructions
- 1
Turn the ignition switch off and move the front passenger seat forward as far as possible. You may also need to tip the passenger backrest forward to access the brake controller underneath the seat.
2Remove the mounting bolts on the cover of the brake controller case with a socket wrench, and slide the controller from its case. Remove the connector position assurance (CPA) locking pins, and detach the electrical connector from the brake controller. Remove the brake controller from the vehicle.
3Attach the electrical connectors to the new brake controller. Install the CPA locking pins to ensure a good electrical connection.
4Place the new brake controller in its case, and replace the cover for the case. Install the mounting bolts for the cover, and tighten the retaining bolts by hand.
5Return the front passenger seat to its original position.
How to Replace the Water Pump in a 2005 Hyundai Elantra

The Hyundai Elantra is a compact car made by Hyundai Motor Corporation since 1991. The 2005 model belongs to the third generation, which was in production from 2000 to 2006. The water pump on this vehicle circulates coolant around the engine to prevent it from overheating. The water pump in a 2005 Hyundai Elantra attaches to the front of the engine, and requires the removal of several other components to access.
Instructions
- 1
Place a drain pan under the radiator and remove the radiator cap to speed the draining process. Open the radiator drain plug and allow the coolant to drain out of the radiator. Replace the drain plug and radiator cap.
2Disconnect the negative battery cable with a socket wrench to prevent the battery from producing sparks. Remove the accessory drive belts. Disconnect the hose to the radiator and the bypass hose, if your vehicle is so equipped.
3Remove the pulley for the water pump with a socket wrench. Disconnect the front cover for the timing belt and the timing belt. Remove the bracket for the alternator.
4Remove the mounting bolts for the water pump with a socket wrench and record their location, since the bolts have different lengths. Detach the water pump from the engine block and discard the gaskets.
5Install the new water pump and gaskets to the engine block. Tighten the mounting bolts to between 14 and 20 ft. lbs. with a torque wrench.
6Connect the alternator bracket with a socket wrench. Install the timing belt and its front cover. Attach the pulley for the water pump and the hoses for the radiator. Connect the accessory drive belts.
7Attach the the cable to the negative battery cable with a socket wrench and fill the radiator with coolant. Start the engine and check for coolant leaks.
How to Cut a Steel Auto Fuel Line
Vehicle fuel systems operate under high pressure. Steel fuel lines keep high-pressure fuel contained on route between the fuel tank and the fuel delivery system. Correctly installing steel fuel lines entails producing straight cuts on the ends of the line. This ensures the lines will seat properly in the compression fitting connecting two pieces of line or connecting the line to fuel system components. Improperly cut fuel lines create a situation where fuel can escape from a crooked edge.
Instructions
- 1
Mark the cut location on a piece of steel fuel line with a piece of soapstone.
2Open the jaws of a tubing cutter by turning the lower knob counterclockwise. Stop turning the knob when the distance between the top rollers and the bottom cutting blade allows enough room for the steel fuel line.
3Slide the fuel line in the open jaws of the tubing cutter. Align the cut mark with the center of the bottom cutting blade. Turn the cutter knob clockwise until the blade contacts the surface of the tube. Turn the knob clockwise a quarter turn to apply pressure to the line.
4Spin the tubing cutter around the fuel line for two revolutions. Turn the knob clockwise a half turn. Spin the cutter an additional two revolutions. Continue tightening and spinning the tubing cutter until it cuts through the steel fuel line.
5Place the tapered end of the burr remover -- located on the back face of the tubing cutter -- inside the cut end of the fuel line. Apply pressure toward the fuel line. Turn the tubing cutter to clear the burr from inside the fuel line.
How to Remove a VW Beetle 1 8 Turbo Head Gasket
The New Beetle comes equipped with a variety of engines, including a 1.8-liter engine with a turbocharger. The cylinder head in a New Beetle is a platform that sits on top of the engine block and forms part of the combustion chamber. A gasket between the cylinder head and engine block ensures a tight seal between the two components. The procedure for removing the cylinder head gasket in a New Beetle requires you to put the lock carrier in the service position. The lock carrier is the front assembly that includes the front bumper, headlights and radiator support.
Instructions
- 1
Disconnect the front bumper from the lock carrier with a socket wrench. Remove any electrical wiring needed to move the lock carrier into the service position. Disconnect the quick-release screws from the front insulation panel. Then, remove the air guide between the air filter and lock carrier. Release the retaining clamps that attach the wiring harness to the left radiator frame.
2Remove the No. 2 mounting bolts from the lock carrier with a socket wrench and support it with Support 3369. Remove the remaining mounting bolts from the lock carrier and pull the lock carrier out as far as it will go. Fasten 6 mm bolts to the lock carrier and fender to secure the lock carrier in place.
3Disconnect the cable from the negative battery terminal to ensure the engine doesnt start while you are removing the cylinder head gasket. Detach the cooling fan drive belt from its pulleys and remove the cooling fan from the engine.
4Drain the coolant from the radiator into a container and store for later use. Disconnect the intake manifold from the engine with a socket wrench. Detach the accessory drive belts from their pulleys.
5Remove the regulator valves for the wastegate bypass and the evaporative emissions canister from the engine with a socket wrench. Detach the mass airflow sensor from the engine.
6Disconnect the housing for the air cleaner with a socket wrench. Detach the wiring harnesses for the engine-coolant temperature sensor and any other electrical components needed to access the cylinder head. Detach the breather line from the crankcase.
7Remove the fuel lines and oil line from the cylinder head. Disconnect the heat shield and turbocharger from the exhaust manifold with a socket wrench. Detach the coolant hose from the rear of the cylinder head.
8Detach the upper cover for the timing belt with a socket wrench. Turn the crankshaft clockwise to align the timing mark on the crankshaft with the top dead center mark on the crankcase. Loosen the Torx bolt on the timing belt tensioner with a T45 Torx wrench and push the tensioner down to relieve the tension on the timing belt.
9Remove the timing belt from the gear of the camshaft, and remove the Torx bolt from the timing belt tensioner with the T45 Torx wrench. Rotate the bracket for the timing belt tensioner forward to access the valve cover and then remove the valve cover with a socket wrench.
10Disconnect the mounting bolts for the cylinder head with a socket wrench. Lift the cylinder head from the engine block and remove the gasket from the engine block. Clean the remaining traces of gasket material from the cylinder head and engine block with a gasket scraper. Clean the bolt holes on the cylinder head with a shop cloth and blow them dry with compressed air.
Jeep Cherokee Engine Problems

Chrysler has issued various safety recalls for manufacturing defects that could result in Jeep Cherokee engine problems. Concerned drivers may contact the National Highway Traffic Safety Administration (NHTSA) to verify whether their Jeep transmission problems are associated with these or other recalls.
Control Module Defect
On February 5, 2008, Chrysler recalled 1,338 Jeep Grand Cherokees because of a manufacturing error in the front control module. This defect could cause the engine to stall unexpectedly, a potentially dangerous condition.
Fluid Leak
On September 8, 2005, Chrysler recalled 101,925 Jeep Grand Cherokees equipped with 3.7L engines and NAG1 automatic transmissions. A leak may develop in which air conditioner evaporator condensate water gets into the transmission and causes shuddering when the torque converter clutch engages. This leak can cause an engine fire if the water gets hot enough and transmission fluid is subsequently purged into the engine.
Sensor Wire Defect
On March 2, 2004, Chrysler recalled 14,621 Jeep Grand Cherokees equipped with 4.0L engines due to a manufacturing defect in the crankshaft position sensor wire. The wires insulation may crack and leave the wire exposed, which could lead to a stalled engine if the wire gets wet and the sensor malfunctions.
Tuesday, October 22, 2013
What Is a Friction Drive Belt

Friction drive belts, also known as V-belts, are used in a variety of automotive, agricultural and industrial machines that use pulley systems.
Function
Friction drive belts are used in mechanical systems that utilize pulleys to do their jobs. The friction drive belts, which are also known as V-belts because of their trapezoidal shape, are attached to a set of pulleys, and the friction of the belts against the pulley surfaces causes them to move, much like a gear or a chain system.
Significance
The unique V-shape of the friction drive belts is what increases their efficiency. The area where the belts make contact with the pulley surfaces are wider, allowing them to achieve more grip and better transmission of power. The tops of the belts are compressed more tightly to produce a more solid, durable "spine" that increases the overall strength of the belts.
Considerations
Friction drive belts transmit power purely through friction between the belts and the pulleys. Because of this, you should never make the mistake of lubricating them as you would a normal gear or chain system. Lubricating a friction drive belt system will only make the belts slippery, which will cause them to lose their grip and their efficiency.
How to Find Out What Anti Lock Sensor Is Bad
Most modern passenger vehicles use two or more anti-lock brake sensors to determine the rotational speed of the wheels. These sensors relay wheel speed information to the ABS computer and the powertrain control module, or PCM. The ABS and PCM computers use this information to calculate when to activate the anti-lock brake system, engage the traction control, retard the ignition timing and many other actions. When a wheel sensor fails, the on-board computers cannot gather information properly. In this situation, they disable one or more of these systems until the problem is remedied.
Instructions
- 1
Drive your vehicle to a safe location where you can perform an isolated road test. This could be a large, empty parking lot or a remote street without pedestrians and cars. Youll need to read a scan tool while the vehicle is moving, so its important to be in a safe testing location.
2Connect an ABS-capable scan tool to the vehicles diagnostic port and turn on the scan tool. Navigate to the ABS menu and select the Live Feed function. Your scan tool may have the Live Feed menu labeled as something different, but youll need to find the menu or setting that allows you to read the live data from the wheel speed sensors.
3Drive the car forward and accelerate to 15 miles per hour. Glance down at the scan tool and make sure that all of the wheel speed sensors show the same 15 miles per hour reading as the speedometer inside the vehicle. If one of the sensors shows 0, Zero or N/A, then that sensor is not providing the computer with a wheel speed value.
4Return home and park inside your garage. Turn off the engine and raise the end, front or rear, of the vehicle that has the bad wheel sensor. Support it with jack stands and chock the wheels on the opposite end. Apply the parking brake, if the opposite end is the rear of the vehicle.
5Crawl underneath the vehicle and locate the wheel speed sensor that wasnt responding. Use a work light to inspect the wiring harness and for cuts, frays and other damage.
6Disconnect the wheel speed sensors electrical connector and turn the ignition to the ON position. Measure the voltage at the sensors electrical connector with a digital multimeter. Look up the specified value in a service manual and compare that to the value on your digital multimeter. If the value is correct, and the wires arent frayed or damage, then the sensor is bad and must be replaced.
How to Reset the Service Engine Soon on a 2002 Suburban

To reset the "Service Engine Soon" light that appears on the control panel of your 2002 Chevrolet Suburban, you need to buy a scan tool from your local auto-parts store. The light should only be reset after you have serviced your engine, unless it goes on for some other reason such as from a loose gas cap. The scan tool is very affordable, quick and easy to use. It interacts with the vehicles computer to read the error codes helping you to diagnose other problems and reset and turn off the light after you have read the codes and fixed the problem.
Instructions
- 1
Look for the diagnostic connector port under the drivers-side dashboard between the center console and the steering wheel.
2Affix the scan tools connector to the diagnostic connector on the vehicle.
3Turn the ignition key to start the car. Select "Read" on the tool and wait for the codes and their corresponding diagnoses to appear on the screen of the scan tool. Write down the codes and their diagnoses on a piece of paper.
4Erase the codes by pressing the button that says "Erase" (different scan tools will employ different words). This will clear the codes and turn off the "Service Engine Soon" light. Turn off the car and remove the scan tool.
How to Replace the Coolant in a 2005 Mini Cooper

Coolant is an important regulator of engine temperatures. Coolant is a mixture of glycol and water. The chemical solution is able to withstand temperatures that would boil pure water, cooling an engine when its running; yet it also resists freezing, remaining a liquid when the engine is off overnight in severely freezing weather. You can purchase automotive coolant at any auto parts shop and most general retailers. Replacing the coolant in a 2005 Mini Cooper is a simple process. Check your Minis coolant levels regularly, and add when necessary.
Instructions
- 1
Park the Mini Cooper on a level surface and turn off the engine. Pull the hood latch inside the cabin, then get out an open the Mini Coopers hood. Let the engine cool before continuing.
2Loosen the coolant tanks cap slightly. The coolant tank is located behind the radiator. Do not remove the cap, just loosen it so excess pressure can escape. Wait a couple of minutes, then remove the cap completely.
3Check the coolant level by seeing where the liquid fills the tank. If the liquid is below the MIN line, youll need to add coolant.
4Add coolant to the coolant tank until the coolant level reaches the MAX line. Do not go fill the tank with coolant past the MAX line.
5Place the cap back onto the coolant tank and tighten it firmly. Close the hood of the vehicle.